Team Member Training in an Automated World
Training is a key component of any effective manufacturing operation, especially within the food & beverage market, but as more pieces of the production process become automated, they create new training challenges for processors who want to ensure their team members are staying up to speed.
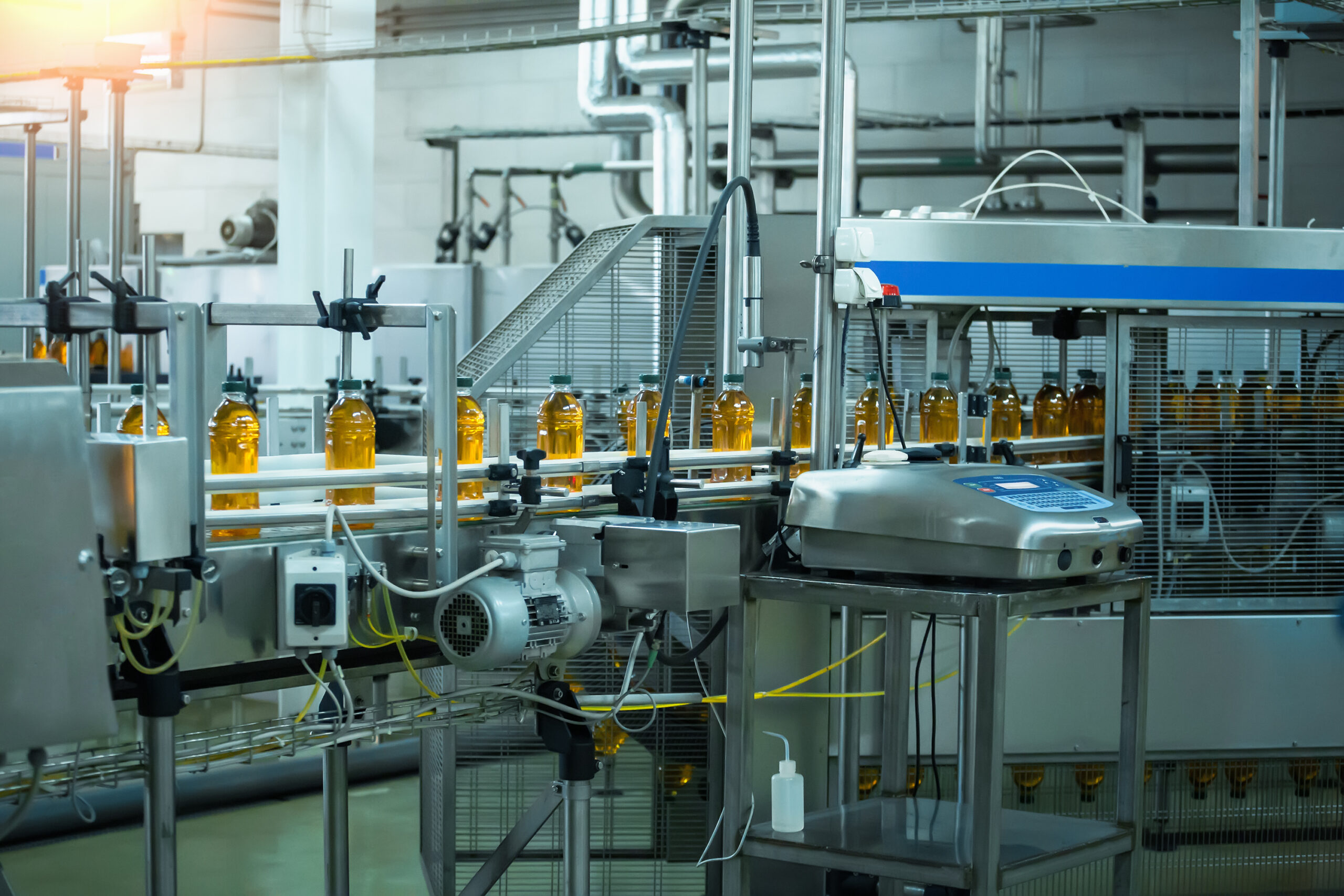
In many ways, adding automation to your facility eases the process, eliminating or simplifying several steps throughout production. But that doesn’t mean that a human operator isn’t needed — after all, an automated labeler can’t refill itself.
So, the question becomes how to successfully integrate automation into the production process while ensuring human operators are safe and capable. This requires a different approach where processors consider the capabilities and limitations of automation, team members’ comfort level with technology, and potential buy-in to training for improved—or altogether new—production processes.
Shifting the Paradigm
One of the biggest challenges of training in an increasingly automated world is encapsulated in a phrase that many processors dread hearing: That’s the way we’ve always done it. It is, at face value, generally a true statement. Breaking away from orthodoxy requires team member buy-in to new processes, as well as new training to understand and effectively carry out those processes. If you don’t have buy-in, you run the risk of team members looking for creative ways to circumvent the new process and do things the old way—which can lead to costly mistakes and downtime.
A key component to successful implementation is ensuring processes are explained from the bottom up rather than top down. While policy is necessarily set by management, it should be adaptable to the expertise and insights of front-line team members. Not only does this help with buy-in, but it also helps to ensure operational details aren’t missed. A veteran operator may be reluctant to change traditional procedures, but will likely have good insights on what is working, what isn’t, and how a process can be improved through automation. Those insights can shape training on new methods and equipment, contextualizing the role of automation within a complete operation.
Think of it this way: Do your managers understand every step of the production process, including the ones that the operators have effectively modified or streamlined to save time and resources? Or do your managers only understand when production is going well and when it isn’t?
One flavorings company decided to put this into action. The company made a decisive plan to place a significant value on training, including on-the-floor training, as opposed to classroom training. Internal audit teams walk the production floor, looking for areas where the process may not be as efficient as possible. When they find those instances, they can execute spot training, then follow up with scheduled training to reinforce what has already been taught.
Another way to identify potential training challenges is by including front-line production team members in production meetings to look at data and understand what it means for production. Data can tell you a lot, but sometimes it needs an operator’s eye to understand what it is really trying to tell you. Front-line operators help translate data into digestible information that trainees can use to deliver tangible production results.
One performance, snack bar company tackled the training challenge by identifying leaders in its workforce and involving them in the training development process. The company was switching from a traditional bakery to a data-driven process that included real-time production data to maximize efficiency and had a veteran workforce that was used to doing things a certain way. Instead of trying to implement a one-size-fits-all training program, the company sought input from the workforce to understand what the needs were, how to address them, and how to effectively build a training program that would incorporate team members’ insights on production.
The Tech Generation
While training for an automated process can be complicated compared to more manual processes, there is one big advantage that food & beverage processors have now: the generations entering the workforce have grown up with technology. A touchscreen control panel or monitoring system is second nature to team members who grew up with smartphones and tablets.
A technologically advanced workforce provides training advantages as well. Several software packages allow companies to develop their own personalized training based on production needs, and they can be quickly updated when new equipment or processes are put in place. Additionally, the technology available via videoconferencing, augmented and virtual reality, and more allows for advanced training options. With these tools, team members can experience training that puts them in a virtual production environment, even from off-site locations.
These technologies will be more comfortable for digital natives, but what about team members that are less tech-savvy? In some cases, these team members will be reluctant to change, which further highlights the importance of bottom-up training. Understanding team members’ level of comfort with technology and clearly communicating its benefits is critical to getting them to embrace new forms of training.
The New Normal of Training
Training in today’s highly automated world presents several challenges. Ultimately, the ability to communicate the need for new training is where the process really begins. As quickly as technology is evolving, so too must today’s workforce evolve to master it. This mastery comes through effective, production-driven training that gives team members the best opportunity to understand and effectively use new tools.
While food & beverage production will only become more automated as technology continues to offer new solutions, overcoming training challenges demands a time-honored approach: communicate effectively, achieve team member buy-in, and reap the rewards of a more effective workforce.
- Category:
- Industry
- Food & Beverage
Some opinions expressed in this article may be those of a contributing author and not necessarily Gray.