Metal-to-Plastic Conversion Expands Design Possibilities
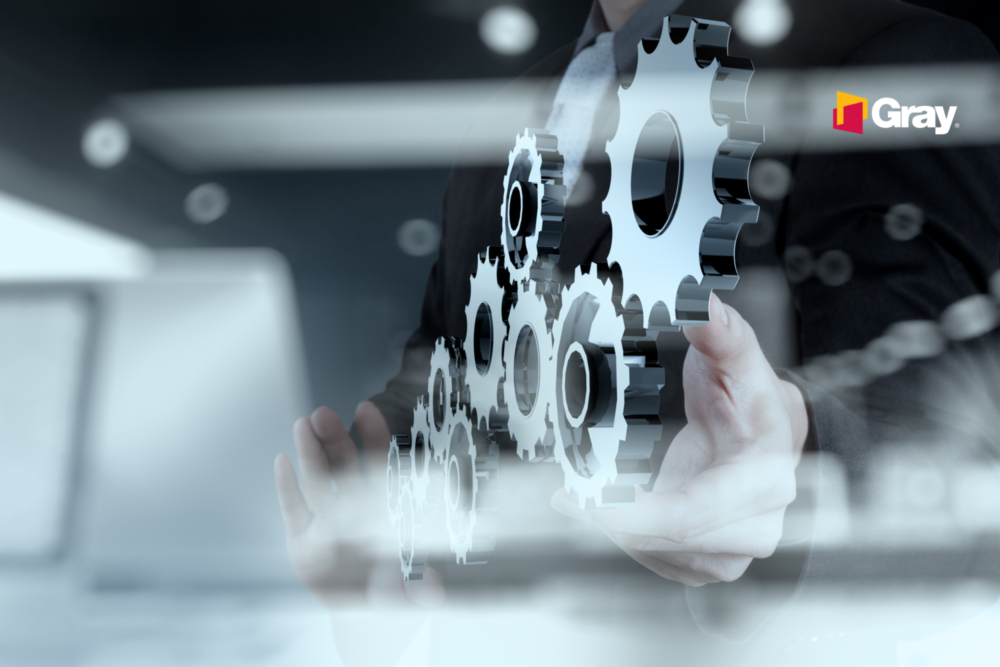
Metal-to-plastic conversion is the practice of using highly engineered plastic components to replace traditional metal components in manufactured products, without sacrificing quality or performance. Even though this process has been used successfully since the 1950s, many manufacturers still don’t know the many ways metal-to-plastic conversion can help them in their operations—especially when it comes to cost reduction.
Because plastic can be molded into smaller and/or more complex shapes, using plastic allows engineers to be more creative in their product designs—in fact, sometimes one plastic part can replace multiple metal parts in a product. This reduces the number of assembly steps, as well as points of potential failure (joints and connections)—all of which simplify the product and the process, improve quality, and save time. The gains derived by using plastic components instead of metal ones can save up to 50 percent in operational expenses. Other savings come from cheaper shipping and distribution costs, both for the raw materials and the finished product, because plastic is so much lighter than metal. This helps make U.S. companies more competitive with low-cost countries.
Tough as steel
What many manufacturers don’t realize is that, when engineered properly, plastic parts can be injection-molded with the same tight tolerances as metal parts, and perform just as well (or even better). Carefully formulated, high-performance plastic blends and hybrids can be custom-designed to provide specific performance requirements—such as strength, flexibility, and heat and corrosion resistance—making them ideal for fuel systems, fluid handling systems, and other high-temperature applications.
More than 25,000 engineered materials are available for manufacturing applications. According to the American Society of Mechanical Engineers, benefits that come with metal-to-plastic conversion include:
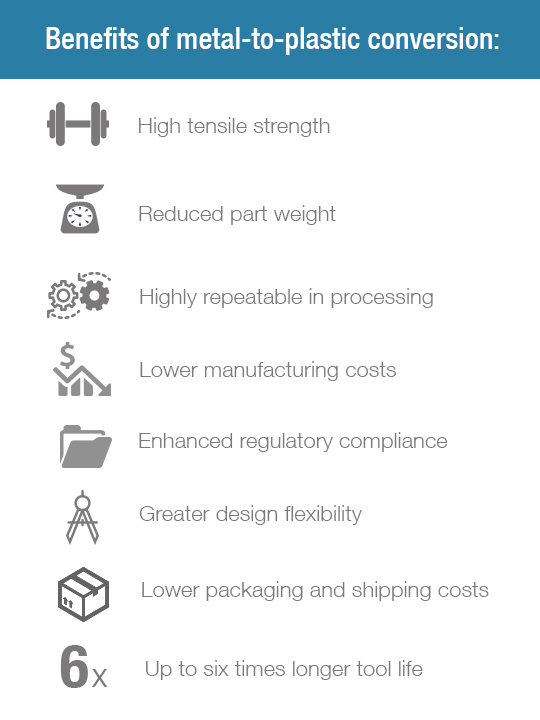
One of the most popular plastics for metal-to-plastic conversion is polyetheretherketone, or PEEK. This hard plastic exhibits superior mechanical performance, high thermal resistance, and low flammability. Because of its hydrolysis resistance, PEEK can be exposed to high-pressure water and steam without degrading. With an operating temperature as high as 450 °F, PEEK is often used in the aerospace, automotive, and chemical processing applications.
Other top plastic choices for metal-to-plastic conversion are:
- Polyamide-imide (PAI)—high strength, broad chemical and radiation resistance, and flame retardant. Because of these unique characteristics, PAI is often used for the coatings for magnet wire.
- Thermosetting polyimide—known for its thermal stability, chemical resistance, and excellent mechanical properties, including a high ductility, this material is frequently used in the aerospace industry.
- Polychlorotrifluoroethylene (PCTFE)—non-flammable, high tensile strength, and resists heat up to about 350 °F. Because of its excellent electrical resistance and very low moisture absorption, PTCFE is often used to protect electronic components and printed circuits.
Applications abound
The automotive and aviation industries have been taking advantage of metal-to-plastic conversion for years to reduce weight and improve fuel efficiency (replacing a metal component with a plastic one results in about a 50-percent weight reduction). Besides being lighter weight, components made from engineered plastics can be just as durable, heat-resistant, and chemical-resistant as metal components, making them suitable for harsh operating conditions.
More metal-to-plastic conversion is starting to happen in the medical device industry—for example, tools and instruments such as hip retractors are typically made of metal. However, when made from plastic, they are lighter weight and easier to use but still provide high strength and stiffness. These high-temperature plastics can also withstand intense cycles of disinfectants and steam sterilization. Other industry applications that are on the rise include construction equipment, industrial pumps, fluid power applications, heavy equipment, appliances, and consumer products such as lighting fixtures, folding tables, and water purifiers.
Greater design freedom
Converting metal parts to plastic parts gives manufacturers more freedom in product design, including material selection and being able to create more complex geometries. “It is much easier to produce complex shapes out of plastic than metal,” states ASME. “Multiple metal parts can be replaced by one injection-molded part made of tough engineered plastic, eliminating the need for fasteners and assembly.”
3D printing companies are also developing new materials that have higher temperature and chemical resistance. Stratasys, for example, has manufactured a heat-resistant material that is suitable for the thermal testing of static parts. Another high-temperature material—RGD525—can simulate the thermal performance of engineering plastics and is ideal for testing applications such as hot-air flow or hot-water flow in pipes and faucets. Although these thermal limits are lower—about 200 °F—higher thermal resistance is expected with future materials.
Perhaps the most exciting advantage of metal-to-plastic conversion is the design freedom it provides engineers. “They can think in more creative ways about complex geometry, performance in harsh environments, shielding considerations, weight and structural limits, thermal management, and product differentiation—both in performance and how it looks on the shelf,” writes Kaysun Corporation, an injection molding company in Manitowoc, Wisconsin, on its corporate blog. “As material suppliers continue to develop high-strength thermoplastics that are increasingly impact-resistant, corrosion-resistant, and heat-resistant, more companies across a range of industries are converting from metal components to plastic.”
Mark Crawford is a Madison, Wisconsin-based freelance writer who specializes in business, science, technology, and manufacturing.
- Category:
- Industry
- Manufacturing
Some opinions expressed in this article may be those of a contributing author and not necessarily Gray.