Reshoring in the COVID-19 Storm
Manufacturing has long been heralded as the backbone of the United States’ prosperous economy, but in the late 1970s, companies started offshore production to lower costs and maximize shareholders’ profits.
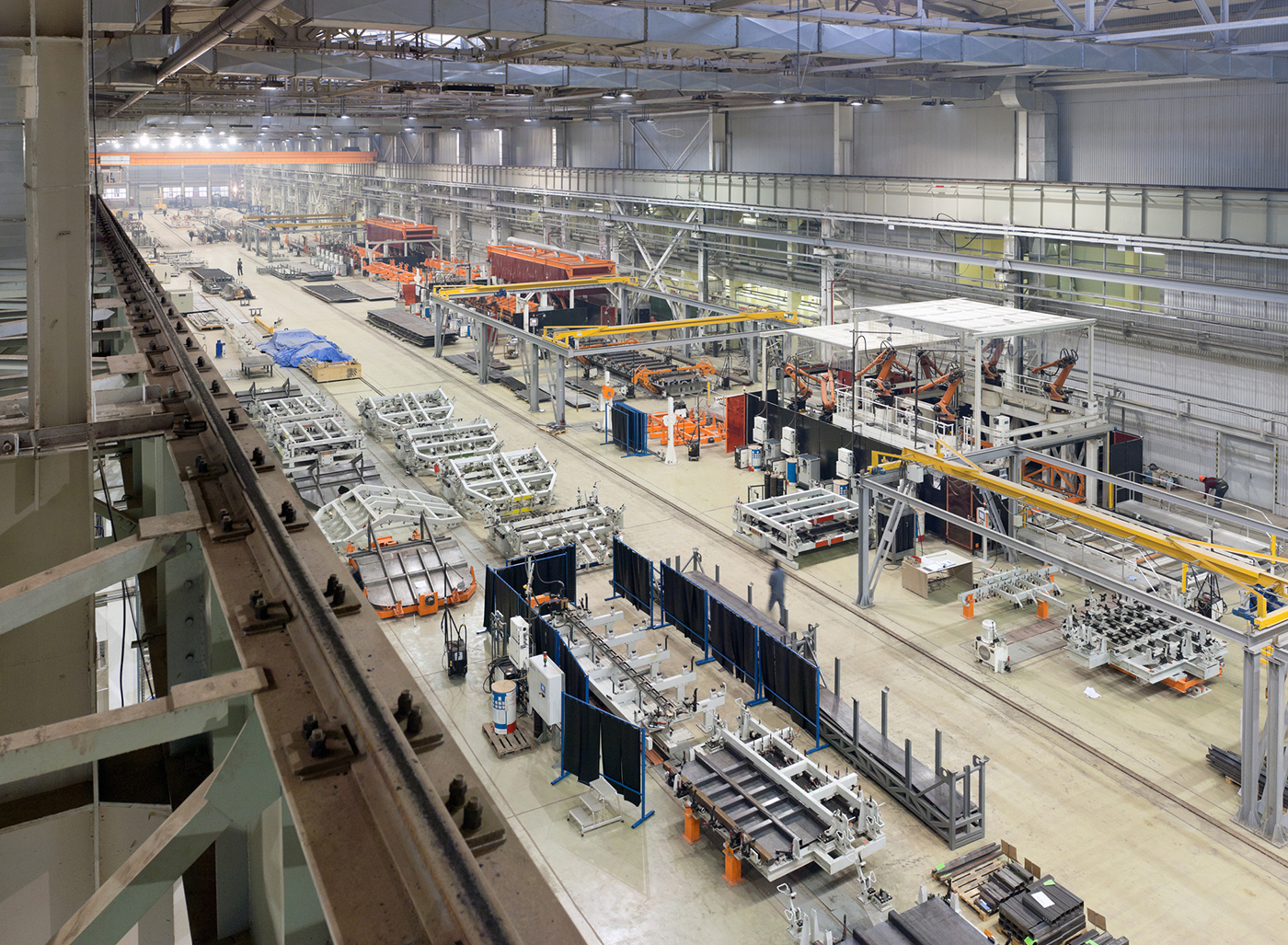
Since then, wage increases in offshoring countries rose consistently, driving the profits down, making the reason for offshoring less clear. Reshoring, bringing manufacturing back to the United States, began to make more sense as companies weighed the Total Cost of Ownership (TCO), which is defined as all the costs of manufacturing a product from beginning to end—especially escalating labor costs, tariffs, quality issues, and unstable supply chains.
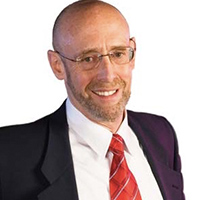
Harry Moser grew up with manufacturing as his family’s income backbone. In 2010, after 25 years as North American president and then chairman emeritus of GF AgieCharmilles (now GF Machining Solutions), and watching the demise of his industrial hometown, Moser decided to spearhead an initiative to bring back offshored companies. The Reshoring Initiative is designed to educate and assist companies in ways of bringing manufacturing back to America.
U.S. manufacturers are feeling the effects of our long supply chains being cut off as COVID-19 brings the world to a standstill. Now, more than ever, the goals of the Reshoring Initiative are crucial to not only prosperity but the survival of our nation and its economy.
Moser recently provided input on the short-term and longer-term impacts COVID-19 is having on the reshoring of American manufacturing.
The Reshoring Initiative began long before the pandemic occurred—how is COVID-19 shaping the movement going forward?
Moser: It has gone from being an intellectual understanding to a visceral fear, a fear of death, fear of losing your job, a fear of your kids losing their jobs. An impact like the Great Depression, again. The pandemic has really gotten people’s attention. COVID-19 has revealed the U.S. dependency on offshore manufacturing, especially China, for health-related items. Not just the masks, gowns, and the gloves, but also the penicillin and pharmaceuticals as well as the active ingredients for the pharmaceuticals we make here. About 80-95% of these products comes from offshore, mostly from China. So, we’re very dependent.
As the pandemic shows, we can suddenly be in the impossible position of not having enough critical supplies. That is not because we didn’t try; it’s because we had almost no base from which to build here in the U.S.
I believe that the politicians and the public industry now understand that our entire supply chains are at risk, so they will evaluate other dependencies—rare earth minerals, magnets made from those minerals, 5G electronics for the new communications systems, machine tools and other kinds of manufacturing technology—for which we are significantly dependent on imports.
What is the biggest hurdle companies face with reshoring?
M: First is the perception of manufacturing costs. Companies believe that manufacturing costs in the U.S. are so high that it doesn’t make any sense to even try and bring work back from China. And if it, for various reasons, has to be pulled from China, it should go to Vietnam, Cambodia, Mexico, India, or Turkey. Our data show that when the companies look only at the Ex Works (EXW) price—the price at the door, leaving the dock of the company from which you’re buying it—that only about 8% of work makes sense to reshore to the U.S. Whereas if you look at TCO (which is our tool for evaluating all the costs)—EXW price plus duty-free packaging, carrying, cost of inventory, value of a made in USA label, and other factors—and put in those numbers, it goes from 8% to 32%. And if the product also happens to be subject to a 15% tariff, then it goes to 46%. So, just by changing the perception and the methodology of measurement, all of a sudden, U.S. manufacturing is much more competitive.
But, you also have to change the reality. Our skilled workforce productivity and automation investment are just not enough to make up for our higher labor costs. We are just not price competitive, which is why TCO is so important.
Will U.S. companies be able to shift to reshoring fast enough to meet the demands?
M: To be self-sufficient again, the U.S. needs to increase manufacturing by 40%, which would generate about five million manufacturing jobs. So, could we handle half a million new jobs, a 4% increase every year? If we did that over a two-year period, we’d run out of physical capacity— buildings, factories, equipment. This would drive facility growth—for example; Gray can build a plant in six months, depending on size. You can get equipment in 6-12 months.
So, yes, we can move fast enough, but people are the key. Fewer people want to be the toolmakers, welders, precision machines, and chemical technicians.
Qualified labor has been a huge issue for years. Will the shortage of a skilled workforce stop companies from reshoring?
M: A skilled workforce is in short supply in every country. In fact, a skilled workforce is the third-highest ranked positive reason to reshore. In all countries, as wealth grows, people pursue their dreams, too often in the direction of arts or finance, instead of manufacturing.
There are 16 million people in retail. And I believe that a quarter to a third of them are going to be unemployed. Four or five million people will need jobs. Train them to become future toolmakers and welders at incomes substantially higher than retail provided.
There are a lot of people in prison who are getting out now, partially because of the virus and partially because they maybe should never have been in there. Train them and put them to work. Many of these people would love to have a $40,000-$60,000 solid, safe job.
How do you deal with the hurdle to build up a skilled labor force?
M: We have a problem with the recruitments of high school kids into manufacturing. Some think it is a dirty, dark, dangerous thing—the old-fashioned way. At the same time, everybody believed all the manufacturing was going to China. So how could a guidance counselor say, “Do you want to become a welder?” if there are not going to be any welder jobs in ten years because all the work is going to China? So, there is a synergy; reshoring needs recruitment, but recruitment needs visible reshoring to make it clear that those jobs will be there when they get trained.
A big cultural change needs to occur to convince people that they could do an apprentice alternative instead of going to university and studying.
White House National Economic Council Director Larry Kudlow has suggested reviving the economy by slashing the 21% corporate tax rate for companies willing to reshore. What are your thoughts on this?
M: Lowering corporate taxes to 21% was necessary when we had the highest rate in the world. The difference between 21% and 10.5% would only provide about one percentage point of price competitiveness. We need a 20% improvement in price competitiveness versus China. Other things that would help include 20% lower USD, a much stronger skilled workforce, training on the use of TCO, and adding a value-added tax (VAT). Also, cutting the corporate tax rate as an incentive to bring companies back is unfair to those companies that never left.
Do you think the pandemic will truly bring manufacturing home, or do you feel there will be a surge of talking and manufacturers will go back to their old ways as the pain diminishes?
M: Eight senators and three congressmen have introduced bills to address that problem to motivate, help, demand that U.S. companies bring medical health supplies back to make again in the U.S.—to make us self-sufficient once again.
I’m getting calls now from companies that want to know how to fix their supply chain and how to reshore. Every couple of days, a state or big city calls— companies and trade associations— that want to either reshore or want to convince their customers to reshore so they can sell them more.
If the federal government does not make the needed policy changes, most healthcare products will still be reshored, and maybe 10% of all other products. That could be about a $250 billion per year improvement in the trade deficit and about 1.5 million manufacturing jobs over a 5 to 10-year period.
If the government does act aggressively, then an additional 25% of the rest, bringing the total to about $800 billion per year, balancing the trade deficit and adding a total of about 5 million manufacturing jobs, for an increase of 40%.
In addition, consumers need to seek and request Made-in-America products. Manufacturers and retailers need to use TCO for their sourcing decisions and apply the statement of the Business Roundtable, including employees, suppliers, and community as stakeholders. However, the government must level the playing field so that U.S. companies have a chance of winning.
Looking Forward
To poetically borrow from Charles Dickens, “It was the best of times, it was the worst of times, it was the age of wisdom.” If we look at the dark time for America in early 2020, and use that knowledge to improve supply chains, invest in automation and robotics, and demonstrate just how resilient American manufacturing is, we can change the future into our best of times by reshoring.
- Category:
- Industry
- Construction
- Manufacturing
Some opinions expressed in this article may be those of a contributing author and not necessarily Gray.
Related News & Insights
Advanced Technology, Automation & Controls
Four Use Cases for AI's Growing Role in Manufacturing
Industry
November 25, 2024Data Centers
Gray Expands Reach with Dallas Office
Corporate News
November 14, 2024Manufacturing, Construction
The Evolving Role of Electric Vehicles in Sustainable Construction & Design
Industry
October 18, 2024