Footwear Leader Discusses Manufacturing in Today's Global Economy
Running a business in turbulent economic times is no easy task, but leaders across the globe are taking on this challenge… and succeeding. Clarks Companies, N.A. President Jim Salzano discusses the state of the global economy and its affect on business, the ripest markets for manufacturing growth, and other issues facing today’s global manufacturers.
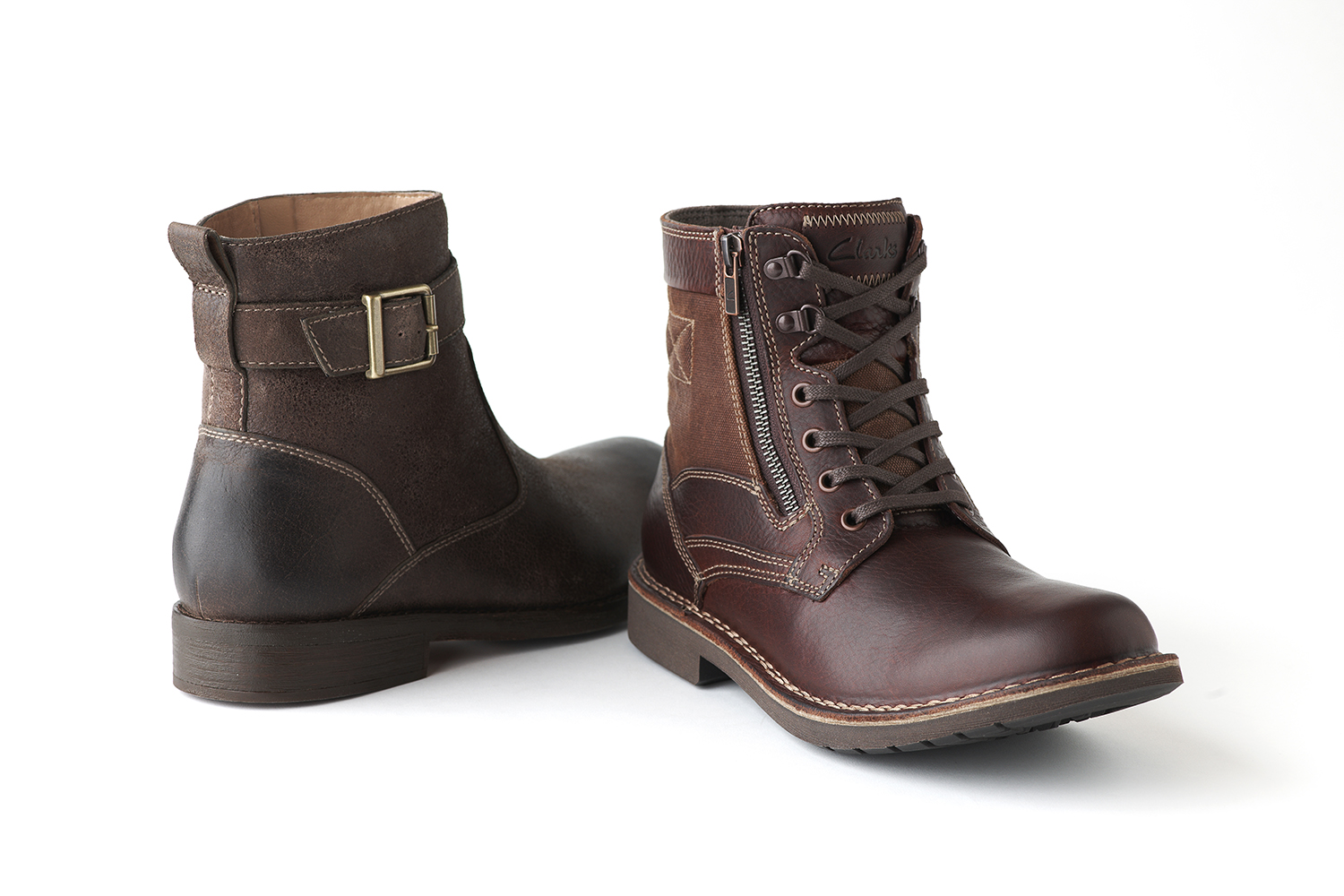
A Q&A with Jim Salzano, president of global footwear manufacturing leader, Clarks Companies, N.A.

Q: What strategies did Clarks use to persevere over the recent U.S. recession?
A: We tried to exercise the best leadership and judgment we possibly could—that’s something we consistently do at Clarks every day, no matter if we are in a recession or not. One thing I think we do well is lean into situations—we lean into conditions and look to exploit them or take them as opportunistic. Let’s take 2008 when the U.S. debt crisis fully emerged. Yes, we had to do things differently, but we didn’t go into a show. We reduced headcount by offering people an opportunity to leave the business early, and we came up with a program to do that, which is really consistent with our culture. We took very good care of our people because we anticipated a downsizing in the market for a while. Nobody really knew what was going to happen. Then, we leveraged the strength of our balance sheet by making sure we were doing everything we could to help our customers through this difficult time. We added marketing resources, field people, and inventories. We extended credit lines and really enriched and built the partnership during that period when a lot of our competition was pulling back—they responded to the recession in a very classic, traditional, natural way, whereas Clarks went out and invested in our partnerships.
Q: There has been a lot of buzz about the U.S. economy inching toward recovery. Have improving conditions in the U.S. counterbalanced the European economic crisis in terms of sales for your company?
A: Clarks is spread out all over the world, across 33 different countries. I oversee the America’s, which, right now, is predominantly North America. Over the last 17 years I’ve been with Clarks, I’ve observed that the benefit we have as an organization is our diverse global footprint. So while things seem to be strong in one part of the world, it tends to come at a time when things might not be so strong in other economies. Right now—with what is really an unprecedented crisis in Europe—we continue to deliver strong results in the North American and Asian markets. That certainly helps mitigate some of the challenges we’re facing in Europe, and in our UK Republic of Ireland region as well. In North America, we’re going to have another record year in 2012, which would certainly help to offset the challenges that we’re having primarily in Europe and the UK. The year 2012 will again demonstrate the power of our diverse geographic portfolio.
Q: As a global manufacturer, what are the ripest markets for manufacturing growth?
A: To be clear, there are challenges in terms of our sourcing strategy that we’ve never had to deal with before. Basically, two things are happening: first, there are challenges in getting the right amount of labor into manufacturing in China. People are moving on from wanting to be in footwear manufacturing to other things as the standard of living changes there. Secondly, because costs are rising, it’s making it less attractive for many who are investing in manufacturing to continue to do so. So the amount of investment—for footwear manufacturing at least—isn’t at the same level it was just ten years ago. We’ve actually seen deflation in our segment of the footwear market for the last ten or so years. Over the last three years, the pressures have started to build, and we finally had to make increases.
With that said, things are developing in India and Vietnam. We are looking at the Dominican Republic, and Mexico has been talked about. The U.S. is starting to become a place for companies to produce footwear. We aren’t (manufacturing in the U.S.) right now, but there are companies in our industry that are investing in manufacturing in America. The reality is, consumers are really dictating the choice in a large way because of their willingness to, and the alternatives they have in terms of price points in the marketplace. In order for us to preserve or even offer an expanded value proposition, sourcing strategy is a big part of that.
And today, essentially everything is produced outside of the two primary countries in which we operate: the UK and the U.S. These countries used to have very significant manufacturing infrastructure. We closed our last factory in the U.S. around 2000. So I think the economic rise of China is going to offer tremendous opportunity to people in other parts of the world to enjoy new employment opportunities.
Q: Advances in manufacturing are continually changing how manufacturers make products. What countries are doing the best job of supporting and nurturing advanced manufacturing practices and initiatives?
A: Some of the companies in our industry are looking at the U.S. because technology has changed, and it’s taken the labor content out, and so it’s made manufacturing relatively more efficient than before we moved it out of the country. In China, investors who have invested in this long-term infrastructure are looking to make their manufacturing processes more efficient. China is beginning to look like what I saw during the last ten years of manufacturing in the U.S. when a lot of technology was invested to keep manufacturing here, and to make it more efficient by taking the labor content out. Still, (the U.S.) couldn’t compete with the rest of the world. But now, you see China very interested in taking labor content out, increasing the efficiency of the labor process, and using technology to do that as well.
The automotive industry has really benefitted from advancements in technology, automation and robotics. It’s really fascinating. I haven’t seen the real game changer in the footwear industry, but there are things companies are doing to leverage existing technologies.
Q: What’s your opinion about changing the immigration laws to allow more degreed people in science and engineering to start migrating to the U.S. to utilize their skills in our manufacturing companies?
A: The one thing that makes us different as a country is we tend to be the problem solver for the rest of the world. And, we do tend to be a country of compassion and care. So when I hear about the children being deported or the parents of children being deported, it just seems obtuse to me. But, I think we should be encouraging talent and expertise to reside in the United States, yet what we do is we encourage it to be exported, so they come to school here, and it’s very difficult for them to stay here. I think that’s counterproductive. As far as sound economics goes, I think we should be doing more to encourage the greatest minds and thinkers and innovators to be residing here to create opportunities for more Americans, and I don’t care where they come from to do that.
Q: Do the threats of large tax hikes on U.S. consumers, or what some are calling the “fiscal cliff,” concern you?
A: No, it doesn’t. You can never count America out of anything. We have an economic system, a government system, and a rule of law that works. We encourage entrepreneurship and innovation. I think the fiscal cliff is mostly a by-product of the fact that we’re in a presidential election year. That’s not to dismiss that we need to be fiscally responsible, but in the end, the United States is a country that many look to for solutions to problems. Carrying that burden comes with some costs but the fact remains, the potential in the United States is significant. I’m confident that this fiscal problem in the end will be sorted out.
Q: Beyond sourcing issues, what other issues face global manufacturers today?
A: I think there are a lot of challenges today that didn’t exist years ago, like corporate social responsibility, which is a really good challenge. It’s only been over the last 10-to-15 years that manufacturers have taken notice of their corporate social responsibility—protecting the environment, protecting workers. When outsourcing came along, some of the benefits to this option came from the lack of regulations relative to the regulations existing here in the U.S. I’m very happy to see more attention being brought to caring for the environment no matter where that environment may be, and caring for workers whether they’re outsourced or insourced. In the footwear industry, we have people working in factories that are part of another company, but that doesn’t mean that they’re not part of our industry—we still need to care for people as an industry. We have an obligation, no matter where they are in that value chain. We have to take a bigger stance on that, and we do at Clarks. We spend a great deal of time working with our suppliers so they understand our expectations and requirements. We spend a lot of time monitoring the working conditions within factories, and we have people monitoring not just quality of product, but the quality of work life for our employees. And then, we move production without regard to cost advantage if a supplier can’t meet those requirements. We spend a lot of time on this because it’s very important to us and to our shareholders. The problem with that, however, is the penalty isn’t for the factory owner, but the people who lose their jobs when we leave. So we work really hard to remedy the situation because, in the end, it mostly affects the people who rely on that income to support their families.
Another challenge is managing really complicated and intricate supply chains that have lead times that domestic manufacturers and people who are being supplied by domestic manufacturers never had to deal with before. Being able to be responsive to your consumers with lead times that are significantly longer than they used to be is a challenge that we’re constantly facing as well.
- Category:
- GrayWay
Some opinions expressed in this article may be those of a contributing author and not necessarily Gray.