The Industry’s Most Worker-Friendly Plant
Traditionally, working in a poultry processing plant for large tom turkeys can be challenging. The roles involved can take a physical toll on workers, requiring continuous lifting and other strenuous tasks. Prestage Foods had a vision to flip this narrative for its Camden facility and developed employee welfare initiatives to improve employee comfort and work-life balance while raising the industry bar for poultry processing facilities.
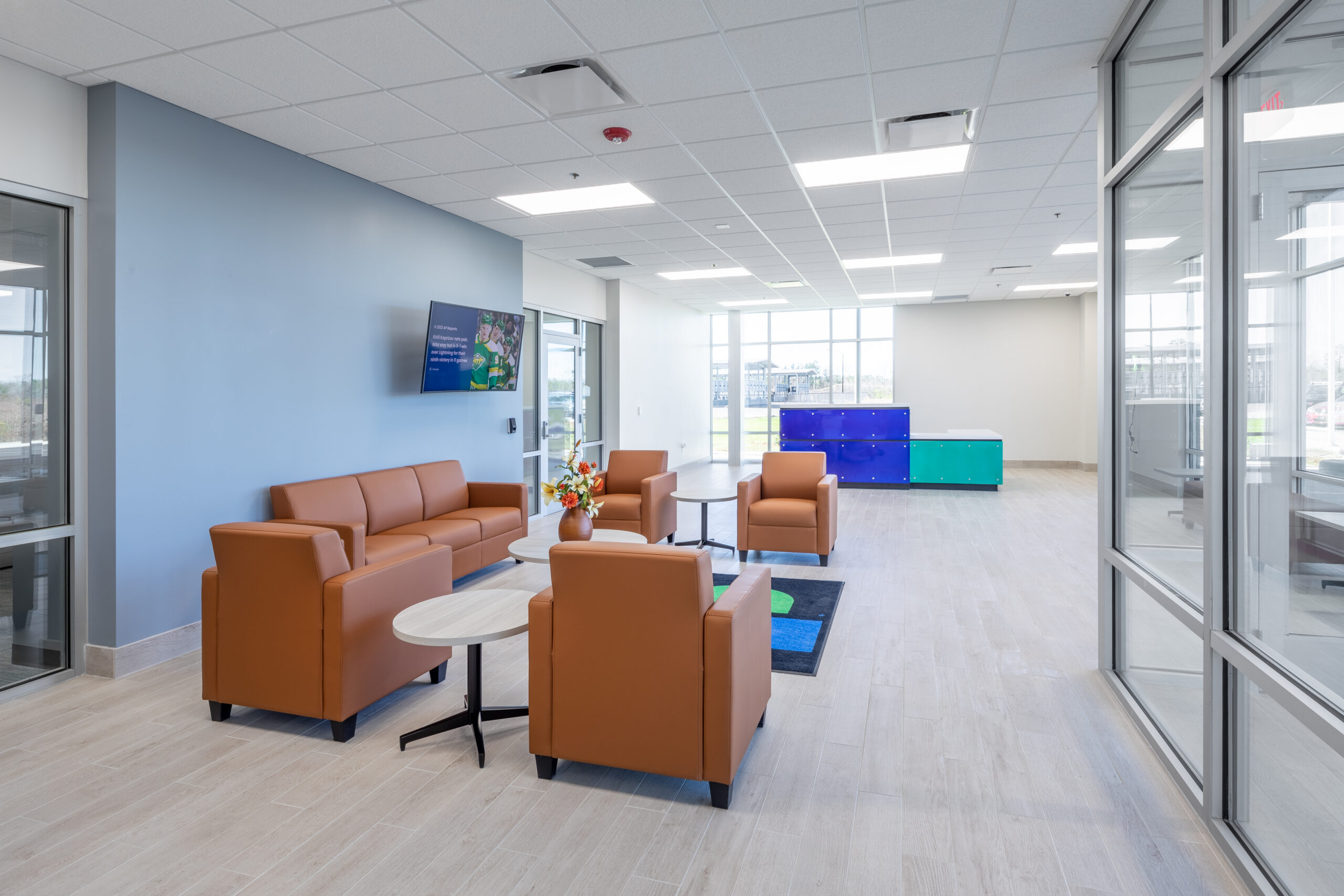
In Numbers
- Camden, SCLocation
- 295,000 s.f.Square Footage
- 16 monthsOperational
The most notable of these initiatives has been the implementation of an innovative production schedule. The company’s switch to an air-chill processing model, coupled with creative operational shift planning, has allowed Prestage to adopt a 4/10 single-shift facility that offers all production employees a four-day work week. First processing works 10-hour shifts Monday through Thursday. The second processing team works 10-hour shifts Tuesday through Friday deboning and packaging products. This system rewards hard-working employees with the freedom and flexibility to enjoy long weekends year-round and results in considerable savings on labor and utilities.
With first and second processing departments operating only four days a week, Prestage can reduce the number of required cleanings while still maintaining maximum sanitation and food safety. This operational model drastically reduces the volume of water and sanitation chemicals needed for the plant’s weekly cleaning cycle. Prestage Foods is proud to be the first turkey processing facility in the country to adapt a 4/10 shift model, and early results have yielded extremely positive feedback from employees and potential hires.
In addition to scheduling changes, Prestage has fully leveraged automated technology to reduce or eliminate the most physically demanding aspects of the operation. Automation in the plant’s evisceration stage was especially impactful. Traditionally, this process can be difficult to keep fully staffed, as manual processing requires team members to lift birds weighing up to 50 pounds for extended periods of time. The newly installed equipment offers advantages in staffing employee ergonomics as well as functional responsibilities. With automated processing, evisceration is now a “no lift” stage for employees. The business’s focus on automation solutions also radically transformed the cropping operation, eliminating a physically strenuous job and opening other opportunities for team members. Using conveyors designed and installed by AD Process Equipment, a Gray company, Prestage ensures that eviscerated parts are automatically conveyed from the production line to the next stage without the need for workers to manually move totes.
To attract the best and brightest employees in the region, Prestage Foods placed special emphasis on employee welfare in the plant’s design. Employee facilities feature a spacious layout, easily flowing traffic patterns, large indoor and outdoor break areas, personal storage lockers, and self-service vending. In addition to promoting optimal food and occupational safety, Prestage Foods’ use of automation and segregated process areas eliminates the need for employees to be stationed in less desirable processing areas, such as onsite wastewater.
Together, these team-focused initiatives reveal that using technology and innovative thinking to stay ahead of the game isn’t just good for the bottom line—it’s good for those responsible for making the business successful day in and day out.
Related News & Insights
Food & Beverage, Construction
Revolutionary Processing Model Vaults Prestage Farms to the Top of the Industry
GrayWay
Food & Beverage
Gray Project Receives Manufacturing Innovation Award
Corporate News, Industry
December 04, 2024Advanced Technology, Automation & Controls
Four Use Cases for AI's Growing Role in Manufacturing
Industry
November 25, 2024