Food Safety in the Time of COVID: 6 Steps to “Error-Proof” Your Plant
Throughout most of 2020, food safety and processing concerns mainly revolve around how to safeguard the public and employees from the coronavirus. However, there are still day-to-day operational considerations that must be addressed—especially with the heightened awareness and caution caused by the need to protect everyone in the midst of a pandemic.
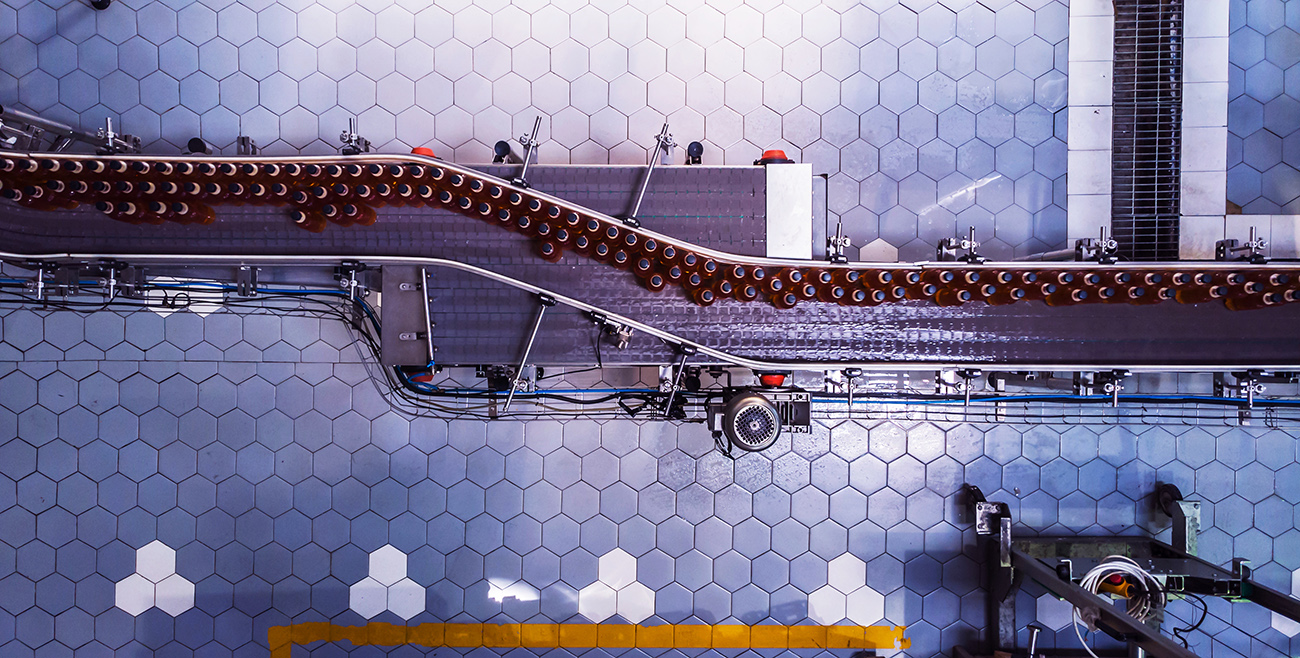
Processors still must be mindful of all the hazards to their employees’ safety and health, such as sanitation, slip and fall injuries, as well as electrical and mechanical hazards. A recent article in Food Engineering, for example, points out that “cleaning is not only an important part of fighting coronavirus, but also a safety consideration, due to the potential for slip and fall injuries, as well as foodborne pathogens and other concerns.”
There is no other industry, other than healthcare, perhaps, that could be considered as essential as the production and processing of food. So, while the pandemic might be top-of-mind, the food industry must continue in a “business as usual” model. And, even as many of the country’s workers are now working from home, that is obviously impossible in the F&B industry.
Adding to the issue is the increased demand most processors are now facing. A huge part of food processing must include protecting employees, while meeting production requirements. The essential problem is how to ensure employee safety, reduce possible transmission—and keep a healthy business/work environment.
Make Your Plant Floor “Error-Proof”
A recent webinar sponsored by Plex and presented via BNP Media entitled “6 Ways to Error-Proof Your Plant Floor” illustrated some of the ways F&B companies can help mitigate risks and ensure safety for all involved in production.
“A Manufacturing Execution System (MES) that ‘operationalizes’ production processes with fundamental error-proofing protects your business from errors,” began the webinar. The logic is that a single MES application keeps the data in one database—meaning dispatched jobs are linked to a master production schedule. This includes process routings, production operations, labeling requirements, and more. The quality inspections for the plant are also linked to the central control plan. This makes it easier and more accurate for reporting and helps eliminate human error.
“Rely on a Single Source of Truth”
Plex’s simplified data-gathering and data-management at all levels helps companies adhere to the first of the six ways to error-proof: “Rely on a Single Source of Truth.”
“Apply Rigorous Track & Trace Methodology”
A robust, accurate track and tracing methodology is extremely important for governing and monitoring how operations are going. The second way to error-proof, then, is just that: “Applying Rigorous Track and Trace Methodology.” Use of such technology as barcode scanners and printers enable users to record and document every step—from receipt to inspection. This helps to ensure “an accurate record of who did what and when. For every action on the shop floor, there is a transaction in the system. Using the single database with pre-defined process workflows, each step is validated before the system allows the next step to occur, making it fast and easy to trace backward or forward to find any issues, contain the issue, and provide required documentation.”
Data no longer needs to be hunted down from one source to the next. Instead, it can be easily accessed to help management make informed, proactive decisions.
Control Production; Control Compliance
“Ensure Production & Quality Control”
Production and quality-control assurance is the third step in the error-proofing process. By tying operations to a production control plan, you can provide evidence for a customer to approve. This ensures that whatever error-proofing control mechanism is in place has a built-in “check and balance” system. As stated in the webinar: “Each operation has defined input materials, work center machines, tooling, and inspection procedures and frequency—to ensure that no out-of-spec material or equipment is used.” In addition, alerts can be sent to supervisors automatically, should anyone attempt to override or go around the control plan: “Activities are recorded directly at the work center and are immediately available throughout the business for analysis by quality managers.”
“Enforce Customer & Industry Compliance”
The fourth step involves enforcing the compliance of both industry and the customers. Compliance from both, regarding industry requirements and regulations “requires a significant amount of work and rigorous management. A system that takes the risk out of compliance can provide peace of mind for company leaders who are accountable for, but not necessarily in control of, compliance procedures.” This can involve such things as “lockouts,” i.e., not allowing an operator to complete a task or record an item unless required checklists have been adhered to.
Digitalization Means Freeing Up Employees
“Automate Production Transactions” and “Free Up Employees from Mundane Tasks”
The fifth and sixth steps in the error-proofing “playbook” both deal with the concept of making better use of employees’ time, while also making sure tasks that can and should be automated are done so productively. The lightning-paced adoption of digital tools makes it even more important (and easier) to connect and collect data from production equipment.
As stated in the webinar: “There is perhaps no greater error-proofing investment you can make than automating the recording of machine uptime (availability), production output (performance), and scrap or waste (quality) and the associated reason codes. These metrics combine to produce an overall equipment effectiveness (OEE) rating that plant leaders and executives use to measure plant performance. If any of those measures are adulterated by human error, the entire OEE number is incorrect and could result in wasted effort trying to improve it.”
Automation of machine uptime (availability), along with production output (performance) and scrap or waste (quality)—combined with the associated reason codes can be a great investment in error-proofing. The combined metrics can lead to overall equipment effectiveness—and reduce wasted effort due to human errors.
Automation and digitalization means the freeing up of workers from having to do mundane, repetitive tasks. Ending reliance on manual, paper-based processes can not only free employees’ time for more productive tasks—it can also ensure the business is less at risk from error-prone, outdated processes. A system that “positions control panels throughout your facility allows employees to log in to record their hours, track job status, and monitor job costs in real time.” It is also easier to monitor employee training and certification for certain jobs to ensure worker safety, reduce damage to equipment, and reduce raw material waste.
In Summary
Such change can bring with it a foundation of visibility—along with a better understanding and control of inventory and increased operational efficiencies. It also helps to reduce human errors and improve the quality of the product—by the early identification of production errors. And, F&B production in the time of COVID means keeping errors to a minimum and safety at maximum velocity.
- Category:
- Industry
- Construction
- Food & Beverage
Some opinions expressed in this article may be those of a contributing author and not necessarily Gray.