Automation: Redefining Food Processing
Modern food processing plants on the scale of Clemens Food Group’s new Michigan facility are pioneering advances in automation for many crucial reasons. Specifically, automation helps standardize and improve processes, which helps increase product throughput, reduce labor costs, establish and maintain elevated quality standards and improve workplace safety. Benefits include meeting accelerated delivery dates, better utilization of capital budgets, improved material flow and a more efficient plant footprint.
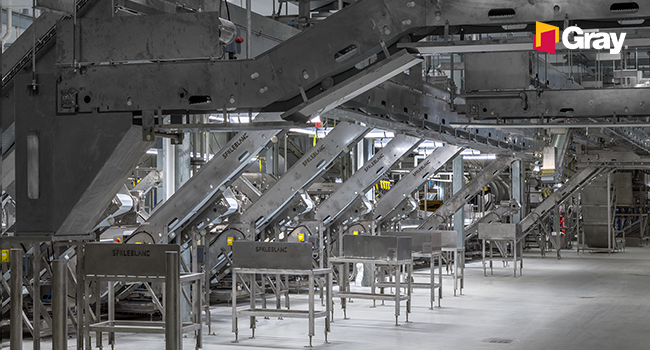
In Numbers
- Coldwater, MILocation
- 645,826 s.f.Square Footage
- 34 monthsOperational
Higher Food Quality, Improved Worker Safety
Roughly half the respondents to Food Engineering magazine’s 2017 State of Food Manufacturing survey say automation is once again considered to be the most impactful trend that will affect manufacturing operations over the next five years.
“Processors need to fully understand their operations and gain insights from a floor perspective,” points out Debra Schug, editor-in-chief of Food Engineering magazine. To do this, capturing and analyzing the correct data is essential. More companies are leveraging cloud technology, as well as employing more Industrial Internet of Tings (IIoT) solutions to obtain the kind of real-time data that drives key improvements and optimizes production capabilities. Some 80 percent of survey respondents expect their respective company locations to purchase process control hardware/software in 2017, with PLCs (programmable logic controllers) being the most likely item purchased.
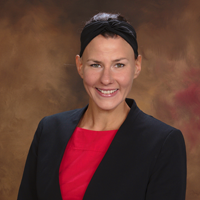
Getting Hip to HIMP
Improved data collection is key to new government reporting guidelines. The Food Safety and Inspection Service (FSIS) of the USDA uses Hazard Analysis and Critical Control Points (HACCP) as a framework for inspecting food processing plants for safety and food quality. As part of a new Modernization of Pork Slaughter rule passed last year, the USDA started a pilot program called HIMP, or the HAACP Inspection Models Project. According to Dan Kovich, deputy director of science and technology at the National Pork Producers Council, “HIMP is an inspection system under which packing plants take greater responsibility for carcass inspection, with FSIS employees ensuring the effectiveness of these activities as well as focusing on other food-safety verification tasks.” Currently, five U.S. pork packing producers (including Clemens Food Group) are participating in a HIMP pilot project. Enactment of a modernization rule will make this system available to all packers.
Whether for reporting purposes or improved process efficiency (or both), automation advances are prevalent throughout the new Coldwater facility. “This is the first greenfield fresh pork processing facility built in this country in the last ten years,” says Doug Clemens proudly. “Any kind of process improvement for higher efficiency or improved safety has been put into this plant.” These include:
- A sophisticated automated storage and retrieval system (AS/RS) that improves material handling and worker safety
- Automated scaling and sorting systems to assure products meet precise weight requirements
- Variable Retention Time Freezer (VRT) incorporated into the freezing process to increase efficiency and production, decreasing the typical meat-freezing process from a three-day waiting period to less than 24 hours – all optimized according to specific product and case sizes
- A patented equilibration cooler system for better control of carcass shrinkage and extended shelf life
- Waterjet cutting for improved processing of pork bellies for more precise cuts and higher yields
Automation not only helps Clemens Food Group with compliance reporting, it also serves a growing need to provide more information on their food to people across many demographics. From local sourcing to antibiotic use, people hungry for information will be satisfied.
Some opinions expressed in this article may be those of a contributing author and not necessarily Gray.
Related News & Insights
Manufacturing
Redefining Automation: Moving Manufacturing Jobs Forward
Industry
Distribution, Construction
Clemens Food Group Holds Ribbon-Cutting Ceremony for Fresh Pork Processing Facility
Corporate News
July 31, 2017Manufacturing
Greenfield versus Brownfield: The Experts Weigh In
Industry