New Era of Augmented, Virtual Reality in Manufacturing
Part I: Using AR and VR As Design and Planning Tools
Put away your bond paper, sketch pads, and drafting pencils—virtual design has emerged from the fray as the preferred method of architects and engineers worldwide. Leading the hi-res charge are augmented reality (AR) and virtual reality (VR), technologies which not only offer advantages in plant and process design, but also in daily operations for built facilities.
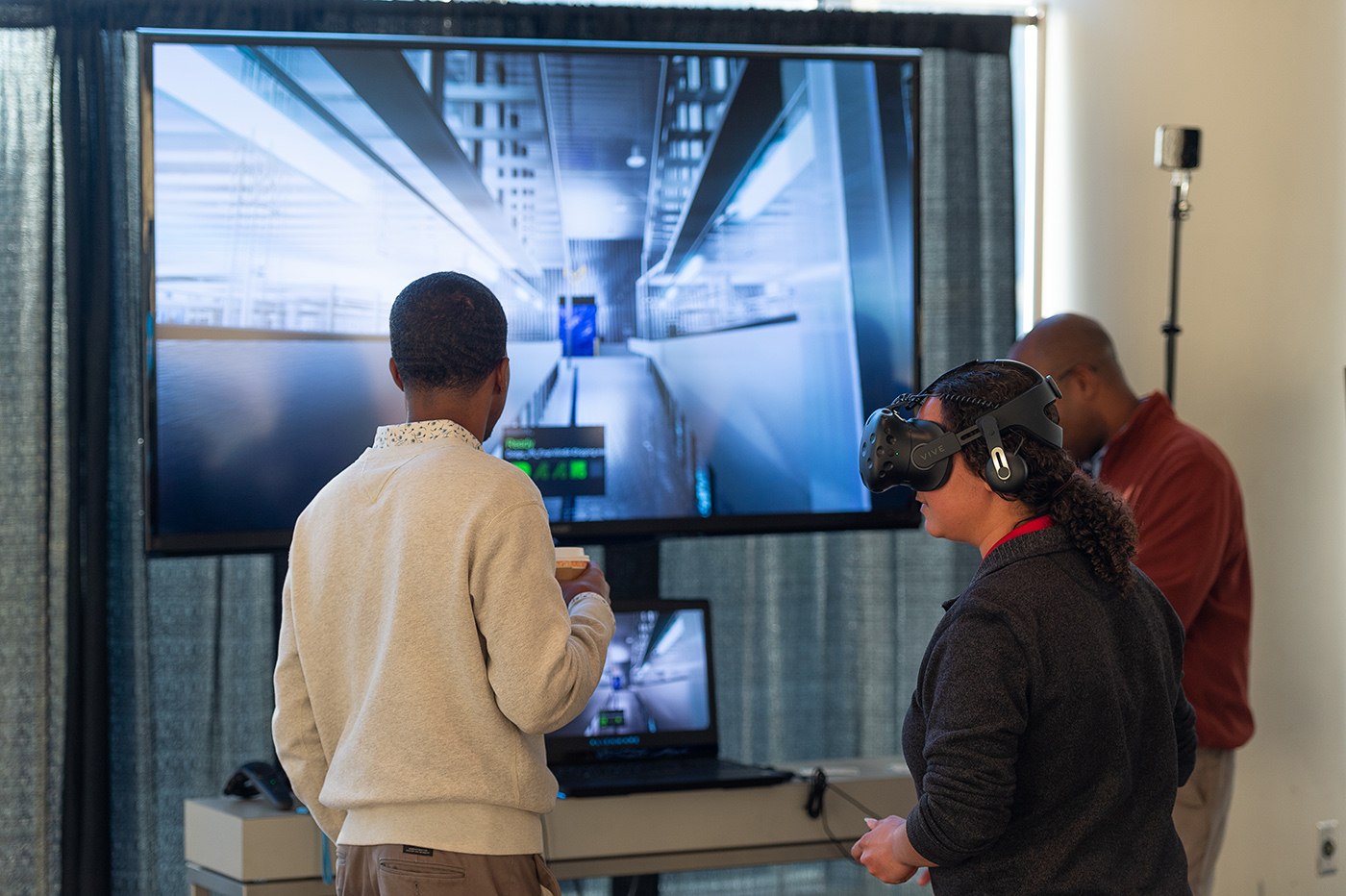
AR, VR—what’s the difference? Think of augmented reality as an overlay for a real world environment, while virtual reality is a fully immersive simulation. With AR, users can visualize and manipulate information, such as data sets and 3D objects, as part of an interplay with a real physical space. Conversely, VR allows users to create a full environment, complete with equipment, utilities, and even simulations of plant processes.
Together, these technologies are shaping the future of the manufacturing industry. In Part I of this two-part series, we’ll cover how AR and VR can be used to spark the creative process and build safer, more efficient facilities with less expense and waste.
Picture Yourself Here
One of the primary benefits of using AR and VR in manufacturing plant design and construction is the ability to enhance spatial and visual understanding. Users can place themselves within a virtual representation of a facility, allowing them to examine details of the planned layout—whether equipment has proper clearance, workpaths have sufficient width for personnel and vehicles, and utilities are run the correct distance. This visualization facilitates designers’ ability to identify issues and refine their work, such as making more efficient use of materials (or reducing the volume ordered), improving material flows, and implementing energy-saving features.
VR also enables multiple team members to collaborate within a virtual environment, which allows for brainstorming and testing ideas while being spatially aware of the facility.
“With some additional coding, customers can place virtual people in a space to [better] understand equipment clearances and distances required for an operator,” says Gray’s Robert Lownes, manager, BIM/VDC. “Multiple people can join the same space for a collaborative VR environment. This helps facilitate design ideas and innovation across teams.”
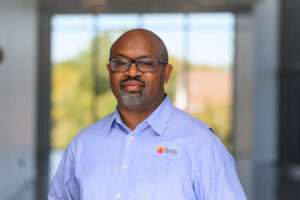
At a recent trade show, Gray exhibited a virtual model of a real-world pet food manufacturing plant the company had designed and built. The exhibit included a virtual tour of the new facility and an audio/visual walkthrough of the pet food production process. A tour guide desk and several VR stations facilitated the experience. “We ended up with the most popular exhibit on the [trade show] floor,” Lownes says.
Items such as plant safety, employee logistics, and assembly tasks can be integrated into the facility design as well, says Lownes, which results in safer and more efficient plant design and management.
Digital environments also promote greater flexibility for manufacturers by allowing customers to review the capabilities and costs of proposed process upgrades or expansion projects. With a more thorough proof of concept, leadership can better decide whether to adapt existing systems or purchase new equipment and technology.
“Customers often review a model in VR and then decide on what equipment could or should be in a space,” Lownes says. “Sometimes this can be equipment, technology, or products not originally planned for.”
Straightening the Learning Curve
Despite the many benefits that AR and VR offer, their adoption can pose a challenge to users who lack familiarity with the tools and technology. Users must have a significant level of technical understanding if they are to use these technologies effectively.
“Our facilities are very large,” says Lownes. “AR/VR requires the inverse.” He notes that integrating a model’s many finite details is a challenge that requires extensive time and effort. At times, renovation or process redesign projects require virtual designers to recreate the facility from the ground up in order to demonstrate the optimal setup. Using AR and VR can also pose logistical challenges, as end users don’t always have easy access to the necessary equipment, such as headsets.
From Design Tool to Operational Asset
For manufacturers eager to look beyond the initial design and construction of their facilities, AR and VR offer a wide range of capabilities to enhance daily operations. These can be used during the assembly of products or the fabrication of complex components, helping companies achieve better consistency in assembly quality while reducing training costs and worker errors.
AR and VR can also enhance staff training and education, especially when it comes to dangerous or expensive equipment. Managers can place trainees in virtual scenarios, allowing team members to practice the equipment’s various operations and make decisions under challenging circumstances. Apart from training simulations, AR-enabled wearable technology can help technicians as they perform work tasks by overlaying instructions or procedures on equipment as they operate it. Similarly, AR can help with work flow optimization, literally displaying the most efficient picking paths on the floor for warehouse workers.
The technology helps enhance safety by enabling employees to train on hazardous situations that they could face. “In fact,” says Lownes, “this is probably the most common request we hear from customers—how to train someone and keep them safe.”
AR and VR technologies offer numerous opportunities to enhance plant design and construction, improve staff training, and increase product innovation. Despite the challenges of their adoption, these technologies have the potential to transform the manufacturing industry and help companies stay competitive in a rapidly evolving marketplace.
For a much deeper dive on how AR and VR can be used to assist and improve manufacturing operations, check out Part II of our series . Click here to read more.
- Category:
- Industry
- Digital
- Food & Beverage
Some opinions expressed in this article may be those of a contributing author and not necessarily Gray.
Related News & Insights
Digital
New Era of Augmented, Virtual Reality in Manufacturing: Part II
Industry
Food & Beverage
Gray Project Receives Manufacturing Innovation Award
Corporate News, Industry
December 04, 2024Advanced Technology, Automation & Controls
Four Use Cases for AI's Growing Role in Manufacturing
Industry
November 25, 2024