New Plant Answers the Call to Compete Globally
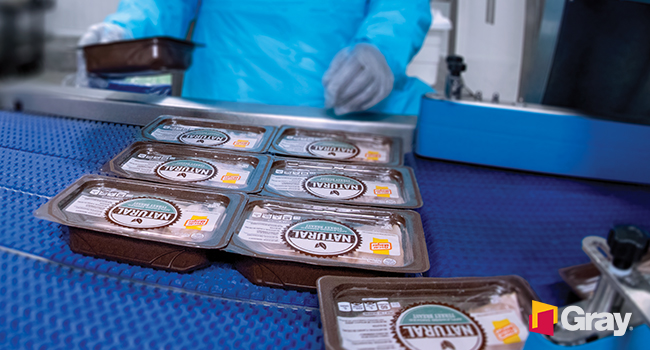
In Numbers
- Davenport, IALocation
- 382,157 s.f.Square Footage
- 14 monthsOperational
How a new Kraft Heinz facility provides what customers want and the market demands
Significant changes in consumers’ demands and rapid advances in technology are making this a most unpredictable time to be in the food manufacturing business.
In order to stay competitive, big food manufacturers are racing to provide what customers want by enhancing and expanding their own product lines and acquiring other brands that serve niche markets.
Dave Donnan, partner with A.T. Kearney, a global management consulting firm, told Area Development magazine that his company’s research found grocery store shoppers “are buying more in the perimeter area such as the deli, prepared foods, meat, and dairy as they seek fresher and healthier eating; center aisles where you find dry and packaged goods are experiencing losses.”
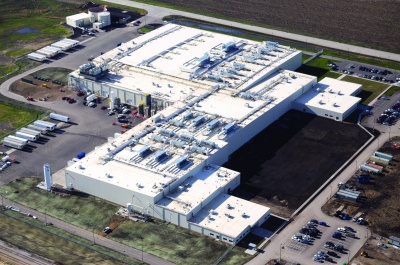
Continuing advancements in automation are helping manufacturers cut costs. For example, when CMC Food built a new production facility in New Jersey, it invested in egg-handling robots that could put 144,000 eggs on pallets per hour.Even as manufacturers face changes in the types of products consumers demand, they also must respond to rapid technological progress in labor-saving and supply chain tracking equipment. It’s compete or starve: if your competitors are saving money with more efficient production at their plant, you had better upgrade yours.
“In the past, the workers would have to feed 10 dozen eggs at a time into the machine and also stack the finished boxes at the end. Now the robots handle the heavy parts,” Michael Culley, CMC Food’s president, told CNBC.
Kraft Heinz finds itself in this competitive environment. Its Oscar Mayer products had been produced at a plant in Davenport, Iowa, since 1946. But after Kraft Foods Group and H.J. Heinz Co. merged in July 2015, the company conducted an extensive review of its North American manufacturing footprint. The conclusion: a new, state-of-the-art facility able to produce a variety of Oscar Mayer deli meat products in Davenport was in order.
In an article earlier this year, The Wall Street Journal described how at the older plant, “workers drove forklifts loaded with giant vats of ham, turkey and chicken parts on and off freight elevators,” while it would take “four rides between floors” for a turkey breast to be processed from raw meat into slices.
As part of the $1.5 billion Kraft Heinz invested over the past couple years to upgrade its global manufacturing plants, the company spent more than $225 million on a new facility in Davenport, located on 70 acres in the Eastern Iowa Industrial Park, about 10 miles away from the older plant. As part of this greenfield project, Kraft Heinz built in modern innovations in safety and technology by moving all processes to one floor; separating raw and ready-to-eat products; and integrating Rockwell Automation software into the process and refrigeration controls.
Construction of the 382,000-s.f. facility took 14 months from foundation to first production.
Answering consumer demand for natural ingredients, the new plant’s 12 packaging lines are producing Oscar Mayer products that are distributed across the United States. These include Deli Selects, Natural No Antibiotics Ever line of deli meat, and Naturals — whose packaging features “NATURAL” in large block letters and promises the absence of artificial ingredients, preservatives, flavors and colors. The plant also produces a significant portion of the total U.S. Oscar Mayer Deli Fresh meat volume.The plant’s design was deliberately aimed at keeping it competitive for years to come, with flexibility built into its design and layout.
In another feature that meets the goals of both saving money and satisfying consumers’ desires for social responsibility, the new facility uses significantly less water, because of increased efficiency.
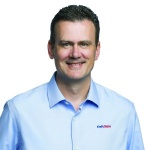
Additional sustainability features in the new plant include:This fits with a companywide goal of reducing overall water use of 15 percent by 2020, said Michael Mullen, senior vice president of Corporate & Government Affairs.
- LED-based lighting, which requires less power and increases reliability.
- Windows, air conditioning and HVAC units that largely reduce energy consumption.
- A pretreatment system for wastewater that is discharged into the local sewer plant.
- Non-greenhouse and non-ozone depleting refrigerants.
- Buffalo grass in the facility’s retention basin to help filter water.
In Davenport, new technologies and optimized processes drive decreased energy and resource consumption. While not LEED-certified, the new facility’s windows, air conditioning, HVAC units and LED lighting significantly reduce its energy consumption. It will use less water than the previous factory because it’s significantly smaller and is more efficient.
This investment is positioning Kraft Heinz to compete more effectively in a rapidly changing marketplace — and for the long term.”The $1.5 billion-plus we spent over the past couple years upgrading our global manufacturing facilities – including the one in Davenport – was done to enhance our capacity for innovation and product quality,” said Mullen. “In 2016 alone, we at Kraft Heinz increased our capital investment in quality by 45 percent.”
Some opinions expressed in this article may be those of a contributing author and not necessarily Gray.
Related News & Insights
Food & Beverage, Design
Kraft Heinz and Gray Construction Awarded Food Engineering Honors
Corporate News
April 11, 2018Food & Beverage, Architecture
A Foundation of Safety and Efficiency
GrayWay, Industry
Food & Beverage
Gray Project Receives Manufacturing Innovation Award
Corporate News, Industry
December 04, 2024