America’s Promise to Fund Manufacturing Education
Beginning October 1, thousands of people who want to gain advanced manufacturing skills will be eligible for two years of free college. That’s America’s Promise, a feature of the President’s 2017 budget announced in April. It was funded in June when regional coalitions were invited to apply for grants of up to $6 million each. The winners will be announced in October and the wheels will start turning to prepare future members of the manufacturing workforce.
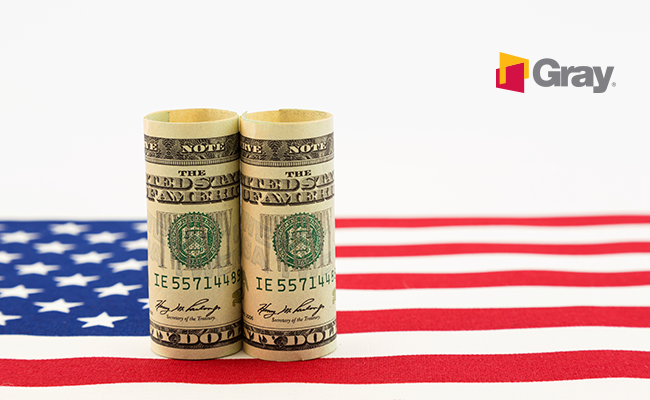
Good as far as it goes, but some hidden resources can do more for manufacturers.
What America’s Promise means
These America’s Promise Job Driven Training Grants are going to 20 to 40 broad-based coalitions that will build tuition-free programs, not directly to students.
Understand that America’s Promise Job Driven Training Grants aren’t blank checks from the government and will not go directly to students. They are going to 20 to 40 broad-based coalitions that will build the tuition-free programs. The partnerships include employers, economic development agencies, workforce development boards, community and technical college as well as K-12 education systems and other community-based organizations.
An example of one of the hopeful applicants is the Michigan Coalition for Advanced Manufacturing (MCAM). It includes eight community colleges spanning the state that are helping grow a workforce with skills in welding, machining, mechatronics/maintenance and manufacturing production/assembly. MCAM’s community college members are working with local manufacturers that realize they are competing for the same talent in a shrinking pool. They know that making the pool bigger will be better than trying to hire employees away from each other.
What is the role of the manufacturing employers in the coalitions? They will help shape the program by identifying the skills and competencies they need, whether it’s in renewable energy technology, 3D printer operations, computer numeric control (CNC) machining skills or some other trade. They will also contribute by offering apprenticeship, paid work experience and paid internships. The payoff for being part of the coalitions is a stronger pipeline of qualified people to run their operations.
Alternative methods of help for manufacturers
Waiting for America’s Promise won’t help most manufacturing employers, but fortunately, there are more grant sources. These grants aren’t easy to find and not generally easy to apply for or manage. However, this is when manufacturers manufacturing employees should turn to the workforce development departments of local community colleges.
When it comes to grants, community colleges can hold the center of a virtuous circle. They can perform skills’ assessments for companies, work with them to develop a training plan, tap grant funding sources on behalf of the company and write professional grant proposals. They often take on another headache – managing a grant and fulfilling reporting requirements, which would require time and skills a manufacturer doesn’t want or have. In the end, everyone wins — the manufacturer gets the funds, it pays the community college for delivering training and workers gain valuable skills.
How to approach grant offers
What can manufacturers do to get started with this approach to training? Since not every community college has the same resources, it is important to look at several systems in your region. Ask about the workforce development department, which will be separate from the academic programs. When you speak to the department’s representative, you will be able to learn how much they can help you. Then, meet with the administrators and instructors to assess their people and programs. Some important questions to ask are:
- Where do you find grants, and who handles applications and reporting?
- If you must share costs, find out how paid work time or machine time used during training (known as “in-kind” support) can take the place of dollars.
- What are your responsibilities, and what is the college responsible for?
- Do you minimize the time your employees are away from their work by delivering training on site or online?
For examples of a couple of community colleges with assistance for getting workforce training grants, check out:
- Macomb Community College, Grant Supported Job Training
- Wisconsin Indianhead Technical College, Grant Funding Available for Training
While you are finding out about community college resources for manufacturers, don’t forget to look into their core manufacturing education programs. When you get connected with instructors and graduate placement programs, you forge early relationships with new manufacturing talent you need.
The need for skills development in the manufacturing workforce of the future is widely recognized. The most recent issue of the GrayWay looks at this challenge and highlights what organizations such as SkillsUSA are doing to remedy it.
The skills gap challenge has received much support, but it’s fragmented. By reaching out, however, manufacturers can probably find a community college prepared to put the pieces together.
Karen Wilhelm has worked in the manufacturing industry for 25 years, and blogs at Lean Reflections, which has been named as one of the top ten lean blogs on the Web.
- Category:
- Industry
- Manufacturing
Some opinions expressed in this article may be those of a contributing author and not necessarily Gray.
Related News & Insights
Manufacturing
Why Increased Education Funding is Critical to Our Nation…and Manufacturing
Industry
Manufacturing
Can a Narrow Focus on Labor Productivity Block the Big Manufacturing Picture?
Opinion
Manufacturing
Why Consistent Near Miss Reporting is Crucial to Any Good Safety System
Industry