These Workforce Development Programs are Tackling the Manufacturing Skills Gap Head-on
Manufacturing has come back from the Great Recession. Although production is up for many manufacturing companies across a range of sectors, a stubborn problem remains that is preventing even greater recovery and expansion—a lack of skilled workers.
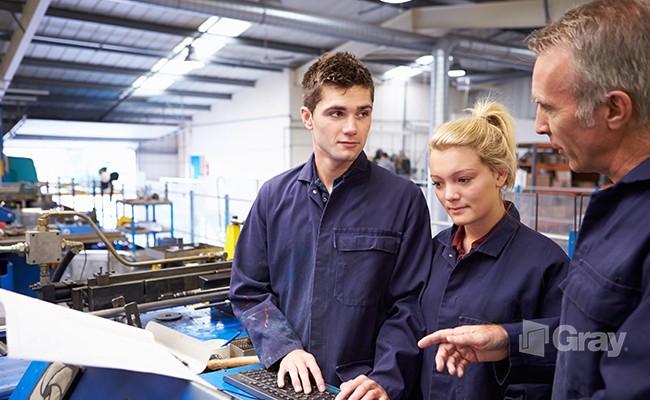
U.S. manufacturing supports about one in six American jobs. However, over the next decade, 2 million manufacturing jobs will go unfilled, severely limiting expansion. This is the result of the widely reported skills gap, where there are not enough trained workers with the technical skills needed to step into these jobs.
“There is a pressing need for workers who either already have the skills needed to manipulate the sophisticated equipment, or the aptitude to learn from the fast-retiring baby boomers to get proficient on the job,” states Swiss Machining Precision in a recent blog on its website.
As a result, the availability of a stable and skilled workforce is the number-one concern of companies when locating new operations, or expanding existing ones.
State Development Teams Step Up
After the Great Recession, states are more competitive than ever for big corporate investments. They are working hard to craft tailored incentive packages that meet the specific needs of these companies. The first question is almost always labor—how can they provide companies with the skilled workers they need to land these projects? One key incentive is providing workforce development programs at little or no cost to companies—both those looking to come to the state, as well as those that want to remain and expand. Increasingly, state economic development teams handle recruitment, customized training assistance, and training incentives—all at no cost or low cost, providing certain job creation/retention benchmarks are met.
Workforce training and development is a significant part of overall labor cost and can be a critical factor in site selection. This is especially strong in the South, where comprehensive, innovative, and customized workforce training programs have been attracting big manufacturing projects for decades. Top programs include:
Quick Start, Georgia
Providing comprehensive training programs through the state’s technical college system, Quick Start is well-known for its “can do” attitude. For example, when Hyundai announced plans to build a manufacturing plant in West Point, Quick Start developed a highly customized training program for its new workers. Before plant construction was finished, Quick Start built a simulated conveyor system and production line at its training facility to start training these new employees.
Kentucky Skills Network (KSN)
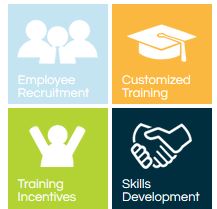
This agency delivers flexible, personalized workforce services to both new and existing businesses within the state. According to its website, KSN has provided training to over 4,000 companies and 84,000 Kentuckians across a variety of industry sectors, including manufacturing, healthcare, information technology, energy, distribution, and research and development.
FastStart, Louisiana
FastStart provides customized employee recruitment, screening services, and training programs for new or growing companies. Founded in 2006, FastStart has served more than 150 expanding companies and provided over 337,000 hours of training to more than 23,800 workers since 2008. This job-training program has helped Louisiana attract new high tech industry and expansions—for example, IBM in Baton Rouge, GE in New Orleans, and startups like Gameloft in New Orleans.
With globalization and increased competition with lower-cost countries, it is paramount that the U.S. manufacturing workforce has the skills it needs to compete. More state economic development departments are working closely with corporate representatives to assess their training needs. Each corporate prospect is unique and requires workforce solutions that are customized for a unique timeline, proprietary processes, and/or specific performance results. This can also expand economic development opportunities in rural areas by designing training programs through community and technical colleges.
“It is getting harder to rank the leaders in workforce training because so many states have finally gotten the message that workforce development is job one in the U.S.,” says Jack Rogers, editor-in-chief for Business Facilities, which recently ranked FastStart as the nation’s top state workforce training program for the seventh consecutive year. “As a result, more states are aggressively acting to close the critical gap in skilled workers.”
- Category:
- Industry
- Manufacturing
Some opinions expressed in this article may be those of a contributing author and not necessarily Gray.