Greenfield versus Brownfield: The Experts Weigh In
One of the toughest (and most important) decisions in the site-selection process is greenfield versus brownfield. Which offers greater immediate advantages and long-term benefits: a net-new site or one that has been previously developed?
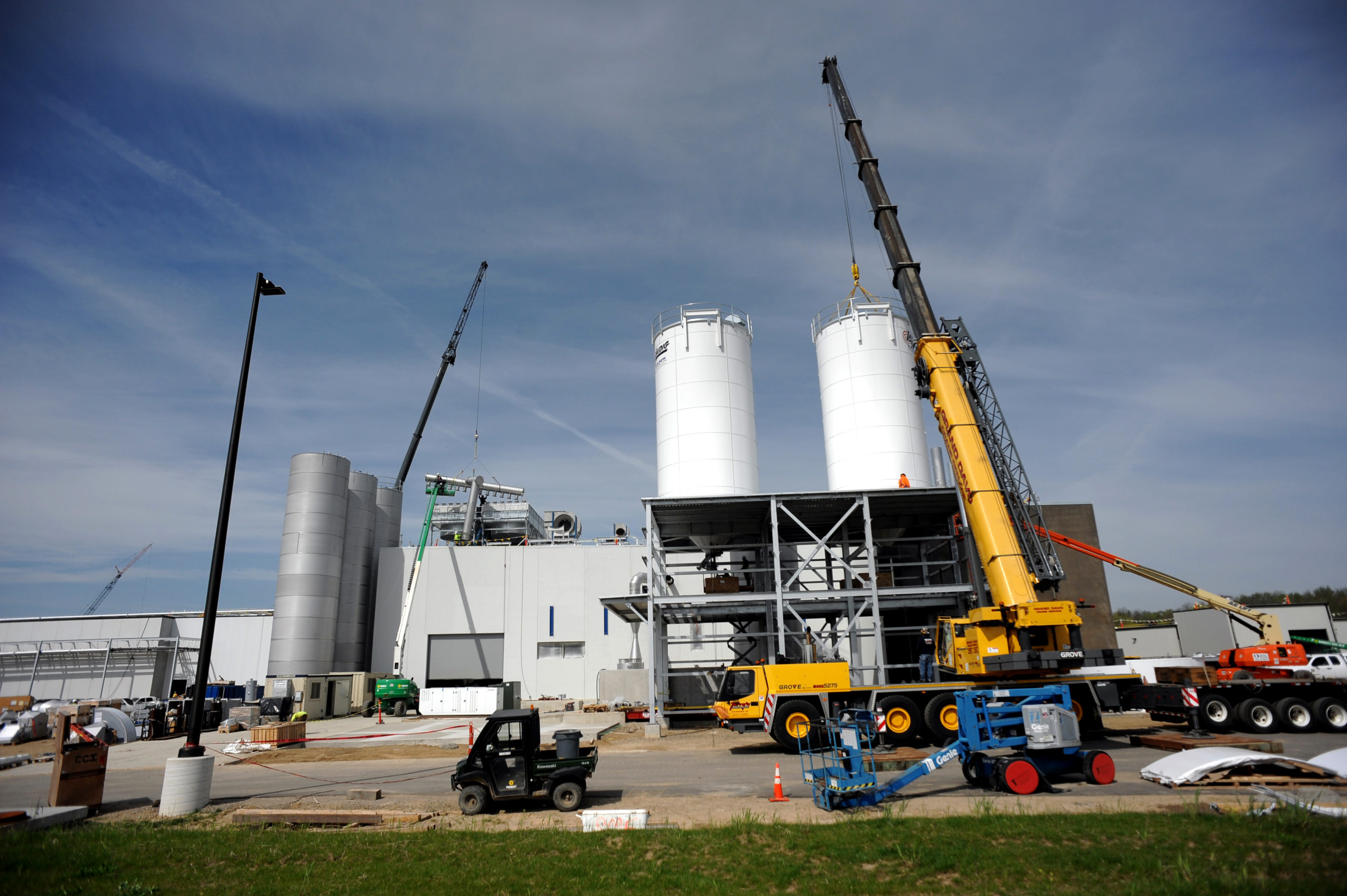
We asked Paul Kornman, senior project manager for Gray, and Brian Fain, senior vice president of Gray AE, for their insights into this complex question. Paul and Brian offer a combined 50 years of construction management experience and have overseen many key projects for customers such as Mercedes-Benz, Siemens, and Caterpillar.
What are some of the top advantages of having a greenfield facility?
Kornman: The advantage of greenfield is being in control of your destiny. There is no history of how a previous plant operated, no skeletons in the closet, so to speak. The new project is built for the intended use and tends to attract a larger labor force, as new facilities often offer better ergonomics, welfare spaces, and other benefits.
Fain: A greenfield site also allows for the incorporation of the latest technology and innovation from the outset, which contributes to enhanced operational efficiency and competitiveness. All infrastructure, from utilities to building materials, is new, reducing maintenance costs and potential downtime associated with older infrastructure.
What are some of the advantages for a brownfield?
Kornman: The immediate advantage is lower capex cost and existing utility infrastructure. Brownfield facilities possess the unique advantage over greenfield facilities in that they are pre-equipped with certain needed aspects for the project. With a greenfield facility, we’re starting from dirt.
Fain: Existing infrastructure such as roads, utilities, and sometimes buildings or structures that can be repurposed or renovated. Brownfield sites are often located in established industrial or commercial areas, providing proximity to markets, suppliers, and a ready labor force.
What industries are best-suited for greenfield and brownfield sites?
Fain: Greenfield projects are particularly well-suited for industries and markets that require flexibility, customization, and the integration of cutting-edge technologies. These include tech startups and data centers, biotechnology and pharmaceuticals, manufacturing and industrial production, and logistics and distribution.
Kornman: Brownfields generally lend themselves better to manufacturing and distribution, as the original buildings were likely built for that type of process. Industries that tend to select brownfields include urban redevelopment and mixed-use developments, commercial real estate and office spaces, residential housing and affordable housing initiatives, and brownfield industrial parks and manufacturing centers. What was once a greenfield manufacturing facility could make for a very nice brownfield manufacturing facility years down the road.
Everyone wants speed when building their facility—what are the speed-to-market factors for greenfield and brownfield facilities?
Fain: Speed-to-market is a critical factor for both greenfield and brownfield facilities, albeit with different considerations due to their distinct developmental contexts. Due to the complexity of building a new facility completely from the ground up, greenfield projects typically require particular attention around planning, efficient execution of construction and regulatory processes, and strategic technology integration to optimize time-to-market outcomes effectively.
Kornman: For the right brownfield investment, speed to market can be faster than a greenfield project. Permitting is likely less of a challenge and modifications to the existing structures would be limited. If the process is complex or somewhat new (perhaps automation-dependent), the viability of a brownfield may be less due to the amount of modification that would be required, making a greenfield a better choice.
Fain: Environmental considerations also impact speed to market. Greenfields generally involve less environmental impact initially, but may require compliance with environmental assessments and regulations. Brownfields must address any existing contamination or environmental hazards, which requires thorough assessment, remediation planning, and compliance with environmental standards.
What are some common mistakes that companies make when considering the greenfield/ brownfield decision?
Fain: A common mistake is underestimating environmental and regulatory challenges, such as assuming that environmental remediation and regulatory compliance will be straightforward or less costly than they actually are. Companies may underestimate the complexity and time required for environmental assessments, remediation efforts, and obtaining necessary permits for brownfields. For greenfields, companies may not consider potential environmental impact assessments and regulatory hurdles associated with developing on pristine land. Failure to account for these factors can lead to delays, additional costs, and legal challenges.
Kornman: Another mistake is insufficient master planning, especially regarding room for expansion. Very seldom does anyone engage in a project without the hope of growth. For example, with a brownfield, you build the process around the building. This usually means expandability or flexibility is reduced, which puts a cap on growth.
Fain: Companies have a tendency to overlook total cost of ownership (TCO) considerations. For greenfields, this means focusing solely on upfront costs such as land acquisition and construction expenses without considering long-term operational costs. This includes utilities, maintenance, and potential future expansion costs, which can be significant for greenfield developments. For brownfields, companies may not accurately assess the total cost of remediation, infrastructure rehabilitation, and potential ongoing maintenance expenses associated with older or deteriorated infrastructure. This can lead to budget overruns and unforeseen costs.
Conclusion
Avoiding these mistakes requires careful evaluation, strategic planning, and consulting with experts in environmental remediation, regulatory compliance, real estate development, and construction management. By addressing these and other key factors proactively, companies can mitigate risks and make informed decisions that align with their business objectives and maximize project success.
There are clear advantages for both greenfield and brownfield facilities. Both types of projects have clear use cases where one is more advantageous than the other. So, which is right for you and your business? That’s the million dollar – or in most cases, millions of dollars – question. To answer this, you must evaluate your business, your need, your location, and numerous other factors that all help determine which fix is right. One thing is sure, whether you need a new greenfield facility or a renovated brownfield project, Gray has the expertise to help you.
- Category:
- Industry
- Manufacturing
- Food & Beverage
Some opinions expressed in this article may be those of a contributing author and not necessarily Gray.
Related News & Insights
Manufacturing, Construction
Greenfield vs. Brownfield: What’s Better for Your Manufacturing Facility?
Industry
Food & Beverage
Gray Project Receives Manufacturing Innovation Award
Corporate News, Industry
December 04, 2024Advanced Technology, Automation & Controls
Four Use Cases for AI's Growing Role in Manufacturing
Industry
November 25, 2024