Next-Generation Stamping Drawing Major Investment
Stamping plants have been a manufacturing mainstay for all the 20th century and beyond. As volumes of automobiles, appliances and other products grew into the millions, stamping plants with massive mechanical presses remained as noisy and robust symbols of the manufacturing economy.
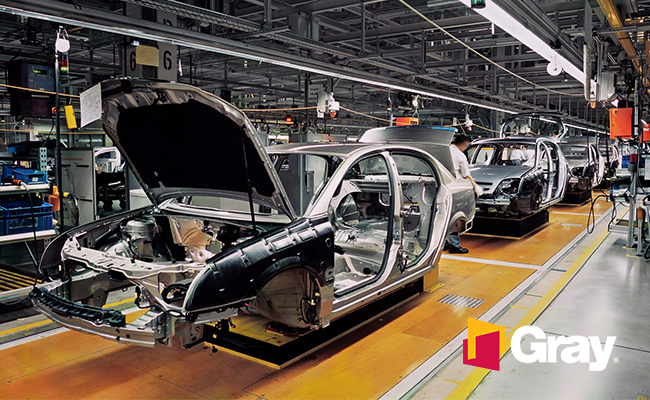
That economy now, particularly where cars are concerned, is mainly focused on safety, strength and improved fuel usage, mandating high-strength aluminum components as opposed to steel castings and forgings. In response, stamping press technology has evolved and incorporates servo motors to increase stamping flexibility and speed.
Late last year, Fiat Chrysler launched three new stamping press lines at its Sterling Stamping Plant in Sterling Heights, Mich., the largest stamping plant in the world at nearly three million square feet. The servo-driven press lines were the first new presses at Sterling Stamping since 2000, and they represent a $166 million investment.
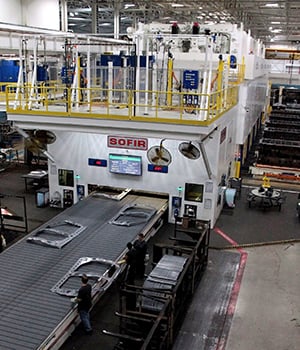
Mechanical vs. Servo
Mechanical presses are so called, because they are geared machines that use flywheels and other gear assemblies to drive the ram’s motion to provide maximum pressure at bottom dead center (BDC). Massive rams and massive flywheels and gearing would provide immense tonnage to form body panels and other components outof sheet metal with the use of dies and other tooling.
Such presses provide impressive strength but limited flexibility. As needs began to change and lightweighting and more complex parts became necessary – such as stampings with multiple bends at different thicknesses, plus piercings and other formed portions – press technology changed as a result.
Essentially, servo presses use servo motors together with geared assemblies to provide full press tonnage at different portions of the slide motion. This permits additional stamping operations, such as piercing, coining, assembly and other in-die operations in the same press stroke and often in less time, greatly increasing speed and flexibility.
Fiat Chrysler says the new servo presses are the first of their kind at Sterling Stamping. They will increase the plant’s capacity by nearly 75,000 stampings per day or 20 million stampings per year. Production at the plant will increase by about 30 percent, from more than 62 million stampings annually to roughly 82 million.
A Tier 1 stamper in Howell, Mich. also shows how it’s done. “We have competitively bid all our work since day one,” says C. Michael Hylton, executive manager of purchasing at Thai Summit America Corporation (TSAC). “About five years ago, our Plant 1 was showing signs of not being capable of keeping up with the million-vehicle programs we were growing into,” he says. To stay ahead of the curve, the company became serious about investigating servo press technology in service of high-volume stamping programs.
“The main issue is speed,” Hylton declares, asserting that flexibility and quality are also critical. Compared to the company’s history with mechanical presses, the servo motors and drives contributed significant advantages. “With a pendulum motion that can deliver full tonnage in what is essentially a half stroke, we were able to project speed increases from 50 percent to 100 percent, depending on the part,” he points out.
“The servo press starts and stops on a dime as opposed to mechanical gearing,” he went on to say. “Handling variances, such as piercings, coining, deeper draws and other requirements on the same part, also adds to profitability.”
Die Technology Also Contributes
TSAC has two servo presses that were installed two years apart. When asked what made the stamper return to their press supplier for a second press line, Hylton explained that press makers continue making advances in the entire press line technology. “We had outstanding customer support,” he says. “With our second press line, they were also supplying the die-transfer equipment, which was also servo, and the coil-feeding line at the front end. Marrying all these technologies together in a system got us up and running much more quickly.”
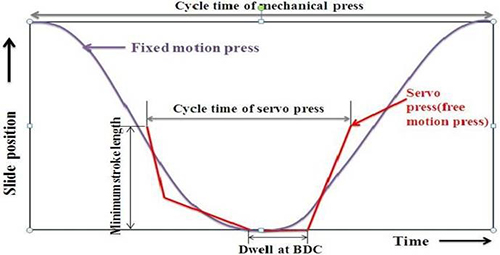
The stamper is also an experienced die builder, supplying what Hylton calls “trogs” (short for transfer dies) for his presses. “These transfer dies function as a blanking station in the press,” he says. “Servo technology allows you to use a fractional pitch – a half-pitch or a short-pitch – to synchronize blanking and all the stamping variances required for multiple jobs. It’s speed and flexibility combined,” Hylton added.
The company is also using its stamping production knowledge to further innovation. It co-developed a product for the heavy truck industry that required a draw die, which exceeds 340 mm in a single stroke. This process is currently being used in production. It uses what it calls “die floater technology” that allows for more flexibility in product development without adding an additional die. By adding another action inside the die, TSAC is able to reduce the amount of dies required to make parts.
Increasing speed and flexibility are essential foundations for keeping any manufacturing facility competitive. Stamping presses, while remaining massive and robust, are surprisingly nimble in response, and therefore are beneficial for industry competitiveness and consistent innovation.
- Category:
- Industry
- Manufacturing
Some opinions expressed in this article may be those of a contributing author and not necessarily Gray.