Practical Solutions to Improve Animal Handling
A Conversation with Dr. Temple Grandin, Part I
To those in the agricultural industry, Dr. Temple Grandin needs no introduction. Since the 1970s, she has stood as a leading thinker in animal science and a staunch advocate for improving animal welfare and handling techniques within the meat processing industry. Today, her recommendations for feed lots and processing plants are widely regarded as industry best practices, and her insights into animal behavior and equipment design cannot be overstated. Astonishingly, this is not the only arena in which Dr. Grandin’s expertise has broken down barriers and informed generations: her work concerning the developmental disorder autism has greatly contributed to our understanding of the condition and how to manage it.
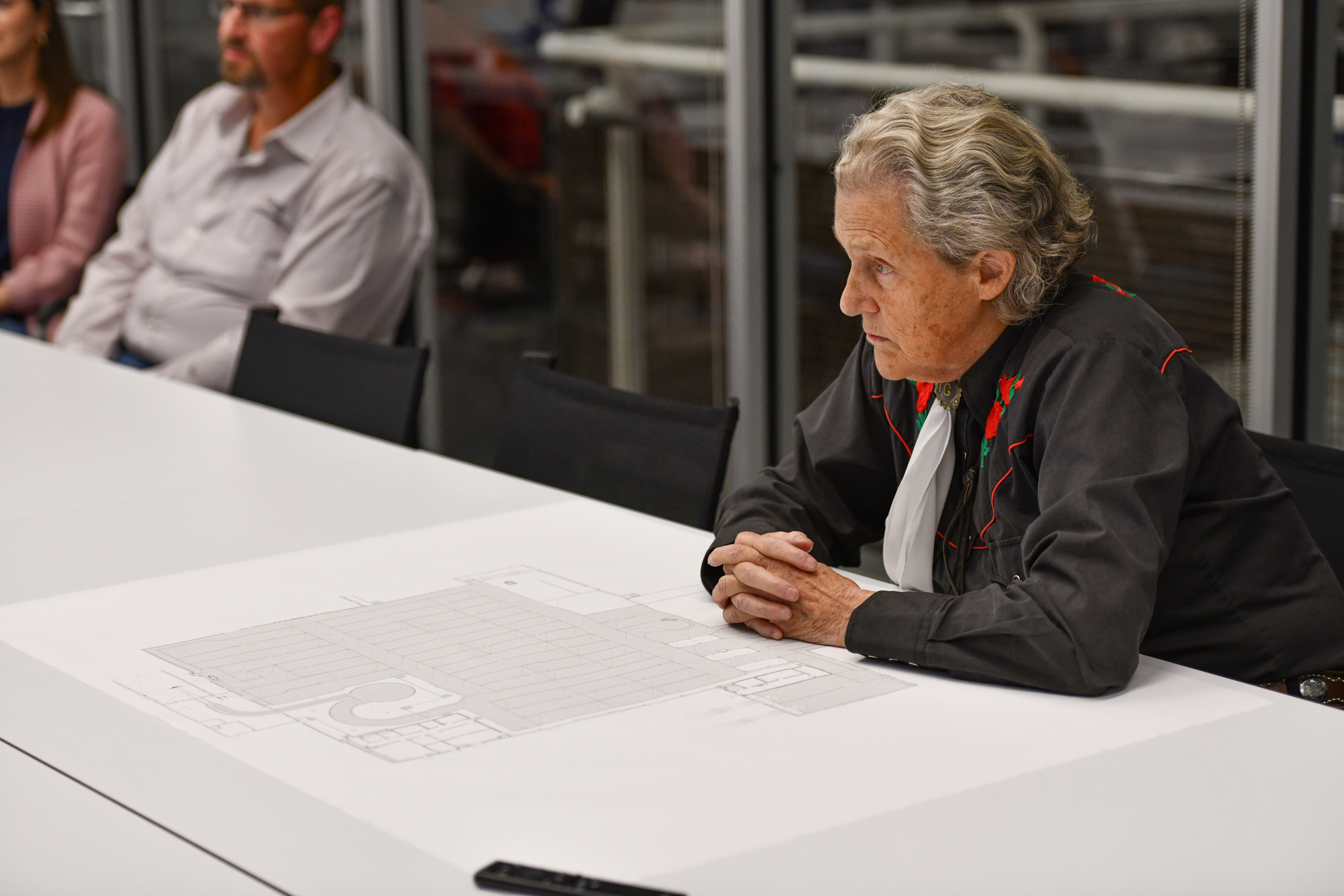
In Numbers
- Wright City, MOLocation
- 800,000 s.f.Square Footage
- 27 monthsOperational
Gray’s ongoing design-build project for Missouri’s first large beef harvest facility provided an opportunity for the company to put Dr. Grandin’s principles into action. Gray has designed the facility, known as America’s Heartland Packing—an American Foods Group company—following her methods, and when the opportunity arose to host Dr. Grandin and review the facility designs, Gray jumped at the chance.
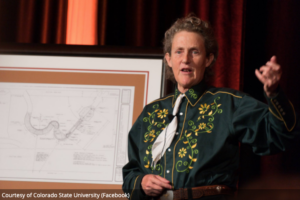
As part of her visit to Gray, Dr. Grandin sat down for a discussion that ranged from the fundamentals of her animal handling approach to simple but effective solutions for common industry problems to the need for better IT/OT integration. This is part one of that conversation. The discussion has been edited for length and clarity.
Q: Thank you for being with us, Dr. Grandin. I want to start by talking about the love for animals and connection to animals that are at the heart of your work. How do you define humane animal treatment within the meat processing industry?
A: When I first started at a Swift plant in Tolleson, Arizona, in 1972, one of the questions I wanted to answer was whether the cattle knew they were going to be slaughtered. If they knew they were going to be slaughtered, they should be wilder at the Swift plant than they were out at the feed yards. I’d go back and forth between the Swift plant and the local feed yards, and I found that the cattle behaved the same way in both places.
If you look at the data on stress going into the slaughterhouse, it ranges from high to low, but the same range occurs out on the feed yards and ranches. There is going to be stress from handling, yes, but if you’re doing things right, the cattle just walk in. At a beef plant, I found that cattle are afraid of things like air blowing back in their faces or shadows in their path. I visited one plant shortly after startup, and at two in the afternoon, a big wagon wheel-shaped shadow appeared that the cattle refused to walk over. Coats on fences, a piece of string hanging down, a construction light left on the side of a building—these can all cause problems. If you get these distractions out of the facility, then the cattle will walk right in.
Q: How do you gather enough observational data to turn that into practical recommendations?
A: I went to every feed yard in Arizona and got down into the chutes to see where the cattle were stopping. Just going through those places and observing. There might be a shadow or other time of day effects. There might be a shiny truck. At the different lots and meat plants, I could see the things that made them stop. If you remove those things from the facility, the animals will move through it.
Now at the time I did this, I didn’t realize that I was an extreme visual thinker and other people were more verbal. Some people said “That’s kind of crazy that you got down into the chute to see what the cattle were looking at.” I didn’t know that other people thought verbally. In my new book, Visual Thinking, I talk about how we need people who think visually in working with animals. Also in designing mechanical devices: people that think visually are often very good at understanding how mechanical things work.
Q: I’m glad that you mention that because I want to talk about what this design looks like practically within a beef or pork harvest facility. What handling practices, systems, and equipment promote a low-stress environment for the animals? How do you purposefully design equipment for this?
A: Non-slip flooring is absolutely essential. I developed the center-track restrainer system that’s in most of the big plants today. One of the things I learned is that you need to have a non-slip ramp going into it. You have to have it well lighted; cattle don’t like going into dark places. Now that more equipment is being made with stainless, we’ve got more problems with reflections.
But the main thing is management. You don’t just buy equipment and consider it automatic management, because it’s not. Cattle must be brought up from the yard calmly in small groups. People always want to bring the cattle up in too big of a group. We’ve got to educate people: don’t scream at cattle; get the electric prods out of your hands, because if you get the cattle all excited and upset, it takes 20 minutes to calm them down. The people working with the cattle need to calm down themselves, and then the animals are going to remain calmer and be easier to handle.
One of the other things we’re concerned about right now in breeding Angus cattle for lots and lots of meat is that they’re starting to get leg and foot problems, and it can make them sore-footed. We’re putting all our genetic breeding emphasis into meat and shortchanging the animal’s infrastructure, which would be the skeleton. We need to be breeding decent feet and legs on animals. We have to have an animal that’s fully mobile in order to handle it. When I see a big welfare problem at one of the plants, that’s something I’m going to have to fix outside the plant.
Let’s say your old dairy cows are coming in; they’ve got to be shipped to the plant when they’re still fit for transport. Don’t wait until they’re skinny and half-dead before you ship them. In order to have good handling and low-stress handling in a meat plant, I’ve got to have animals that can walk and move.
Q: That problem makes sense given the industry’s ambitious yield targets. I tend to hear this animal welfare concern expressed more commonly in reference to poultry facilities. Do you have any insight on that?
A: In poultry, the birds grow really fast, and you’ve got a system on the edge where you have to do everything right with broiler chicken. If you make one little mistake, you’re going to have a lot of lame birds and downers. But the birds have to be mobile. Period. They need to not be dirty or have lesions on them. Breast blisters, foot pad lesions, hock burn—these are things that I can measure. If you have a bad environment with wet litter, you’re going to have a higher percentage of foot pad lesions. You have to manage the litter in such a way that you don’t get these lesions.
I have a book called Improving Animal Welfare: A Practical Approach where I emphasize outcome-based indicators. There are a lot of things I can measure at a plant: lameness, broken wings from bad handling, swollen joints on dairy cows’ legs. I can measure these things and tell if I’m getting better. If I see lameness in the cattle coming into the facility, that’s a problem that we have to fix at the farm.
Q: America’s Heartland Packing will be Missouri’s first large beef harvest facility. What unique challenges come with humanely designing a large, high-volume facility that smaller operations may not have to consider? How does increasing the scale of an operation affect the approach to humanely designing the space and equipment?
A: It’s designing it for the chain speed. In Colorado, there are two extremely high-volume plants that I was involved in designing. One challenge is laying out the equipment for the chain speed you’re operating at. The other thing we have to reinforce is good handling.
Even for the large plants, you don’t bring 30 cattle up at a time: you bring 14 at a time. The plants that are doing good handling enforce moving the animals in small bunches. But that requires more walking [for the employees], so management has to enforce bringing up the correct number of cattle. Same with pigs. If you don’t enforce that, [workers] just keep bringing up more and more. You’ve got to bring up the correct sized bunches.
Q: Is that correct size more a function of ergonomics to help the animals fit better within the equipment, or is it a natural, social behavior of the animal to feel more comfortable in smaller groups?
A: What you want to do with pigs and cattle is time the bunches. When you bring cattle out of the yards through the crowd pen areas, they need to be able to immediately enter at the single-file chute. If the single file chute is full and you fill up the crowd pen, then the animals just turn around on you. People have a tendency to pack the whole back end with cattle. That doesn’t work. That’s when the electric prods come out, and you don’t want that. You have to time the bunches and operate with a single-file chute that’s long enough to provide time to refill the crowd pen without running out.
Q: Are staffing shortages playing into that problem?
A: Well, solving it requires management to enforce bringing up the right number. Time your bunches so that your single-file chute is half-empty, so when you bring up your next bunch they just flow into the single-file chute and don’t have time to turn around on you. For instance, another plant had a big silver truck near the animal intake that was unloading salt, making a dreadful noise and throwing a giant reflection. They were trying to bring cattle right up that main alley and they wouldn’t go. You have to put up a wall so that they don’t see that salt truck. Maintain the flow and minimize distractions to walking.
Q: And this can sometimes be done very simply. In my research, I read that one facility you visited was having a problem moving animals despite being designed to your recommendations. Ultimately, you discovered that this was due to light coming through a hole in the roof—a quick solve.
A: This plant was an older facility that did mostly dairy cows, and I fixed four simple things to improve the handling. First, we had handlers bring the animals up in small bunches. Next, there was a light that came from a hole in the roof that made a great big spot right where the cattle go into the chute, so we covered that up with a tarp. There was also a person checking cattle IDs, so we had to use cardboard to get her covered up and put a light on the restrainer entrance. In another place, the cattle could see people walking by and we had to put up a curtain for that. When we did these things, it really improved the handling.
Q: That’s one of the things I love about your involvement: how practical these fixes can be. These aren’t high-cost solutions. They’re simple, natural, and effective.
A: They were simple, yes. My earlier example: a brand-new facility was working great in the morning, but in the afternoon, the animals stopped because of this big wagon-wheel shadow. I went out in the afternoon and saw the shadow and thought “No wonder they won’t go across!” At one point, they were having problems at night and called me in a panic. I told them “I want you to bring up a nice calm bunch. Watch where they go up the chute and see where your lead animals stop. The lead animals will show you the stuff they don’t like; they’ll look right at it. If you bring them up too fast, they’ll just turn back on you. As it turned out, there was a portable construction light and that’s where the animals stopped. The plant got rid of that—problem solved.
Part II of our interview with Dr. Grandin can be found here.
- Category:
- Industry
- Design
- Food & Beverage
Related News & Insights
Food & Beverage
Gray Project Receives Manufacturing Innovation Award
Corporate News, Industry
December 04, 2024Advanced Technology, Automation & Controls
Four Use Cases for AI's Growing Role in Manufacturing
Industry
November 25, 2024Manufacturing, Construction
The Evolving Role of Electric Vehicles in Sustainable Construction & Design
Industry
October 18, 2024