Strategies from the Front Lines: How Manufacturers Combat Opioid Addiction
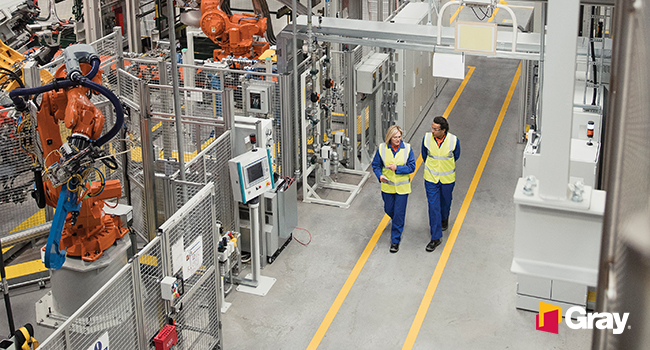
Manufacturing companies find themselves in a unique position. To attract skilled workers for precision tasks, manufacturers offer attractive prescription benefits – but those benefits can make manufacturers vulnerable during the opioid crisis.
According to a story in Crain’s Detroit Business, Nexteer Automotive’s Steering Gear plant in Saginaw, Michigan, worked with an investigative firm to place an undercover agent on the shop floor to investigate an increase in suspected workers’ compensation scams. A few hours into the agent’s first shift, the agent was approached to buy prescription opioids.
The scam, which has spread to a number of manufacturing facilities, goes something like this: A worker falls off a forklift and will get a prescription for, say, 50 Percocet tablets. Then, a number of employees take turns becoming injured to get prescriptions filled and supply each other. Selling pills on the side soon follows. The employer pays out workers’ comp and pays for the medication.
In short, the employer becomes the supplier.
At Nexteer, the investigation led to the firing of six employees and a switch from a fully insured health plan to a self-insured plan, Crain’s reported.
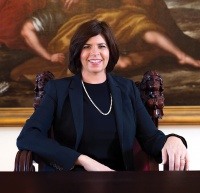
Assertive Apprenticing
At Warren Fabricating & Machining in Hubbard, Ohio, where at least four out of 10 applicants test positive for drug use, Regina Rebhan Mitchell, a co-owner, is fighting back by setting up an apprentice program that de-emphasizes experience and existing skills.
Training her own apprentices helps her do that, she said, by allowing her to choose solid candidates who want to learn their craft and improve their livelihood. They do not tend to miss work, come in late or leave early. At the same time, they are grateful for both the job and the training.“We need to get a handle on the opioid epidemic for the health and safety of our community,” she said. “The only power I have over this is to keep drugs out of our company by remaining a certified ‘Drug-Free Workplace’ from the State of Ohio.”
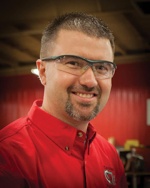
Learning responsibility related to drug usage is not isolated to a manufacturing workplace. It actually begins with education. Leading a student-run business that provides commercial work gives high-school teacher Craig Cegielski a chance to mold teenagers into ideal manufacturing employees. He makes a point of teaching the teens that a fulflling career in manufacturing leaves no room for drug abuse.
Remaking Manufacturing Education
“Every once in a while, an employee will leave to work for a competitor after we’ve spent time and money on their training,” Mitchell said. “The main problem with the apprentice program is that it is expensive to run. Often I pay two people to do one person’s job because our on-the-job training is so extensive. This makes it harder for us to compete for skilled workers, as we may pay $1 or $2 lower than other fabricating shops in our area.”

Every year delivers a different group of students. What they need from Cegielski varies, he said. “But there have been years when developing soft skills accounts for 25 percent of what we spent our time on.”Cegielski runs Cardinal Manufacturing, a student-run job shop in Wisconsin’s Eleva‐Strum school district focusing on ready-made apprenticeships and manufacturing career success. According to him, business is growing. “We now start the students in 7th grade so I get to see them for 6 years, which is even better,” he says. “Employers do not have 6 years to mold an employee. Schools have the time and need to prioritize working on soft skills and employability skills first, including the importance of drug-free workplaces. Then come the technical skills.”
- Category:
- GrayWay
- Manufacturing
Some opinions expressed in this article may be those of a contributing author and not necessarily Gray.