Foreign Firms See Positive Impact Manufacturing in the U.S.
New technologies, infrastructure improvements, and staying close to customers are reasons why.
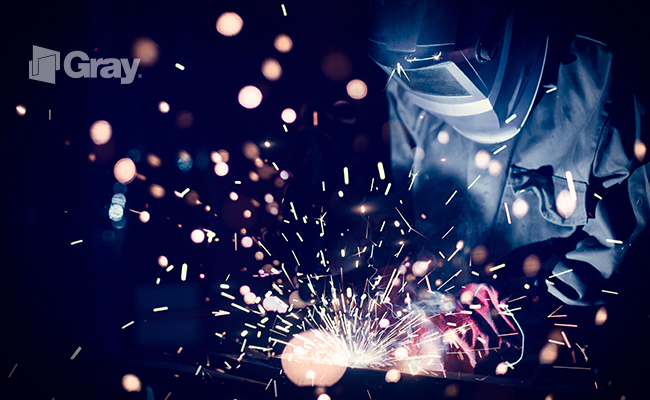
Following security-based travel bans and clear warnings of new tariffs or “border taxes” on imports, the ongoing flurry of executive orders and pronouncements in the early days of the new U.S. administration is being interpreted by many observers as a general pulling back on globalization.
That interpretation would be wrong. With the economy and the stock markets riding record highs, major manufacturing firms around the world are taking decisive steps to establish U.S.-based facilities to serve the Western Hemisphere’s most dynamic marketplace.
Hiring and Expanding
Fuyao Glass is the largest supplier of automotive glass in China. But Fuyao Group CEO Cao Dewag firmly set his sights on the U.S. to establish what he calls the world’s largest automotive glass manufacturing plant. In 2014, he secured a closed SUV manufacturing plant in Dayton, Ohio, and began investing $200 million in its rebirth. In 2015, the company began shipping glass from the Dayton plant several months ahead of schedule and has doubled its need for employees in its first year. Current production is approximately 8 million windshields and integrated car sets (windows and sunroofs) evenly split between OEMs and aftermarket customers. Riding the wave of new car sales records over the last two years, Fuyao is projecting the need for 2500 additional jobs over the next decade with significant new investment to come.
In January, Taiwan-based Foxconn, the world’s largest contract electronics maker (think Apple iPhones), said it was considering setting up a Pennsylvania-based manufacturing plant for television displays. Chairman and CEO Terry Gou said the United States had no panel-making industry but that it continued to be the second-largest market in the world next to China for televisions. Investments would be in the area of $7 billion and create 30,000 to 50,000 jobs.
Both Fuyao Glass and Foxconn share a new manufacturing fact of life. China is no longer the low-labor-cost target it was in the closing decades of the 20th Century. The country continues to rapidly modernize, which brings along with it higher labor wages, increased regulations, and rising shipping and logistics concerns. Where the U.S. remains an expanding and dynamic economy, it makes eminent sense for global manufacturers to locate there to be close to customers.
Behold the Speedfactory
Germany-based Adidas, known globally for sports shoes, clothing, and accessories, is taking the concept of being close to the customer to a whole new level. From design to appearing on store shelves, new shoes can take up to 18 months to complete and ship. Add that up to 75 percent of new shoe designs are on sale for less than a year, and that runners and fitness enthusiasts want better fit or ideally custom features, and the old way of making tennis shoes is intolerable.
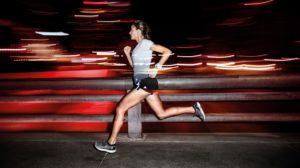
“For years our industry has been playing by the same rules manufacturing product remotely in Asia,” said Adidas Group Executive Board Member Eric Liedtke, responsible for Global Brands. “As the creator brand that challenges convention and looks to co-create the future with our consumers, we are obsessed with bringing all steps of the creation process home to America. We’re fueling design at the ground level of creativity in Brooklyn and reinventing manufacturing with the first Adidas Speedfactory in Atlanta. This allows us to make product for the consumer, with the consumer, where the consumer lives in real time, unleashing unparalleled creativity and endless opportunities for customization in America.”
Adidas instituted the Speedfactory concept in Anspach, Germany, in 2015. The goal was to radically shorten the time it takes to manufacture shoes using a combination of software-based integrated computer-aided design and computer-aided manufacturing (CAD/CAM), robotics, knitting machines for uppers, and 3D printers for soles and other features. Company officials state that the production process will drop from months to less than a week and can ramp up to half a million shoes per year. Adidas ships a total of 300 million shoes per year.
“Speed is far more than a business strategy for us,” said Adidas Group Executive Board Member Glenn Bennett, responsible for Global Operations. “Speed is all around us. It’s what athletes train for, and it’s essential to our consumers who live in a world of immediacy. With the first U.S.-based Speedfactory, we’re combining some of the world’s best technology and manufacturing processes to give our consumers access to constant newness. This is another big step in our ambition to become the world’s first true fast sports brand.”
The more than 74,000-square-foot Atlanta factory will be fully functional in the second-half of 2017 and create around 160 jobs, the company says.
Ray Chalmers is founder and principal writer at Chalmers Industrial Communications Inc., assisting manufacturing technology providers and users by providing tech features, customer success stories, newsletters, op-eds, and other content services. He is based in Canton, Michigan.
Some opinions expressed in this article may be those of a contributing author and not necessarily Gray.