New Era of Augmented, Virtual Reality in Manufacturing: Part II
Part II: Using AR and VR As Operational Technology
In Part I, we discussed using augmented reality (AR) and virtual reality (VR) as tools for the design and construction of manufacturing plants. In this installment, we’ll get under the hood of these facilities to see how AR and VR can be used for training, preventive maintenance, inspection, and quality control.
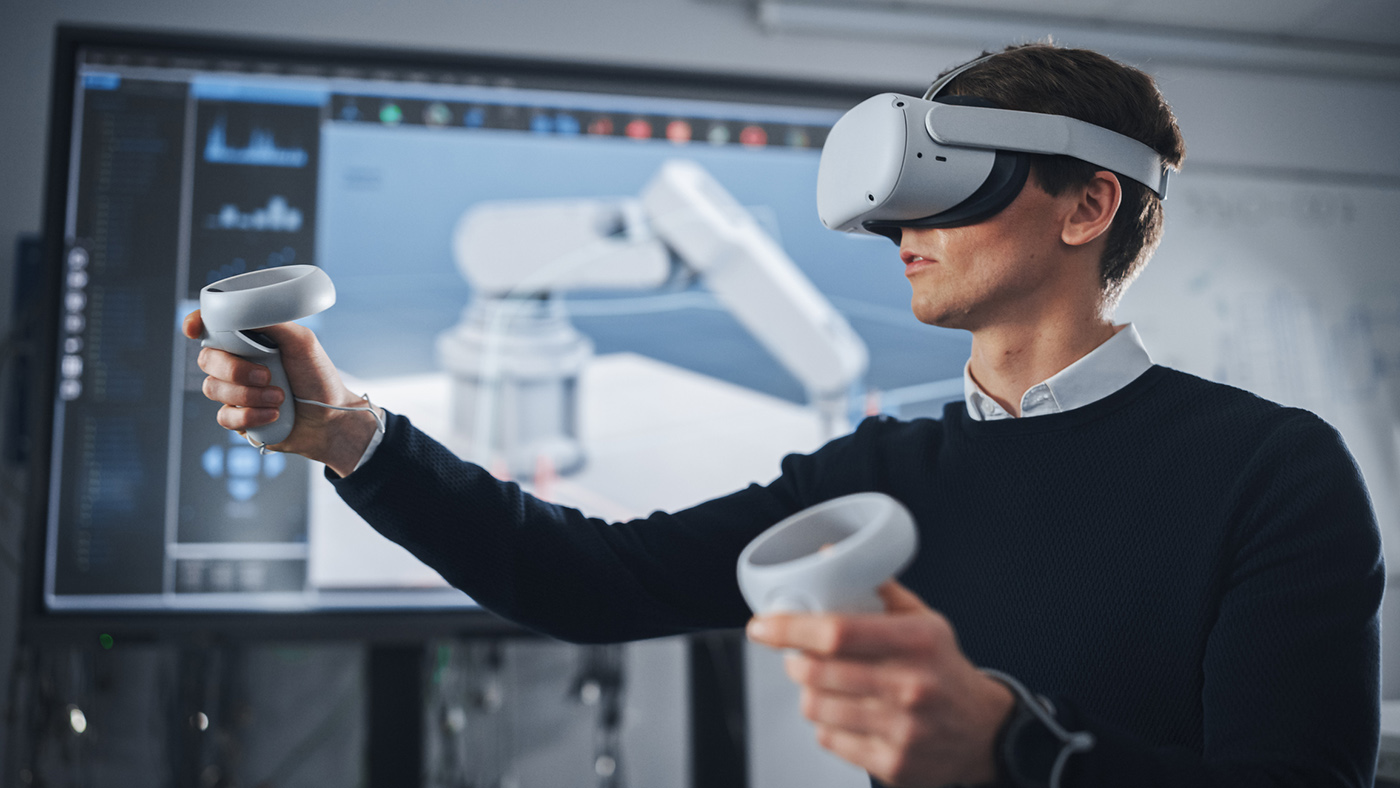
According to Rick Graff, senior applications engineer of advanced solutions at Gray Solutions, a Gray company, AR and VR technologies offer unique benefits that make them indispensable. Collaborative use of these technologies enables manufacturers to interact with human workers, test automated solutions, and engage in immersive 3D simulations of their facilities.
Each of these technologies offers distinct benefits in a manufacturing environment. “AR typically overlays visual objects in the field of view and can display augmented virtual items such as equipment or even instructions on how to perform a task on a machine or equipment,” Graff explains. “VR, on the other hand, is a total virtual world experience and typically requires a PC or good internet connection to implement the technology.”
Virtual Learning That Works
AR and VR are especially useful in training employees on new or changing processes.The technologies are increasingly well received by management and new hires alike to better understand how to operate and maintain a system or piece of equipment. AR assists employees with learning a new process by overlaying instructions on how to perform a task, offering the benefit of detailed, real-time guidance while keeping the actual equipment in the field of view.
This is extremely valuable when needing to perform complex maintenance tasks that require an operator to continually review and recall from memory the detailed steps to perform a task. AR and VR allow these steps to be interfaced to external systems to check that each step has been completed, ensuring repeatable and consistent results. Training and retraining with VR also helps new employees to understand the functional range of operations for critical systems and equipment.
Both technologies have been lauded by customers for their simplicity in use and application for all levels of the manufacturing entity, Graff says.
“A great example of applied AR technology is in the use of an annual preventative maintenance process to tear down a combined cycle gas generation turbine,” he explains. There are hundreds of steps in the teardown and rebuilding of the turbine, and it is critical that they are completed in the proper sequence. “With AR, the end-user can be instructed step-by-step what to do on both teardown and reassembly. These instructions can be overlayed in the glasses or goggles being worn while performing the work. With VR, the same process can be accomplished virtually or, say, after the machine is reassembled.”
In an immersive simulation, manufacturers can provide complete training for their teamsthrough every step of the process, from beginning shop-floor-assembly to restarting operations. “This is an invaluable tool where VR can be used to learn critical paths to operation and avoid a potential safety incident,” says Graff. Moreover, VR training can be monitored by a qualified operator and used as a certification tool to qualify new team members on a designated system or piece of process equipment prior to the start of actual plant operations. This approach can be applied to a wide variety of systems and equipment in any industry sector, explains Graff.
In addition to CAD and operator training, these tools can be used in simulation environments with immersive experiences for customers and other stakeholders. “At Gray Solutions, we use 3D simulation tools such as Emulate3D and Oculus VR headsets to develop models that allow project team members and customers to be placed immersively into the virtual environment for a complete VR experience,” says Graff. There, they can interact with the digital twin of the process system or equipment and ask questions, offer feedback, or request changes.
For instance, in a customer walkthrough of a manufacturing facility, AR can be used to explain various processes overlayed in the AR headsets while touring a facility,. In the same manner, a simulated VR environment allows visitors to participate in a guided group tour. This digital interaction can be take place with the customers in the same room or connected at remote locations. “Our customers have shown their excitement and appreciation of these tools in evaluating and seeing their investments come to life,” says Graff. “They have been great tools for reviewing and approving designs at every phase of the design-build process.”
Inspection and Quality Control Made Easy
AR technology is useful in the inspection process, where a human can monitor a non-automated process without exhaustive training on the complete inspection criteria. These criteria can be overlayed with AR glasses, providing guidance to the monitor and ensuring adherence to the rejection criteria. In this space, VR can simulate a machine’s operational settings, such as temperature and other instrument setpoints, to maintain quality control.
“A great example would be a large industrial oven with an operator that needs to learn what they should be looking for in the expected quality of the food being cooked,” Graff says. “In the simulated environment, the employee can, for instance, interact with a digital twin of the real control panel and run the equipment properly.” He notes that a qualifying supervisor can be in the simulated model with the trainee to observe and qualify the new employee or retrain the worker on new settings to ensure quality is maintained.
Further Integrations
Although AR and VR are yet to become industry standards, Graff believes that complete integration of these technologies into the manufacturing sector is just around the corner. The acceleration of plant automation and the increasing need to train new employees amid labor shortages will be driving forces behind the technologies’ complete integration in the next three to five years. “Network infrastructure and speed are also increasing and serve as foundational parallel technology for AR and VR,” Graff says.
Current barriers to the technologies’ entry into the manufacturing sector include limited network performance and bandwidth as well as the development and implementation of headsets that are lightweight and comfortable to wear. As the tech industry gradually overcomes these hurdles, virtual technology will continue to enhance the manufacturing industry in significant ways.
AR and VR are revolutionary in the manufacturing industry, with distinct benefits that improve production and maintenacne processes, enhance employee training and development, facilitate quality control, and ultimately offer better customer experiences. As manufacturers begin to implement these technologies in both known and novel ways, AR and VR will undoubtedly usher in a new wave of innovation across the sector.
Related News & Insights
Food & Beverage, Digital
New Era of Augmented, Virtual Reality in Manufacturing
Industry
Advanced Technology, Automation & Controls
Four Use Cases for AI's Growing Role in Manufacturing
Industry
November 25, 2024Distribution, Advanced Automation
Shining a Light on the Lack of Fully Automated "Dark Factories"
Industry
September 27, 2024