Resuscitating Supply Chains After COVID-19
Even before COVID-19 hit the U.S., American manufacturers were feeling the strain on their supply chains when the trade wars caused higher tariffs on imported and exported goods. With the onset and growth of the pandemic, supply chains for many products, including crucial medical supplies, suffered major disruptions, either by manufacturing being shut down in virus-stricken countries or by the refusal to ship overly needed supplies.
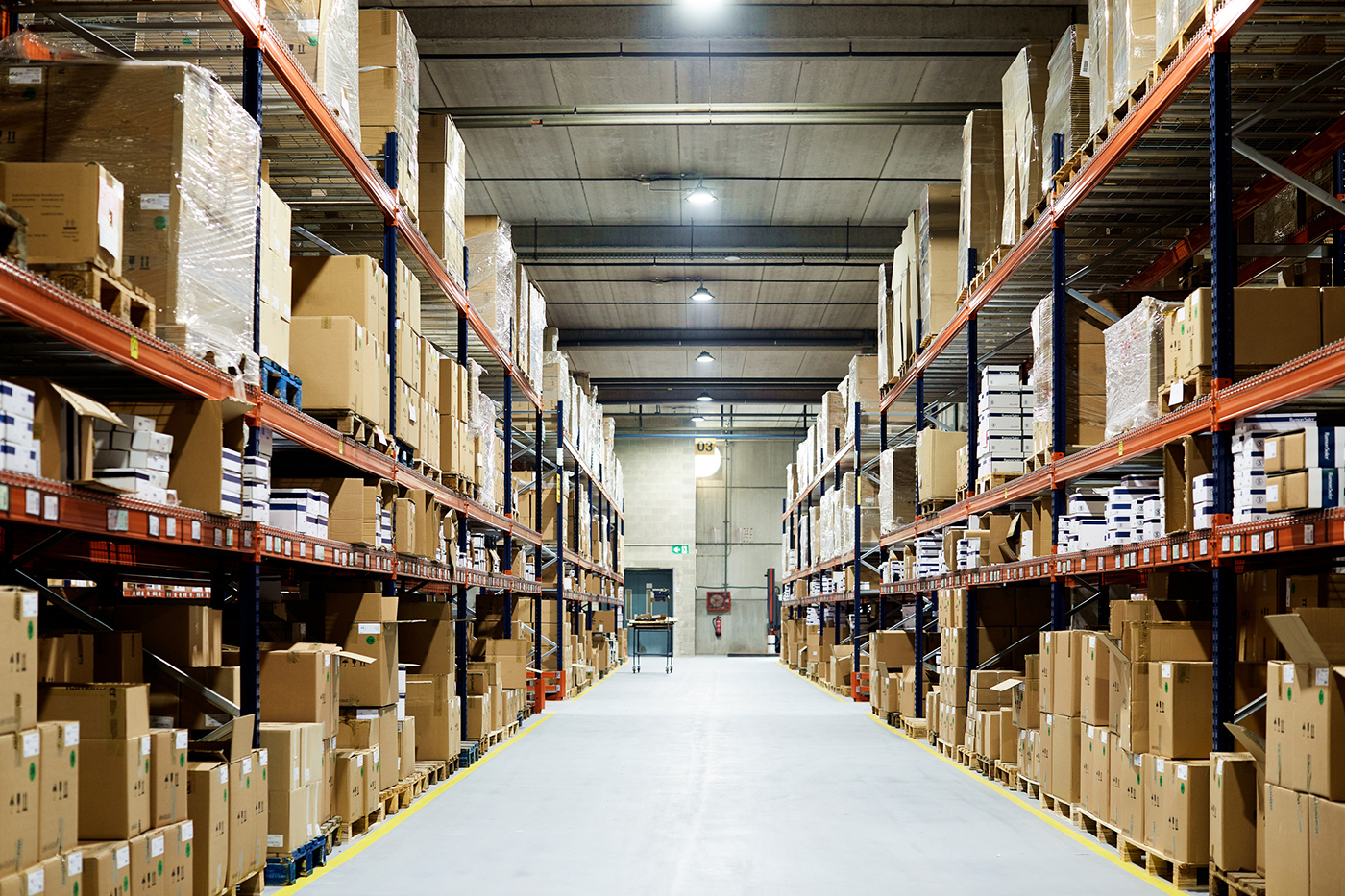
The National Retail Federation reports 40% of retailers and the National Association of Manufacturers reports 35.5% of manufacturers have experienced severe disruptions to their supply chains. These companies and others are analyzing their entire supply chains, not just their line to the customer. This includes analyzing the entire spectrum from the beginning of the product life cycle to the vendors that supply the resources for the product being made.
“As the crisis evolves, complexities and vulnerabilities in global supply chains, which extend beyond China’s central role in manufacturing and goods trade, are coming to the fore,” says Tim Ryan, U.S. chairman and senior partner at PwC.
Pandemic Brings Change
As the pandemic looms on, companies are scrutinizing every link in their supply chain to find over-dependencies and rigidities that make them vulnerable to current and future disruptions.
The positive takeaway from the COVID-19 crisis is that companies will benefit from greater transparency, including the demands and prices placed on the vendors, by assessing the best ways to make their supply chains as efficient and responsive as possible to changing economic conditions.
Flexibility and diversity to reduce over-dependencies on a single supplier, manufacturer, or country will come from collaboration with companies in similar industries to fill supply chain shortages or gaps when they arise. Larger companies will also downsize their global hubs in favor of smaller facilities in countries where the product is demanded the most—this helps keep the supply for that country flowing and cuts down on transportation costs and tariffs. For example, Coca-Cola is famous for partnering with 225 bottling plants around the world, where each plant bottles and distributes for its region. This model was in place before the pandemic started, and, for that reason, Coca-Cola saw less disruption.
The standard for the last few decades has been offshoring, with China as the top destination, and following just-in-time inventory management to keep costs down and profits up. Although suppliers are looking at moving away from China, it does not necessarily mean they will return to the U.S. Lower-cost and more stable manufacturing locations include Eastern Europe, Mexico, Thailand, and Indonesia, which can also support the idea of creating multiple manufacturing hubs instead of depending on one centralized area. However, these potential destinations are not without their own challenges, such as increases in tariffs and production costs. In addition, lower energy costs in the U.S. have increased an attraction for companies considering re-shoring back to the U.S. Sharing a common language, time zones, and easier travel all make communication and decision-making easier in times of a crisis, adds more luster to the idea of reshoring. Companies that invest in reshoring and help reindustrialize the U.S. will contribute to the prosperity of the country during a time of great need.
Thriving in Uncertainty
Once COVID-19 runs its course, manufacturers will have made significant technological improvements to their supply chains that increased performance, efficiency, and, most of all, reduced risk—improvements they will likely keep. Blockchain technology, already in use by global companies like Walmart and Coca-Cola, will be implemented by more companies to reduce the duration of order reconciliation and give real-time insights into the thousands of transactions made by all vendors in the supply line.
As new COVID-19 cases rise, the timing of when facilities working at full capacity of production and labor is still uncertain. With concerns over future disruptions, extreme workforce, and HR challenges can also be alleviated with technology. For example, 3-D printing, robots, and automation can be expanded if labor falls in short supply or is unable to be onsite and must work remotely.
One of the highest priorities for companies is to have a system of reliable back-up vendors for goods and components when the primary supply flow is disrupted. This redundancy will create flexibility to respond efficiently to future disruptions.
AGCO, a global agricultural equipment manufacturer, weathered the first wave of the pandemic with minimal disruption to its business. With a system already in place for risk assessment, data analysis, and constant communication with every manager as well as primary and back-up vendors, the company was prepared with PPE and safety protocols in place to protect workers, determine which vendors could handle increased demand, and alternative modes of transport mapped out.
Redundancy in vendors and suppliers used to be viewed as a cost-prohibitive action of limited value for a supply chain; that ability now, however, is saving the day, keeping manufacturers in operation and workers employed. For example, when one vendor was forced to shut down, AGCO turned to their second-tier vendors to fill the demands. When shipping via cargo ships was disrupted, AGCO pivoted to analyze the comparative cost of air-versus-land and shipped their product across Russia via trains. Although it cost more, it kept their supply chain flowing and met their ‘customers’ demands.
The post-COVID-19 future and recovery are unstable—not in the sense of whether we will get through this—human beings are dynamic and creative. There will be a future that we can look back at the end of COVID-19. When it comes to how we do business and how things are made, that will be a different landscape. The manufacturers that survive, or are born from this pandemic, will be the ones that learn that supply chains are similar to any living organism; that they must stay flexible, adapt, and diversify to thrive.
- Category:
- Industry
- Construction
- Manufacturing
Some opinions expressed in this article may be those of a contributing author and not necessarily Gray.
Related News & Insights
Advanced Technology, Automation & Controls
Four Use Cases for AI's Growing Role in Manufacturing
Industry
November 25, 2024Data Centers
Gray Expands Reach with Dallas Office
Corporate News
November 14, 2024Manufacturing, Construction
The Evolving Role of Electric Vehicles in Sustainable Construction & Design
Industry
October 18, 2024