Enabling the IIoT: Collecting Data, Eliminating Pain Points
Operation improvements surge with flexibility options
Each and every plant operation sits on a rich mine of data that it can collect for its own continued improvement, but only a small percentage has an IIoT-enabled strategy in place. A significant drawback is efficiently gathering and compiling that data from different makes and models of machines and controls. This challenge has been likened to a permanently ongoing United Nations meeting with no translators.
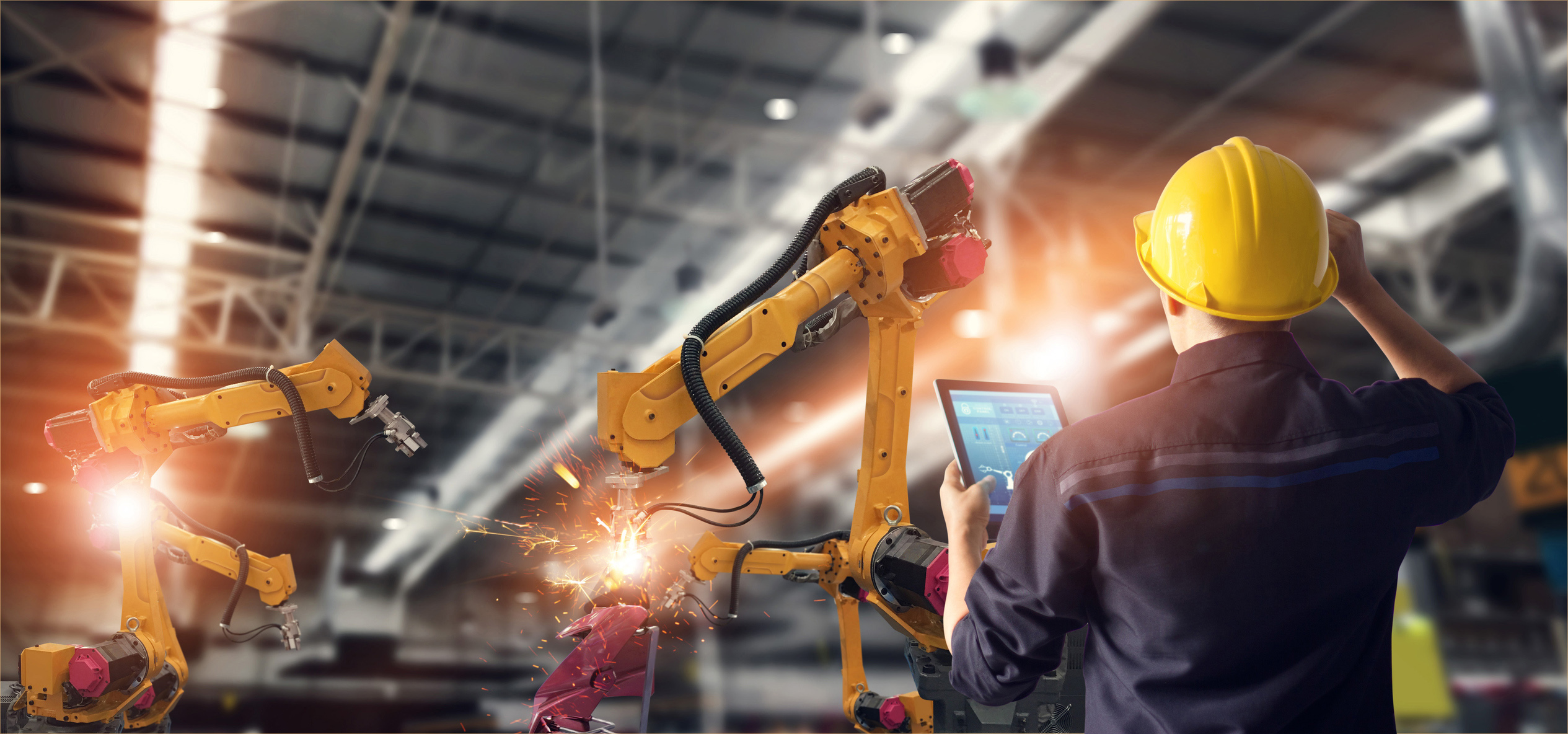
Concepts for gathering data from the shop floor have been around for decades, but recent advances in standards and infrastructure technology have allowed manufacturers to mine data at the speed of their operations. The development of standards such as Common Industrial Protocol, PackML and MTConnect allow equipment manufacturers and integrators to speak the same language. Implementation of Ethernet communication on the plant floor also allows machines to connect directly to their IT counterparts without expensive and complex translators. This means faster speed to market for changes and greater flexibility as business needs evolve.
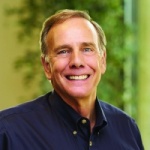
Yet many pain points remain. Don Pearson, chief strategy officer for Inductive Automation, an industrial platform provider in Folsom, Calif., says, “Connectivity was prohibitively complex and expensive in the early days.” Language, for example, can make a big difference. Systems for collecting data traditionally have used supervisory control and data acquisition (SCADA) systems. But over the last 15 to 20 years, many manufacturers have standardized corporate databases, enterprise resource management and manufacturing execution systems on structured query language (SQL). While it is possible to integrate SCADA with SQL databases, this architecture is not an ideal data logging solution for multiple reasons, experts say.
First, traditional SCADA middleware is complicated to implement, maintain and repair, even with assistance from in-house IT specialists or outside consultants. Second, because these middleware systems do not provide a direct database link, they consume cycle time and reduce production efficiency. Last, constant maintenance is required to ensure these operating systems and hardware remains operational, current and free of security vulnerabilities.
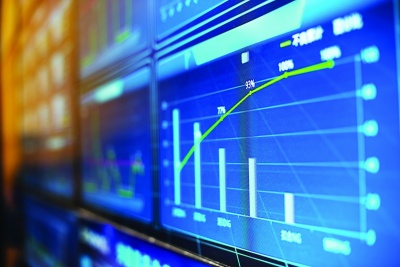
“Now, plant connectivity is delivering information technology results with an operations technology mindset,” Pearson says, likening modern industrial connectivity platforms like Inductive’s Ignition to a Swiss army knife, providing modular solutions for familiar pain points up and down manufacturing operations.
For example, many systems can’t customize front-end user interfaces without hacking the program. “Ignition is one system that gives users the tools to easily develop almost anything,” Pearson answers. Through cross-platform functionality, built-in support for established and open industrial network standards and integration of relational databases like SQL, these systems provide tools and flexibility that manufacturers need, points out Pearson.
And where connectivity projects of the past were time-consuming and required significant downtime, new platforms deploy in minutes. Furthermore, hot-pluggable modules allow adding particular functionalities without shutting down systems.
Naturally, cost and memories of IT false starts are notable pain points for manufacturers. “Where software in the past was sold by the individual seat, today it is a server license, so manufacturers can download it and engineers can start applying applications right out of the box,” Pearson says. “Customers can start connecting devices and not connecting apps.”
Visibility Means Reliability
All this connectivity potential is changing manufacturing operations as well. Machine tool builders, tooling providers and all sorts of technology providers are building the IIoT connectivity into production equipment. “Assuming longevity and reliability exist at the foundation – the machine tool – process improvements can ensue on the march toward efficiency improvements and cost savings,” says Scott Walker, chairman, Mitsui Seiki USA Inc.
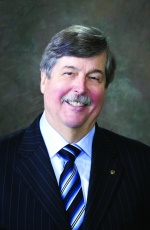
“Advances in controls, software and connectivity mean users can look at all aspects of machine functionality, part geometry and tool life in real time. As one customer said to me, in the end it’s all about reliable monthly output. The goal is to get workpieces in, consistently process them (unmanned if possible) and get finished parts out. How does that happen? With systems, connectivity, and process reliability built-in from the foundation up.”
Convergence will continue, processes and products will improve and the IIoT is the infrastructure.
Some opinions expressed in this article may be those of a contributing author and not necessarily Gray.
Related News & Insights
Distribution, Construction
Manufacturing Convergence and the Industrial Internet of Things
GrayWay, Industry
July 11, 2018The Positive Disruption of the Internet of Things on Distribution Systems
Industry, Opinion
Food & Beverage, Engineering
The New Face of Manufacturing: InLine Engineers
GrayWay, Industry