Manufacturing Leaders Must Embrace Change (and Technology) to Stay Competitive
Being a manufacturing leader has been a wild ride these past few years, with trade wars, COVID-19, and wobbly supply chains. Uncertainty—daily, weekly, monthly—has become a constant in the manufacturing world.
This will likely not change in 2021.
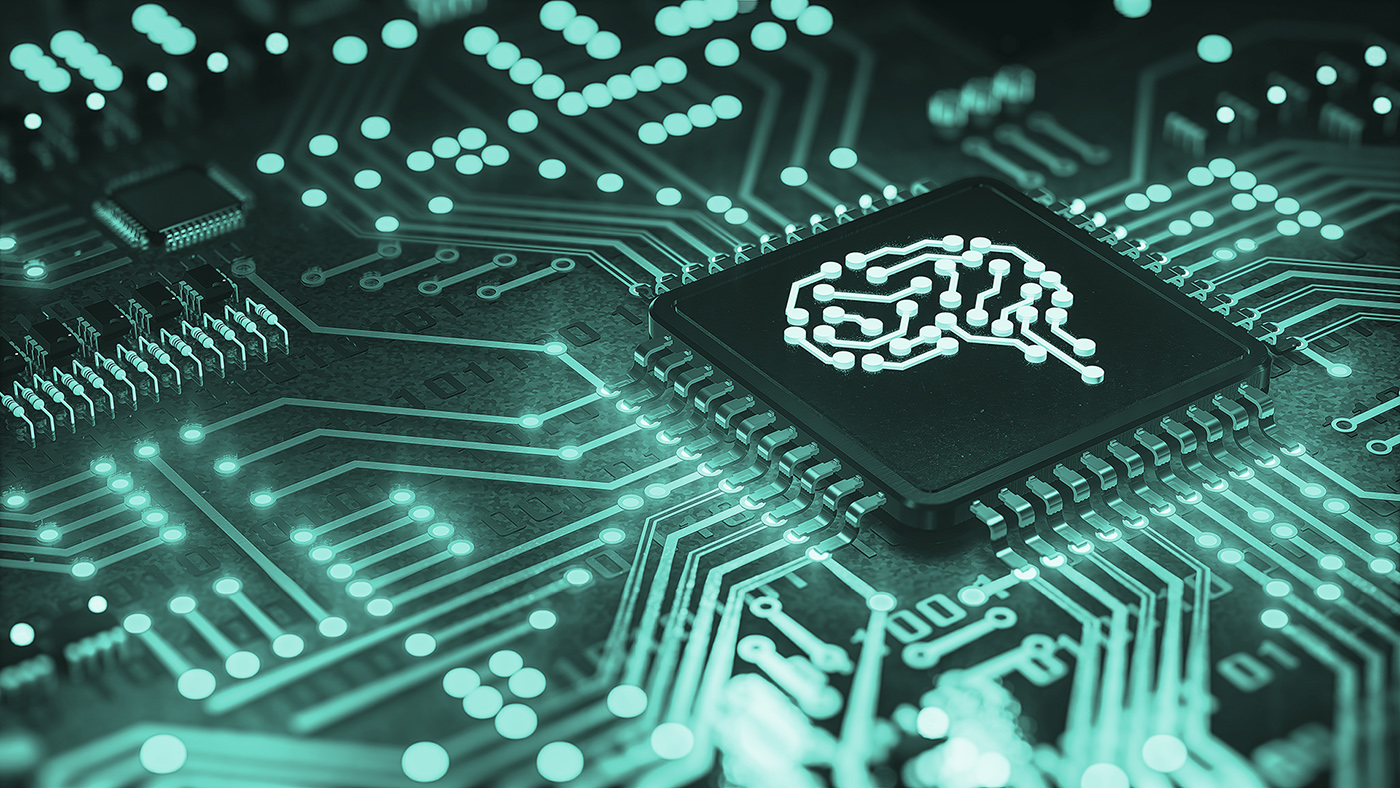
The business climate will hopefully settle soon into a “new normal” as the U.S. government transitions to a new presidential administration, COVID-19 gets under control, and employees return to work under new safety guidelines.
Manufacturing leaders must heed the lessons that were learned during the trade wars and pandemic. This includes keeping the improvements that worked and discarding those that did not to build a culture of preparedness for quick response and decision-making that can deploy assets in smart ways, should another crisis rock the global economy.
According to the National Association of Manufacturers (NAM), manufacturing executives have plenty of challenges on their plates. In a third quarter 2020 survey of manufacturers, the NAM identified the top current business challenges for manufacturers:
- Weak domestic economy and sales
- Attracting and retaining quality workforce
- Rising healthcare and insurance costs
- Trade uncertainties
- Weak global growth and slower exports
- Increased raw material costs
- Unfavorable business climate (taxes, regulations)
- Transportation and logistics costs
- Access to capital
A recent survey by the Manufacturing Leadership Council also reflects the following concerns:
- Diversify revenues
- Increase market differentiation
- Modernize IT infrastructure
- Bolster cybersecurity
- Improve customer experience
- Increase operational efficiencies
These surveys reveal the top challenges for manufacturing leaders going into 2021. COVID-19 and the China-U.S. trade war have shown the vulnerability of U.S. manufacturing to major disruptions. Proactive manufacturing leaders have responded by identifying, purchasing, and deploying new systems and technologies to stay operational and competitive during the economic downturn. When current markets stabilize, it will be especially important to maintain this momentum and not slide back into the status quo. Visionary leaders will build on what they learned during the last few years and invest in the necessary infrastructure and resources so they can be quick, agile, and decisive decision-makers when future disruptions occur.
Invest and Deploy
Smart companies will maintain or expand the improvements they made to boost efficiency and productivity and reduce costs during the pandemic, giving them a competitive edge in their markets, both now and in the future. This means deploying more digital technologies and cultivating an Industry 4.0 mindset at all business levels. Key objectives for manufacturing leaders in 2021 include:
- Improve operational efficiency. Manufacturers are relying on simple, proven methods such as lean manufacturing to streamline manufacturing processes, reduce waste, and optimize the use of manpower, especially as needs for social distancing continue.
- Automation. Automation improves throughput, reduces errors and rework, and improves quality. It can reduce injuries among workers and also enable social distancing in the workplace by performing remote maintenance and management of machines.
- Supply chain resiliency. Shorter, more efficient supply chains are a top focus among manufacturers. Industry 4.0 technologies can be used in real time to provide greater transparency throughout the supply chain. Reconfiguration of supply chains to include domestic suppliers further reduces risk.
- Cybersecurity. Increased cyberattacks during the COVID-19 pandemic have made enhanced cybersecurity a top priority, especially when many employees are working remotely. “Industry 4.0 adoption is also increasing cyber risk by giving bad actors more points of ingress,” says Eskander Yavar, management and technology advisory services national leader for BDO. “Product development teams especially need to embrace privacy by design principles, pursuing innovation with privacy and security considerations.”
- Digitization using digital twins. A digital twin, or simulation model, is a perfect digital replica of a living or non-living object, or collection of objects. The Internet of Things, with its sensor capabilities, and other Industry 4.0 technologies, create these virtual models that can update and change, in real time, as their physical counterparts change. Digital twins can be manipulated to optimize manufacturing systems and even complex supply chains.
- Cloud-based software for work-from-home processes. Remote work and team collaboration are most efficient when conducted through a single source of truth in the cloud, using cloud-native secure applications and tools. Cloud collaboration also makes companies more attractive to younger generations. “Senior executives have to ask themselves—do we have the type of flexible systems and collaboration environment that is going to give us an advantage in attracting younger workers?” questions John McEleney, corporate vice president of strategy at PTC, on IndustryWeek.com.
Leadership Style, 2021
In order to reduce operating costs, expand revenue, and adapt quickly to economic fluctuations, manufacturers must overcome attachments to outdated technologies and embrace Industry 4.0. This can be, however, a steep challenge to traditional-thinking leaders.
“Two top reasons digital initiatives fail are interoperability issues with legacy technology, cybersecurity, and lack of skills and/or insufficient training,” says Yavar. “Improving the customer experience is also vital for retaining customers and building loyalty, and organizations are increasingly leveraging Industry 4.0 tools to meet their customer experience-related goals. However, technology by itself isn’t enough—you need people with the right skills to wield it.”
Developing a strategic roadmap for adapting Industry 4.0 requires a well-planned methodology, such as the Future State Optimization Program, developed by Kansas Manufacturing Solutions, an organization that helps Kansas manufacturers address operational challenges and create growth. “This program begins with an assessment to clarify the current state and includes a traditional SWOT analysis [strengths, weaknesses, opportunities, and threats] and the building of a flexible roadmap, which breaks down how a manufacturer should proceed and why,” states Tiffany Stovall, CEO of Kansas Manufacturing Solutions. “A major consideration is if the current environment is permanent or temporary. The analysis can make the future seem less daunting and includes key areas of the business model, such as customers, management, workforce, facilities, and operations. The process helps manufacturers prioritize goals, revise objectives, and develop an action plan based on necessary responses to uncertainty.”
Manufacturing leaders must also capitalize on lessons learned from the economic and pandemic crises to create their personal leadership models, including using feedback from employees and customers. Capgemini, a global consulting, digital transformation, technology and engineering services firm, suggests a three-phase approach:
- Understand the post-crisis baseline. Assess the status quo using questionnaires, evaluate the data, and define the leadership vision and program.
- Develop and roll out the leadership development program. “Develop digital literacy by combining virtual classroom training, a digital self-directed learning academy, hackathons, or other formats,” advises Luisa Schoenwald, a manager for Capgemini. “Foster emotional intelligence with mindfulness and resilience. Also consolidate the learnings and deepen the experiences by peer coaching or communities of practice.”
- Sustain the leadership model. Maintaining momentum can be the greatest challenge to the successful implementation of new leadership models. “Be accountable by showing responsibility for designing the future,” adds Schoenwald. “Also, build networks by organizing communities of practice and think tanks.”
Perhaps the most impactful Industry 4.0 technology is data management and analytics. Today’s digital manufacturing operations are gradually evolving into smart factories, where big data analytics are available in real time to maximize productivity and efficiency while reducing operational costs.
“The challenge that remains is transforming that data into actionable information, a step that many manufacturers still miss,” states Thomas Luck, chief executive officer USA for FORCAM. “To remain competitive, manufacturers need a more profound knowledge of how to apply digital technology on the shop floor, which allows them to apply processes and controls to improve production capabilities throughout the entire enterprise. Powerful metrics, such as overall equipment effectiveness [OEE], integrate machine and production data for unbiased insights and real-time accuracy in operational performance.”
Manufacturing leaders must play both a mobilizing and facilitating role to grow their operations. The increasing adoption of digitalization and remote work will lead to a paradigm shift, notes Schoenwald, that will require new comprehensive leadership models and skills.
“Leaders will be judged by their capability to mobilize their ecosystem and facilitate new competencies,” she says. “As we move toward an authentic leadership model in the post-crisis world, some leadership qualities will become more important as they support the mobilization of ecosystems. Digital literacy to operate effectively in a digital workplace, agility to build momentum for projects, and purpose to build solidarity and engage employees will become crucial.”
However, she adds, the model must also include other leadership qualities that the COVID-19 crisis has proven to be valuable, such as building relationships to foster fun and enthusiasm, nomadism to organize remote work, and emotional intelligence to foster conscious stress management and resilience building, “which will challenge the status quo and drive evolution,” she concludes.
New business models that capitalize on Industry 4.0 capabilities will continue to evolve as manufacturers move forward.
“It’s tempting to think that the pace of change will slow down in the future, that we’ll all have a quiet moment or two to catch up,” says Yavar. “That sort of wishful thinking is fatal for manufacturers.”
Even if the pandemic and the recession both end tomorrow, he notes, companies would still need to keep pace with the technology changes that continue to shift the manufacturing paradigm. Manufacturers need to start thinking today how they plan to meet the Industry 4.0-enabled future. “By taking concrete short-term steps to address immediate disruption, they can begin to leverage Industry 4.0 technology that will enable them to look further ahead in the future as they continue to weather the strains of the pandemic, ultimately re-emerging on the other side stronger than ever,” he says.
- Category:
- GrayWay
- Construction
- Digital
- Manufacturing
Some opinions expressed in this article may be those of a contributing author and not necessarily Gray.