5 Lessons in Sustainability Leadership We Can Learn From Toyota
Toyota’s continuous improvement process works—small steps add up to big gains over time. This success makes it worthwhile to check in now and then to see what’s new, and what we might learn. I recently took a look at Toyota’s 2014 North American Environmental Report and found some new (and old) ideas any company could learn from.
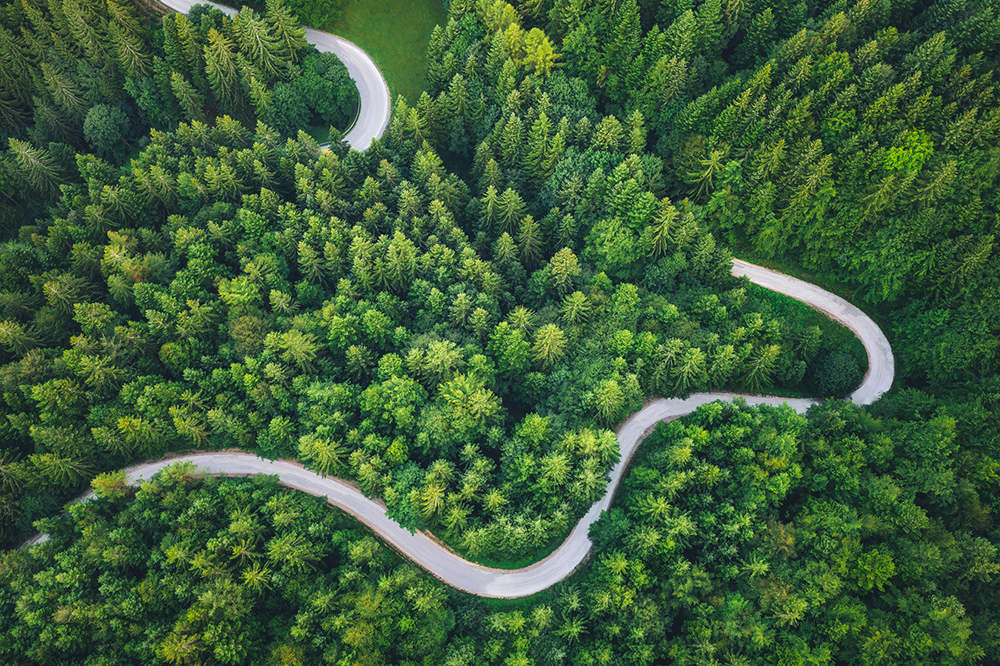
One thing Toyota is known for is its cohesion in corporate strategies, policies and activities. Yet, up to now, manufacturing, R&D, and sales and logistics in North America set separate environmental targets. This year, these divisions are working as One Toyota. In addition to these horizontal connections, the Toyota North American Environmental (TNAE) organization, the chief environmental body for Toyota North America, has been reporting to the top level of management, the North American Executive Committee.
Strategies emerged from methodical assessments performed last year are focused on five core areas:
- Carbon
- Water
- Materials
- Biodiversity
- Outreach
Implementation of the newly refocused strategy can be seen from the new product lineup, to manufacturing operations like casting aluminum wheels, to seemingly insignificant processes like washing cars for the showroom.
Here are a few examples of how Toyota is making strides in sustainability in its five core areas:
Carbon
To continue to reduce carbon emissions, Toyota is introducing a new fuel cell vehicle this year, the Mirai. Consumer resistance to plug-in electric cars will be reduced by giving them longer driving distance capabilities. The hybrid product line continues to grow. Of course, acceptance of such vehicles is limited by lack of a refueling infrastructure. Toyota is working to address this by helping find ways to strengthen the power grid and to develop a hydrogen distribution system.
Carbon also comes from energy use in manufacturing and other facilities—Toyota uses a billion kilowatt-hours of electricity each year, plus natural gas, diesel and gasoline. Significant amounts of energy are required in processes like melting aluminum chips for casting. One Canadian wheel manufacturer was melting about 19,000 metric tons of it annually. Team members there developed a new process that eliminated the need for a holding furnace between the melting and the casting operations. That will reduce natural gas usage by about 220,000 cubic feet and cut 336 metric tons of greenhouse gas emissions per year.
Water
Toyota is known for the “five whys” method of inquiry. Team members at one Toyota vehicle distribution center asked why water had to be deionized to get a spot-free wash. When they tested the hypothesis, they found that they were over-processing the water.
Materials
Heavy metals have adverse environmental and health effects. Parts and accessories in Toyota’s North America vehicles have not contained hexavalent chromium, mercury, lead or cadmium above minimal levels since 2007.
Waste in manufacturing processes is sometimes unavoidable. Metal shavings from grinding processes at Toyota’s engine plant in Alabama make up 41 percent of the plant’s non-saleable waste. To recycle it, they found a company that uses it in making cement. More than 11 million pounds have been diverted from disposal each year.
Biodiversity
130,900 trees have been planted in the last six years on land owned by Toyota Motor Manufacturing, Indiana, creating a thriving habitat for wildlife, including white-tailed deer, red-tailed hawks and bobcats. Elsewhere, employees work to help plant gardens that produce food for local charities.
Outreach
Toyota has updated its Green Supplier Guidelines. They must develop an environmental management system equivalent to that described in the ISO 14000 standard. These are more than just guidelines. Toyota’s environmental expectations will mean the difference between remaining in the Toyota supply chain or not. At the other end of the supply chain, Toyota is encouraging dealerships to use sustainable building practices on new construction and remodeling projects, and to have those buildings certified by the Leadership in Energy and Environmental Design (LEED®) rating system.
Although money is saved from many environmental improvements, it is only a tiny fraction of the total costs of manufacturing. Toyota is used to dealing in fractions, however. In fact, the most significant fractions are the small ones that team members make every day. Through the years, they create a big effect. As Toyota embeds continuous environmental improvement in its core company strategy, it will continue to advance as a sustainability leader.
For more information on Toyota’s the five core areas outlined in the 2014 North American Environmental Report, click here.
Karen Wilhelm has worked in the manufacturing industry for 25 years, and blogs at Lean Reflections, which has been named as one of the top ten lean blogs on the web.
- Category:
- Corporate News
- Manufacturing
Some opinions expressed in this article may be those of a contributing author and not necessarily Gray.