How COVID-19 Is Challenging Manufacturers to Innovate for the Future
COVID-19 is creating economic hardships for businesses, communities, and consumers around the world. The fast-moving pandemic has hit manufacturing especially hard: about 80% of companies that responded to a recent National Association of Manufacturers survey expect negative financial impacts in 2020. In an April 2020 survey, PwC reports that the top concerns for manufacturing leaders are potential global recession (71%), effects on workforce/reduction in productivity (64%), decrease in consumer confidence (40%), reduced consumption (41%), supply chain disruptions (40%) and difficulties accessing capital (23%).
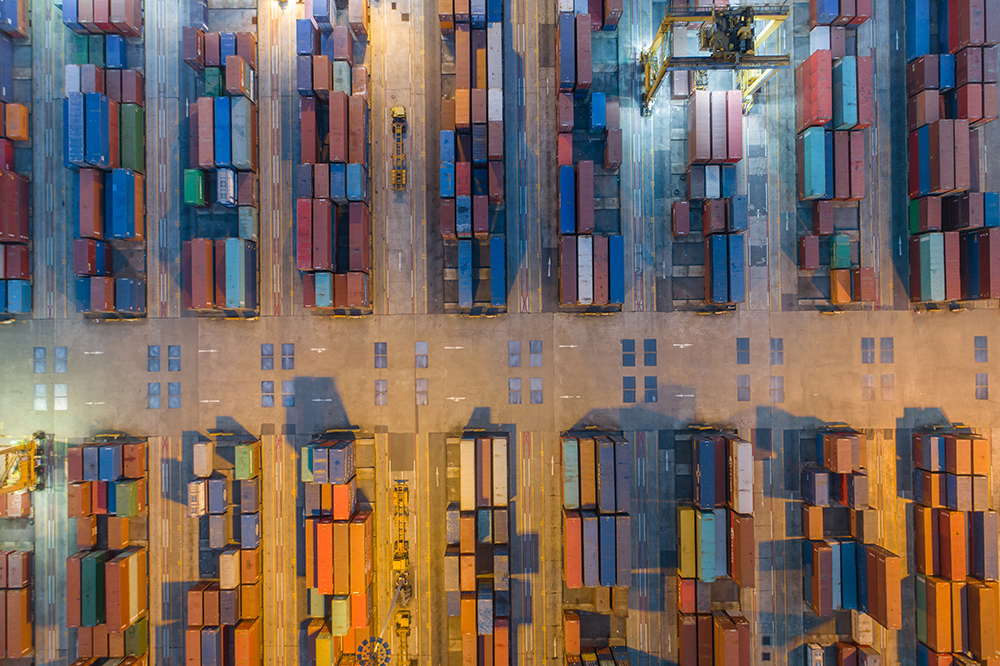
The pandemic has hit manufacturers in a totally unexpected and unprecedented way—”for the first time in modern manufacturing history, demand, supply and workforce availability were all affected globally at the same time,” states Artem Kroupenev, vice president of strategy at Augury, a provider of machine performance software.
Despite this, U.S. manufacturers are finding creative ways to continue operations, and even be part of the solution in defeating COVID-19.
Business is booming for companies that provide and deliver vital goods like personal care, paper, and pharmaceuticals, as well as personal protection equipment (PPE) for those who are fighting COVID-19 on the front line. Hundreds of manufacturers have stepped up to adjust their lines to produce PPE for healthcare workers, as voluntary efforts or through compliance with the federal Defense Production Act.
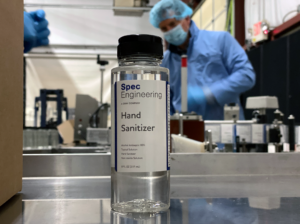
For example, Nordstrom is making face masks and Bacardi is producing alcohol for hand sanitizer. Spec Engineering, a Gray company, has partnered with Sweet Solutions, a confectionery manufacturer, and Sandymount, a technology provider for the brewing industry, to produce alcohol-based hand sanitizer. The operation now produces 30,000 bottles of hand sanitizer daily. Medtronic is working hard to double its production of ventilators for COVID-19 patients. 3M has increased production of N95 masks and Ford is collaborating with General Electric and 3M to discover faster ways to produce PPE and also increase the production of 3M’s air-purifying respirators.
“It is difficult to speculate how the manufacturing sector will look in the coming months or years,” adds Pat Byrne, CEO of GE Digital. “What we do know is that manufacturers are making adjustments, whether it is ramping up essential products or adapting output entirely. This is a trend that was already taking place in the manufacturing industry—being able to more rapidly adapt to changing demand signals.”
Preparing for the Long Haul
For U.S. manufacturing in general, however, many companies are experiencing dramatic drops in demand and are scrambling to find ways to boost efficiency and cut operational costs. “Every major manufacturer is now experiencing disruptions across their supply chains of parts and raw materials, driven by what may now become recurring volatility of supply from South Asia,” states Kroupenev.
Social distancing and employee safety measures are an additional level of pressure on manufacturers; many jobs cannot be carried out remotely and must be performed on-site, which makes social distancing much more challenging.
Of course, worker safety is always a top priority. To increase safety in manufacturing plants, OSHA has issued its “COVID-19 Guidance for the Manufacturing Industry Workforce.” Recommendations include:
- Establish flexible work hours, such as staggered shifts
- Practice sensible social distancing
- Where social distancing is a challenge, implement innovative approaches, such as repositioning workstations or installing plexiglass shields between workstations
- Discourage workers from using other workers’ tools and equipment
- Provide alcohol-based hand rubs containing at least 60% alcohol
- Provide disinfectants and disposable towels for cleaning work surfaces
Another way to minimize close social contact is by creating pods, where a smaller group of employees takes on more roles for a particular task or product line, which minimizes contact with staff and equipment outside the pod. Specialized tasks within the pod, such as quality assurance, can often be conducted by remote specialists, using cameras and digital tools.
COVID-19 will accelerate the adoption of remote diagnostic, management, and collaboration tools. According to Kroupenev, this will result in the emergence of a “virtual shift”—a team of remotely connected specialists that can guide and support the reduced “physical shift” of on-site personnel. “Enabled by real-time data and a range of communication and collaboration tools, the virtual shift will help digitize and scale much-needed expertise across the organization and enable the onsite workforce to become more focused, effective, and ultimately significantly more productive,” he says.
Strengthening the Supply Chain
Most companies already have business continuity plans in place; however, these were not developed to deal with the scope of a global disaster like COVID-19. Typical contingency plans are based on models that simulate disruptions like natural disasters, cyber incidents and power outages. “They don’t generally take into account the widespread quarantines, extended school closures, reduced workforce and added travel restrictions brought on by a global health emergency,” states Jeff Sorensen, industrial products industry leader for PwC US.
In particular, COVID-19 has revealed the vulnerability of supply chains. According to a March survey conducted by the Institute For Supply Chain Management, nearly 75% of respondents experienced supply chain disruptions due to COVID-19-related transportation restrictions.
“The survey also revealed the lack of any semblance of a contingency plan for almost half the companies in case of a supply chain disruption leading back to China, and well over 50% of the companies also reported experiencing sudden, unexpected delays in receiving orders, a problem compounded by supply chain information blackout from China,” says Amitava Sengupta, executive vice president for digital consulting for HCL Technologies, a provider of software and technology services.
Manufacturers are now intently running scenarios and restructuring supply chains to build in more redundancy, with less reliance on a single geographic region. Companies with technology-led (Industry 4.0) business models and real-time access to data tend to be better prepared to respond to hugely disruptive supply-chain fluctuations, compared to less “modernized” companies. Digital approaches to supply chain management include intelligent procurement (letting advanced machine learning algorithms identify trends), automation and analytics and supply chain simulations. More resilient supply chains can be developed through simulations based on business model changes or logistics constraints. “These tools help to validate and identify the best cost-efficient network to achieve the necessary service level across the value chain,” adds Sengupta.
Becoming Resilient
After the Great Recession, McKinsey analyzed the performance of more than 1,000 companies and found that 10% were much more resilient to the crisis than their peers. “They achieved resiliency by creating financial and operational flexibility, cutting costs and building a growth foundation to capture market opportunities at the end of the crisis,” says Kroupenev. “They also invested in software technologies that gave them greater predictability and efficiency, resulting in a significant competitive edge.”
“A resilient manufacturing sector adjusts in real time to emerging global threats by shifting the location of production while minimizing any loss in capacity or product quality,” adds Keith B. Belton, director of the Manufacturing Policy Initiative at Indiana University.
The first step in increasing resilience is engaged management. Referring to a recent article in Harvard Business Review, Belton outlines a three-step plan for manufacturing executives: “Map out your suppliers, including those far up the supply chain, conduct a vulnerability analysis, and develop contingency plans that consider both the costs and benefits,” he says.
Other ways to build resilience into a manufacturing operation include:
- Re-shoring. Bringing manufacturing work back to the U.S. eliminates many supply-chain variables and vastly improves communication and response time among suppliers. Countries are getting involved in reshoring their companies—for example, Japan’s national bank will invest billions of dollars to assist its domestic manufacturers in reshoring production from China. In Congress, Senator Tom Cotton (R-Arkansas) has introduced legislation to re-shore pharmaceutical supply chains, since 80% of active drug ingredients are produced in India and China. “COVID-19 has dramatically revealed the U.S. dependency on offshore manufacturing, especially China,” says Harry Moser, president of the Reshoring Initiative. “I’m getting many calls now from companies that want to know how to fix their supply chains and how to reshore.”
- Invest in skills training. According to a 2018 study by Deloitte, the growing skills gap in manufacturing will leave an estimated 2.4 million positions unfilled between 2018 and 2028 because the available workforce does not have the technology skills required. “The Information Technology and Innovation Foundation recommends that “Congress create a grant program enabling advanced manufacturing education at community colleges that states could use for the acquisition of equipment and faculty recruitment, and couple this with a more generous federal tax deduction for employer-provided education assistance,” says Belton.
- Improve supply chain relationships. Due to the unprecedented scale of COVID-19, many contracts now include a force majeure that allows for such a disruption. “There are several key commitments that companies should require from suppliers during the disruption,” reports Supply Chain Digital. “Executives should ask themselves: How are we dealing with short-term changes? How can we ensure supply safety and supply priority? What if prices are changing rapidly? What happens if volumes are committed? “How are business risks shared?”
Moving Toward a New Normal
For over a century, U.S. manufacturing has had a way of emerging from a major economic crisis (for example, the Great Depression and Great Recession) stronger than before, led by innovation and creative thinking, to create jobs and drive the economy forward.
COVID-19 is no different. The pandemic has created a series of tough challenges for manufacturers, including global supply chain disruptions, trade barriers, liquidity issues, and shifting consumer demands—with the overarching need of making good decisions quickly. Once the pandemic ends, manufacturers will face determining their “new normal.” Out of the many technical and manpower adjustments that were made, which ones will become part of standard operations or even represent the critical “jump start” for companies that were reluctant to embrace Industry 4.0?
“The post-COVID world will see digital technologies playing a critical enabling role in delivering improvements through all levels of manufacturing, such as more resilient supply chains, enhanced user experiences and optimizing technologic processes to deliver business outcomes,” says Sengupta.
Greater connectivity, data analytics, and real-time communication will mean more rapid deployment of Industry 4.0 across the value chain. Key technologies include robotics and automation, artificial intelligence, sensing, data analytics and modeling, remote collaboration tools and artificial intelligence-based insights—all of which increase a company’s resilience by allowing executives to make quick, informed, real-time decisions. Perhaps the greatest value for manufacturing coming out of the COVID pandemic is how quickly technology deployment could level the playing field—this is especially for small and mid-sized companies, who can now move into the Industry 4.0 world with greater confidence and expand into new markets with clarity.
Some opinions expressed in this article may be those of a contributing author and not necessarily Gray.