How Three Manufacturing Giants are Saving Big on Energy Costs
U.S. manufacturing firms spend almost $230 billion on energy each year, and use almost 25 percent of the nation’s energy. When it comes to cutting energy costs, however, little things can mean a lot. Manufacturers like Johnson Controls, Toyota, and 3M, have found some significant savings by paying attention to small details.

1. Johnson Controls
It’s just air, isn’t it? In manufacturing, compressed air is indispensible and it costs money to produce. When Johnson Controls initiated a Compressed Air Efficiency Program, its Continuous Improvement (CI) team set out to reduce large and small compressed air leaks and inefficiencies.
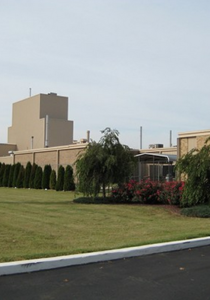
The Johnson Controls Middletown Delaware plant produces lead acid batteries, requiring the use of a significant amount of compressed air. The CI team there found losses small and large. They applied some simple solutions, plus advanced smart manufacturing systems and data analytics, in a wide attack on waste in the compressed air systems.
They began by turning off air compressor equipment when idle, and detecting and repairing small air leaks promptly. Smart meters were installed to measure compressed air pressure, flow, and compressor current. They are connected to a web-based real-time monitoring system, for quick response to leaks.
The team also found leaks that were once undetectable. For example, compressed air is used for purging the baghouse filtration systems that prevent pollutants like lead and barium from being emitted into the atmosphere with the used air. When smart meters were installed, they revealed a large number of tiny air leaks. Stopping those leaks increased the efficiency of the compressed air system, while making pollution control more secure.
Improvements implemented through the Compressed Air Efficiency Program helped reduce the facility’s air electricity usage per unit by 39 percent and monthly compressed air electricity costs by 37 percent. An improvement effort in a single plant reduces costs, but deploying those improvements throughout the company is where the big savings are found. By spreading the Compressed Air Program to all its plants, Johnson Controls estimates it may save $1.5 million per year.
2. Toyota
A focus on HVAC systems helped Toyota save money on heating and cooling its plants. HVAC costs represented 16 percent of total plant electrical costs at Toyota’s West Virginia plant a few years ago. A closer look revealed that the plant’s HVAC system, designed for extreme weather conditions, was oversized. In addition, because it was an older system, it was not equipped with today’s variable frequency drives (VFDs) on fan motors. VFDs monitor temperature in the plant, and respond to control fan motor speed, reduce airflow rate and produce energy savings. With the VFDs in place, airflow can be reduced during non-production and non-summer months while still maintaining the same space temperature on the production floor. Upgrading those motors with VFDs, depending upon usage and weather conditions, reduced the HVAC system total energy use at that plant by 30-86 percent, for payback on investment within two years.
Following that pilot project, Toyota installed VFDs on 211 motors in 164 HVAC units in its Georgetown, Kentucky plant. Deploying the VFDs, along with software upgrades to its vintage 1987 building automation system, is expected to result in:
- Annual savings of more than 11 million kWh of electricity
- A 2.6 percent reduction in the plant’s total electric consumption, for an annual cost savings of $700,000.
This represents a 1.8-year payback period, with future savings on the way.
3. 3M

A barrier to implementing improvements like these is that they are typically too small to make it through a manufacturer’s capital investment approval process. 3M cut the clutter of having numerous small projects to consider. It simply set up a yearly capital set aside fund specifically for energy efficiency projects costing less than $50,000. The corporate energy manager is empowered to control the fund and selects energy-efficiency projects that meet specific criteria.
Partners in improvement
Johnson Controls, Toyota and 3M are just three of the manufacturers engaged in the U.S. Department of Energy (DOE) Better Buildings: Better Plants partnership. Members share performance data and best practices as they find new solutions to meeting energy-saving targets. The Better Plants program also provides tools and training to help new partners improve. The partnership currently includes 157 companies with about 2,400 manufacturing facilities, which represent 11.4 percent of the nation’s manufacturing energy footprint.
Whether through a partnership like Better Buildings: Better Plants or with other paths to comprehensive energy management systems, manufacturers have a lot to gain. New approaches and technologies focused on the smallest sources of energy waste, when added up together, are yielding significant savings. At the same time, saving energy reduces a plant’s carbon footprint, dovetailing with the corporate sustainability goals becoming so important to manufacturers—and their customers, employees, and communities.
Karen Wilhelm has worked in the manufacturing industry for 25 years, and blogs at Lean Reflections, which has been named as one of the top ten lean blogs on the Web.
- Category:
- Industry
- Manufacturing
Some opinions expressed in this article may be those of a contributing author and not necessarily Gray.
Related News & Insights
Manufacturing
5 Lessons in Sustainability Leadership We Can Learn From Toyota
Corporate News
Manufacturing
Why the Carbon Capture Debate Matters to Manufacturers
Industry
The New Face of Manufacturing: U.S. Energy Growth Creating New Manufacturing Opportunities
GrayWay, Industry
May 28, 2014