Expanding the Life of Lithium-Ion Batteries through Research and Recycling
Using lithium-ion batteries in electric vehicles (EV) is a huge factor in reducing greenhouse gas emissions. Analysts predict electric vehicles have the potential to reduce emissions by 50% when compared with gas-powered vehicles. Because EV cars reduce the need for gasoline as a fuel, they also lessen the overall environmental impacts resulting from the processing of petroleum into gasoline.
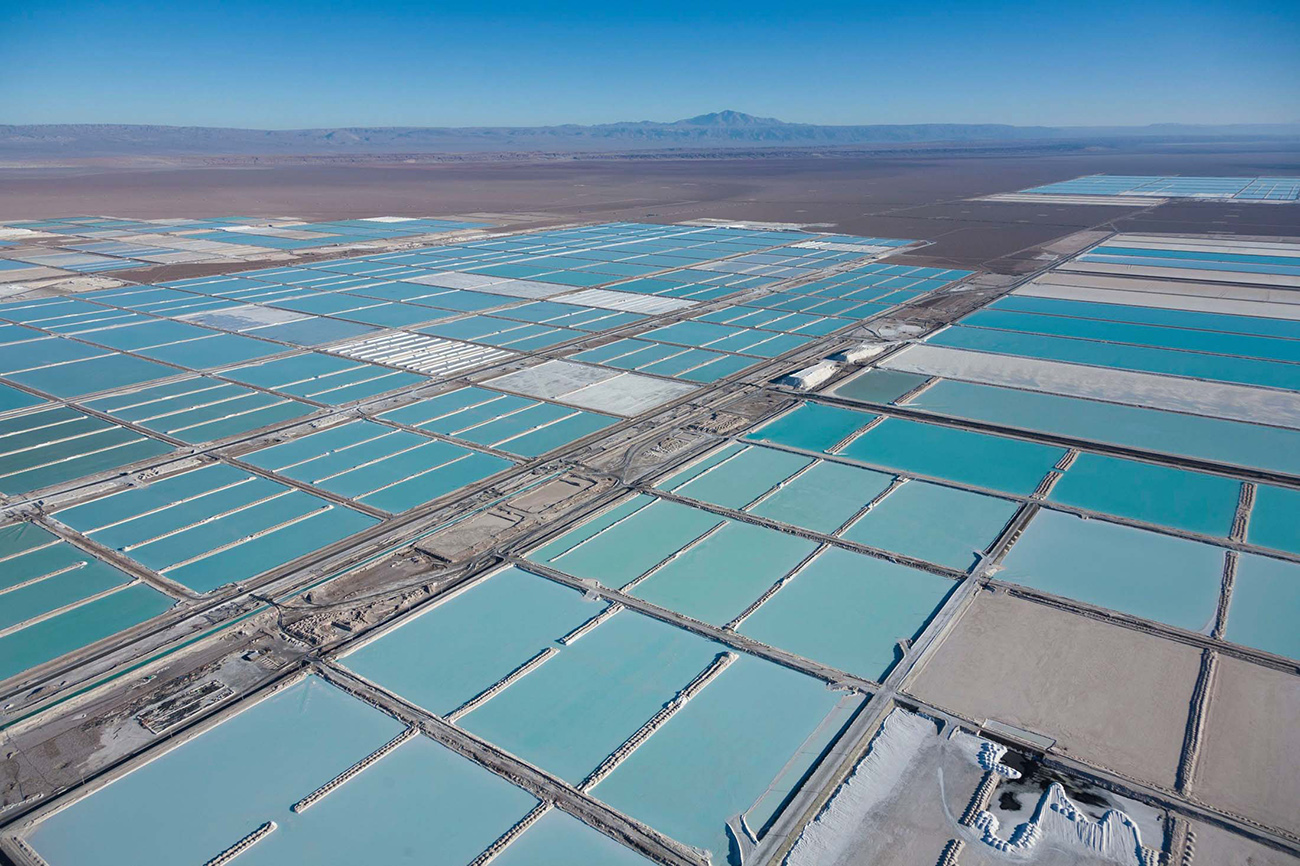
As more people drive electric vehicles, there will be a huge increase in depleted lithium-ion batteries in the coming years, as well as a pressing need for new ones. Industry analysts predict that more than 11 million metric tons of these batteries will reach the end of their service life by 2030.
It is, however, challenging and costly to recycle these batteries. Due to current technical and economic barriers, less than 5% of these are recycled today, with many of them simply thrown away in landfills.
The multi-stage recycling process involves collecting the used batteries, burning off the flammable components, neutralizing the battery, smelting, refining, purification, and disposal of remaining waste. Some of these steps also utilize toxic cleaning solvents. Once the battery is completely broken down, the valuable materials are recycled—largely cobalt, lithium, and nickel.
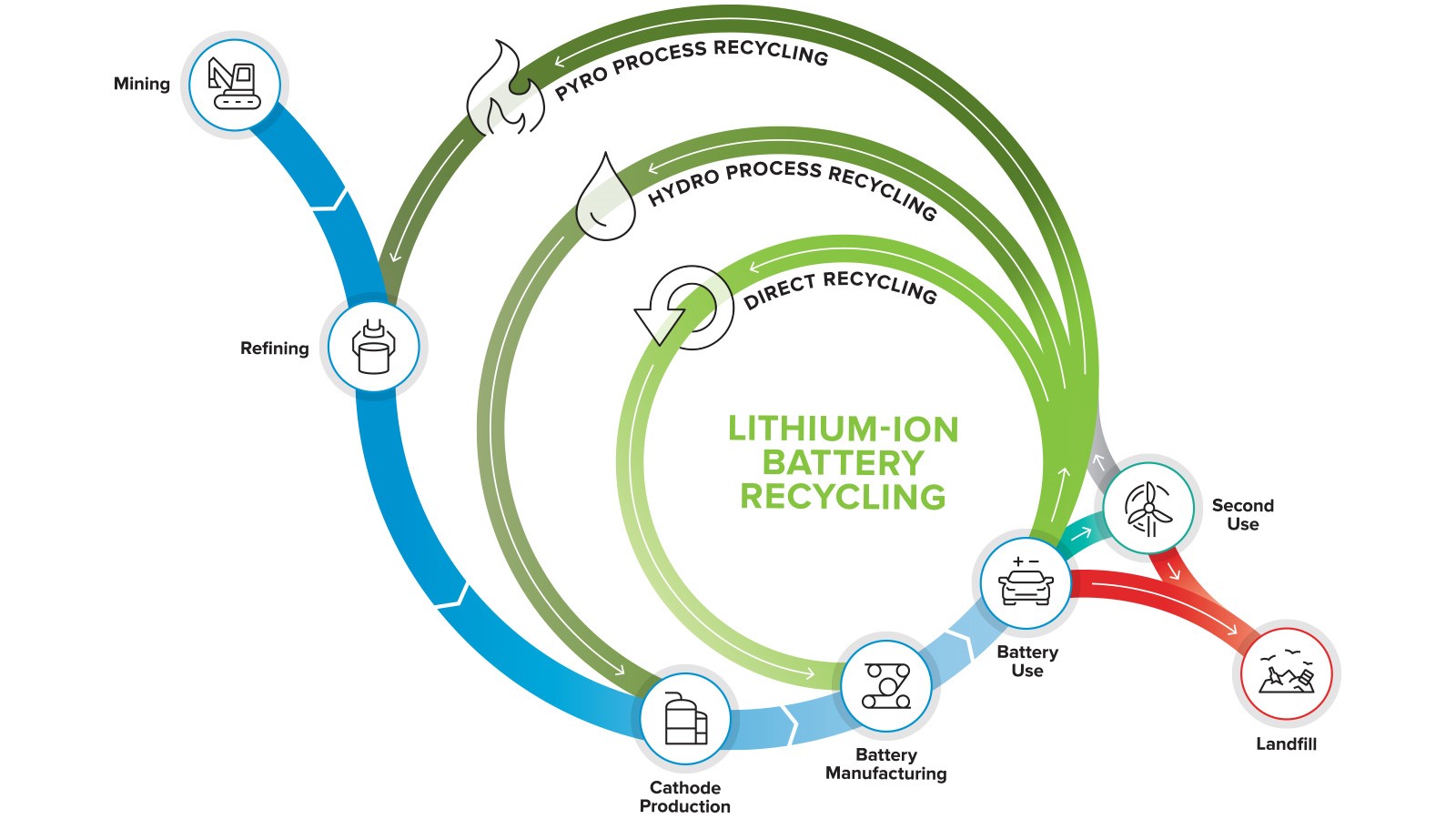
A big challenge is that most recycling companies do not have the resources or time to complete this complex process and still generate a profit; therefore there is an extreme shortage of facilities in the U.S. that can recycle these batteries.
There are also global environmental and social consequences to not being able to recycle lithium-ion batteries. Because these materials are not being recovered through recycling, mining operations are under pressure to produce more lithium, cobalt, and other heavy metals used in these batteries. Most lithium production occurs in the “Lithium Triangle,” an arid region located in Bolivia, Chile, and Argentina. Lithium production consumes huge amounts of water, depleting the water resources for the local communities.
Extending the Life Cycle of Lithium Batteries
Lithium-ion electric vehicle batteries started gaining popularity 2011; because these batteries usually last about eight to ten years, there has been little demand to invest in recycling centers that can efficiently recover lithium and cobalt. Over the coming years, expended batteries will continue to be dumped in landfills or shipped to China. Thus, it is important to develop domestic capacity for recycling these batteries. This includes modernized infrastructure and recycling processes (less complexity, lower cost) and building more centers.
Battery manufacturers can improve the situation by moving away from chemistries that contain cobalt and other toxic materials. For example, York University researchers have created a new carbon-based organic molecule that can replace cobalt in the cathodes of lithium-ion batteries, without sacrificing performance, stability, and storage capacity. “Organic electrode materials are extremely promising materials for sustainable batteries with high power capabilities,” says York University researcher Thomas Baumgartner.
To drive innovation in lithium-battery recycling, the U.S. Department of Energy (DOE) launched the ReCell Center at Argonne National Laboratory in Illinois in February 2019. Funded by DOE’s Office of Energy Efficiency and Renewable Energy, the $15-million lithium-ion battery recycling research center is focused on perfecting methods for recycling the components of these batteries, making it more profitable to run recycling centers in the U.S. This includes eliminating the use of toxic cleaning materials from the recycling process. Key research areas are direct cathode recycling, recovering other materials, design for recycling, and modeling and analysis.
By 2022, ReCell hopes to launch pilot-scale demonstrations of new recycling technologies that can translate to commercial adoption. “The pivotal discoveries we are making in recycling processes and battery designs will increase the global competitiveness of the U.S. recycling industry, reduce battery costs for consumers, and increase national energy security by limiting our reliance on foreign sources for these materials,” says Jeff Spangenberger, group leader for materials recycling at ReCell.
- Category:
- GrayWay
- Construction
- Manufacturing
Some opinions expressed in this article may be those of a contributing author and not necessarily Gray.