Practical Solutions to Improve Animal Handling - Part II
A Conversation with Dr. Temple Grandin, Part II
Since the 1970s, Dr. Temple Grandin has stood as a leading thinker in animal science and a staunch advocate for improving animal welfare and handling techniques within the meat processing industry. Today, her recommendations for feed lots and processing plants are widely regarded as industry best practices, and her insights into animal behavior and equipment design cannot be overstated.
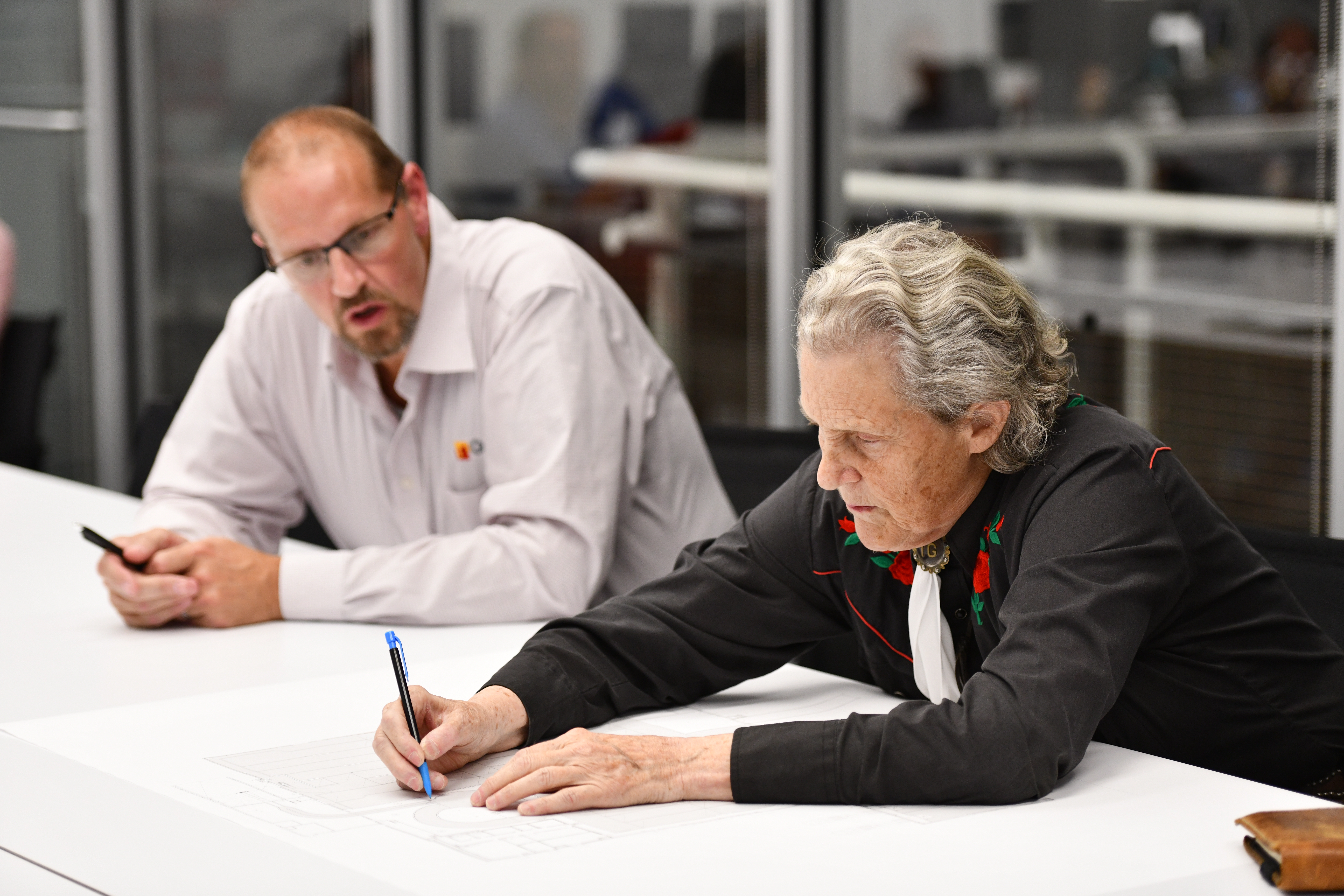
In Numbers
- Wright City, MOLocation
- 800,000 s.f.Square Footage
- 27 monthsOperational
As Gray designs and builds a large beef processing plant for America’s Heartland Packing—an American Foods Group company—Gray is carefully incorporating Dr. Grandin’s insights. Gray recently had the honor to host Dr. Grandin to review the designs for the facility.
As part of her visit to Gray, Dr. Grandin sat down for a discussion ranging from the fundamentals of her animal handling principles to the need for better IT/OT integration. This is Part II of that conversation—Part I can be found here. The discussion has been edited for length and clarity.
Q: Humane treatment of animals and the processing of animals can, on the surface, feel like repellant ideas, but your work purposefully ties these concepts closely together. Why is this so important?
A: One of my biggest concerns right now is the condition of the animal coming into the plant. When there’s a welfare issue, especially in operations that slaughter cows, it’s often because they wait until they’re half-dead to bring them in. I’ve got problems with that. Or with pigs where they’ve used a certain boar line that has really bad feet and legs, then they’re lame coming in and are very hard to handle. That’s a genetic problem. I have a lot of issues with that. I get very upset.
It’s also behavioral: if people never walk the pens to get the pigs used to people walking through them, they’re going to be horrible to handle at the plant. You have to present an animal you can handle at the plant.
With dairy cows, there are still certain dairies that wait until the animals are way too debilitated before they’re brought in. I’ve got big problems with that; I don’t care whose plant it is.
Q: What would be the impetus for processors to wait that long?
A: Well, it seems like certain people just wait too long. I call it “bad becoming normal.” They get so used to seeing lame cows that it’s almost like they don’t see them. This is why out on dairies you need to start measuring welfare indicators like body condition score, lameness, swollen hocks from too small or poorly managed free stalls. I can measure that stuff and then tell if I’m getting better or getting worse.
You manage what you measure. And dairies that measure these problems usually have a lot less of them.
Q: What are the challenges you face in advocating for industry standards, policies, and practices that stress humane methodologies?
A: I worked a number of years ago in implementing the McDonald’s audits. And that resulted in some really big improvements. But you have to keep monitoring. It’s just like traffic out on the highway. If police put away their scanners, imagine how it would be on the highways.
We constantly have to educate, too. We talk about moving small groups, not yelling at cattle, not hitting them. I find that we still have to talk about these basics. You’ve got new employees coming in, so management has to go out there and see what’s going on. You constantly have to monitor.
Q: Is technology that’s emerging helping with that?
A: Yes, there are things you can do with technology, but you can’t just delegate it all to AI. You have to get your butt out of the office and see what’s going on. Wherever you have people that get out into the field, you have less problems. Let’s take airlines for example. When Herb Kelleher ran Southwest Airlines, he worked real jobs every month: bag handler; gate agent; flight attendant. He knew what was going on, and they had fewer problems as a result. Processing plants are no different. People have to get out of the office and look around.
Tech is something that can help you. but most of that’s being monitored by an outside company. Management then needs to act on the feedback they’re getting from that company. But they have to improve the interfaces on these systems. You have all these sensors that can monitor things in a dairy, but the interfaces are horrible and none of the vendors’ tech can talk to each other. You’ll have equipment from three different vendors and none of the software talks to each other. It’s a mess.
Q: So, system integration would really help, then?
A: System integration is non-existent, and you need simpler interfaces. I shouldn’t have to take a course to monitor this stuff.
I had a student that just worked on this problem. They had a bracelet for the cows that could measure lameness and loads of data from the milking machines. But because they were from two different vendors, she had to hand-enter the data on a spreadsheet. A real mess.
Q: As an integrated family of companies in design, construction, engineering, automation, and equipment manufacturing, what role can Gray play in furthering your work and its principles?
A: Basically, by building things right. Sometimes companies have people change the design in ways that mess the system up; other times it’s just shoddy work—concrete work that wears out early; steel work that’s cheated on the pipe thickness. I’m sure Gray Construction’s not doing those sorts of things!
After startup, people need help operating the systems correctly. After I got center-track restrainers implemented across the industry in the ‘90s, half of my clients tore stuff up and wrecked it. It was very disheartening.
Then the McDonald’s audits came, along with Burger King and Wendy’s. Now owners had to repair equipment and truly manage it. For instance, the No. 1 problem with stunning was broken equipment—that was a management problem.
But customers need tech support on new equipment. I can’t emphasize enough how important tech support is. There’s a lot of new equipment coming in from Europe right now, especially in pork and chicken. It’s all too common for them to install all this new equipment, then it’s “bye bye.”
Q: Let’s says I don’t have the capex funds or the facility footprint to embrace all the best practices. What are some immediate ways that operators of existing meat processing plants can improve conditions and their animals’ quality of life? How will they know they’re making a difference?
A: In an existing plant, non-slip flooring. But some people are installing rubber mats on the entire yard. If we bred decent feet and legs, you wouldn’t need those rubber mats. That’s astronomically expensive. I went to a plant that had rubber mats and I looked down and said, “You don’t have very nice feet on your Angus cattle. You have crossed toes, and that’s genetic.” If you put cattle on a rubber mat, yeah, it’s going to improve mobility, but if you bred decent feet and legs, you wouldn’t need the mats. You see, you have to look at root causes of problems.
The other thing is equipment controls. For example, on a stun box, you need good door controls so that when you push the handle, the door moves up right away instead of going down for another two feet before it moves up. That’s going to slam on the cattle’s back, and there’s no way for the operator to control it. I’ve seen some really poor controls that make it very difficult for an operator to manage a piece of equipment. It’s relatively simple but it’s important. I went to England this summer, and they had an air valve to open the door on a stun box, but it was in the wrong location. When you’re trying to get an animal to move forward, you don’t stand at the head and poke the butt. But where this control was, you couldn’t get in the right position behind the shoulder. The guy was forced to stand in the wrong position. I suggested that they move the control. That’s a simple change, but it could make a big difference.
Q: Thank you so much for your time, Dr. Grandin.
A: My pleasure.
Readers interested in learning more about Dr. Grandin and her work can visit www.grandin.com as well as templegrandin.com. Her recent published works include the New York Times Bestseller Visual Thinking: The Hidden Gift of People Who Think in Pictures, Patterns, and Abstractions; The Outdoor Scientist: The Wonder of Observing the Natural World; and The Grandin Papers: Over 50 Years of Research on Animal Behavior and Welfare That Improved the Livestock Industry.
- Category:
- Industry
- Design
- Food & Beverage
Related News & Insights
Food & Beverage
Gray Project Receives Manufacturing Innovation Award
Corporate News, Industry
December 04, 2024Advanced Technology, Automation & Controls
Four Use Cases for AI's Growing Role in Manufacturing
Industry
November 25, 2024Manufacturing, Construction
The Evolving Role of Electric Vehicles in Sustainable Construction & Design
Industry
October 18, 2024