Is Manufacturing Really Experiencing a Skills Shortage?
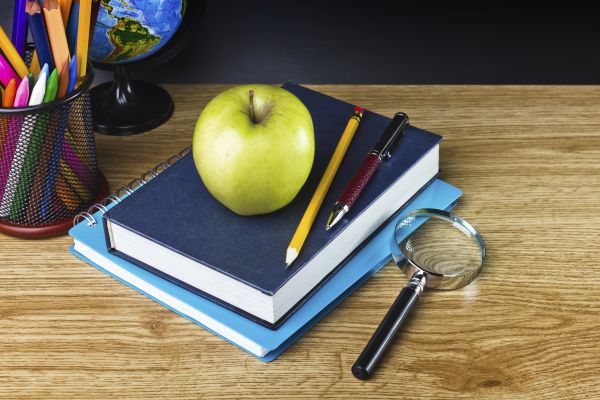
A skills shortage is causing problems for manufacturers … or is it? Nearly 1,000 manufacturing employers recently reported on how hard it is to hire production workers with the right skills.
What skills are manufacturing employers looking for? The researchers who conducted the study, Paul Osterman and Andrew Weaver of MIT, asked employers what skills are required for jobs in their factories.
The data was broken down into two skill levels: the basic and the extended abilities to read, write, understand math, and work with computers. Basic reading, writing, and math skills include the ability to read basic manuals, write short notes, to add, subtract, multiply, or divide numbers, and to handle fractions. Employers reported the following requirements for candidates:
- 76.5% needed people with basic reading skills
- 60.5% needed people with basic writing skills
- 74% needed people with basic math skills
- 62% believe basic skills included computer usage several times per week
This level of skill is provided by a reasonably good high school education, so is available to most people in the workforce.
A job requiring extended skills could call for reading 5-page technical documents such as articles in trade journals, for writing one page, for performing algebra, geometry, or statistics, or for using CAD/CAM or other manufacturing software.
- 52% of employers were looking for people with extended reading skills
- 38% of employers were looking for people with extended math skills
- 42% of employers required more advanced computer system usage
A good high school or community college education ought to provide a solid skill basis and can be supplemented by employer-provided training.
People skills are recognized by employers as more important than reading, writing, and arithmetic — the ability to cooperate with other employees (80% of employers said so) and work in teams (60%). These don’t have to be learned in the classroom.
In contrast to reports of dire skill shortages, most employers said it wasn’t much of a problem to find people. 90% were able to find job candidates within 12 weeks and hire them an average of 86% of the time. Only 24% of employers reported having long term vacancies. In fact, skilled worker availability ranked lower than weak demand, taxes, and regulation in their list of worries.
Where is the hue and cry coming from? Politicians and industry associations are looking for headlines. And loud complainers may be the same employers unwilling to pay a good wage, provide attractive benefits, and offer a safe and respectful workplace.
The real crisis may not be a shortage of skilled workers, but one of too few enlightened manufacturing leaders.
The authors agree that a good education system is a necessary foundation for a skilled workforce, and many are in trouble. We can see that good schools are producing good employees, but we need to do more to make sure all schools prepare students for the world of work.
For read the report in full, visit “Why Claims of Skills Shortages in Manufacturing are Overblown,” Issue Brief #376, Economic Policy Institute, www.epi.org, March 26, 2014.
(The Economic Policy Institute (EPI) is a nonprofit, nonpartisan think tank created to include the needs of low- and middle-income workers in economic policy discussions.)
Karen Wilhelm has worked in the manufacturing industry for 25 years, and blogs at Lean Reflections, which has been named as one of the top ten lean blogs on the web.
- Category:
- Industry
- Manufacturing
Some opinions expressed in this article may be those of a contributing author and not necessarily Gray.