Will Manufacturing Job Growth Continue?
Manufacturing employment trends are a good indicator of the state of U.S. manufacturing, as well as the nation’s overall economy. According to the Bureau of Labor Statistics (BLS), the number of manufacturing jobs in the U.S. grew by 4.8 percent between 2011 and 2016, from 11.7 million to 12.3 million. More recently, the BLS “Current Employment Statistics Highlights” for May indicates that manufacturing added an average of 12,000 jobs per month from January through April 2017; however, employment was flat in May (-1,000 jobs).
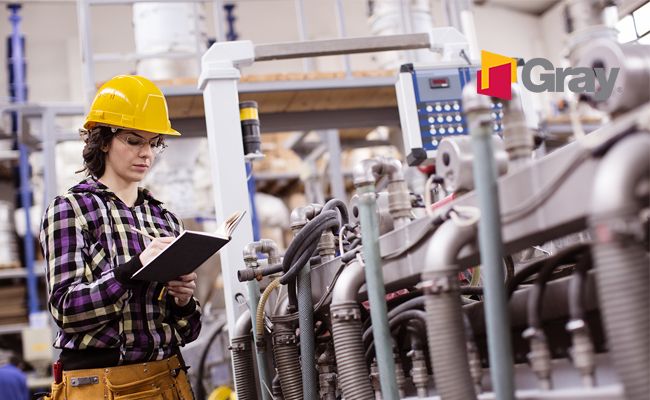
This upward employment trend is reflected by Institute of Supply Management data, which showed that through May 2017, U.S. manufacturing grew for the ninth consecutive month. Of the 18 manufacturing industries, the following sectors reported job growth in May: furniture, nonmetallic mineral products, electrical equipment, appliances, miscellaneous manufacturing, computer and electronics, food and beverage, machinery, paper products, primary metals, petroleum and coal products, and plastics and rubber products.
The industries that reported a decrease in employment are textiles, apparel and leather, fabricated metal products, chemical products and transportation equipment.
Regional Trends
Manufacturers across the country reported steady job growth at the end of 2016. To find the “hotspots” for manufacturing job growth, Joel Kotkin, an expert in demographics and urban planning, analyzed employment data from the manufacturing sector over time, reviewing short-, medium- and long-term trends going back to 2005. He also factored in the variables of persistence and momentum.
“Nine of this year’s top ten regions for manufacturing job growth are in red states, led by top-ranked Louisville-Jefferson County, which straddles the border between Kentucky and Indiana,” writes Kotkin. “Since 2011, manufacturing employment in the metropolitan area has expanded 30.2 percent to a total of 83,300 jobs, led by a resurgent auto industry that accounts for 27,000 jobs in the area.”
Other top locations identified by Kotkin are Grand Rapids, Mich.; Kansas City, Mo.; West Palm Beach-Boca Raton-Delray Beach, Fla.; Salt Lake City, Utah; and Albany-Schenectady, N.Y. Even heavily regulated California, he notes (which has lost about 800,000 manufacturing jobs since 1988), has some bright spots.
“For example, Oakland-Hayward-Berkeley, which has seen a 12.7 percent jump in industrial jobs to 89,600 since 2011, ranked 13th on the list,” says Kotkin. “The big player here appears to be Tesla, whose Fremont factory employs 6,500. The Fremont area has become something of a hotspot, with more than 900 manufacturing companies, including AlterG and LAM Research.”
According to a LinkedIn Workforce Report for May, the greatest demand for skilled manufacturing workers is not in the Midwest, which has long been considered the traditional base for U.S. manufacturing, but along the East and West Coasts. For example, Wisconsin has lost nearly 3,800 manufacturing jobs from December 2015 to December 2016 and continues to trail the national rate of overall job creation, according to BLS data.
LinkedIn indicates there are not enough workers with lean manufacturing and quality management skills to meet demands in faster-growing coastal cities such as Washington, D.C., the San Francisco Bay Area, New York City, Miami, Los Angeles and Denver. “So, manufacturing workers who are having a hard time finding a gig in Cleveland, Detroit, and Minneapolis may want to consider looking for jobs on the coasts, and employers hiring for lean manufacturing and quality management skills on the coast should consider recruiting from the Midwest,” says LinkedIn.
Not Enough Workers
An ongoing, critical problem for U.S. manufacturing is the shortage of quality workers. In fact, without a significant inflow of well-trained workers with some STEM (science, technology, engineering, and math) skills, future manufacturing growth may stall. Deloitte and The Manufacturing Institute predict the industry will create 3.5 million jobs through 2025, but 2 million of them will go unfilled.
Therefore, manufacturers must invest aggressively in giving future manufacturing workers the advanced skills they need to operate increasingly sophisticated manufacturing equipment. This includes outreach to high school students to show them how manufacturing can be a rewarding career. Convincing potential candidates to enter manufacturing will likely require boosting wages to be competitive with other industries.
For example, Reuters reported in June that the average wage on the U.S. factory floors dropped below the average for all private-sector workers in 2006, and the gap has widened since. “Manufacturing workers now earn an average of $20.79 an hour, according to the U.S. Bureau of Labor Statistics, below the $22 an hour for all workers. Service workers, meanwhile, pushed ahead of their factory-floor counterparts in 2008 and now earn an average of $21.70 an hour.
These challenges must be addressed for the future of U.S. manufacturing to flourish.
- Category:
- Industry
- Manufacturing
Some opinions expressed in this article may be those of a contributing author and not necessarily Gray.
Related News & Insights
Manufacturing
Redefining Automation: Moving Manufacturing Jobs Forward
Industry
Manufacturing, Construction
Greenfield vs. Brownfield: What’s Better for Your Manufacturing Facility?
Industry
Food & Beverage, Digital
The Impact of Tax Reform, from a Manufacturer’s Perspective
Projects