Digital Twins: An Emerging Force in the Digital Economy
With the Internet of Things (IoT) and Industry 4.0, the physical world continues to merge with the virtual world. In a “smart” facility, all the critical equipment, processes, and systems are connected through sensor technologies, creating volumes of operational data than can optimize how the facility is managed.
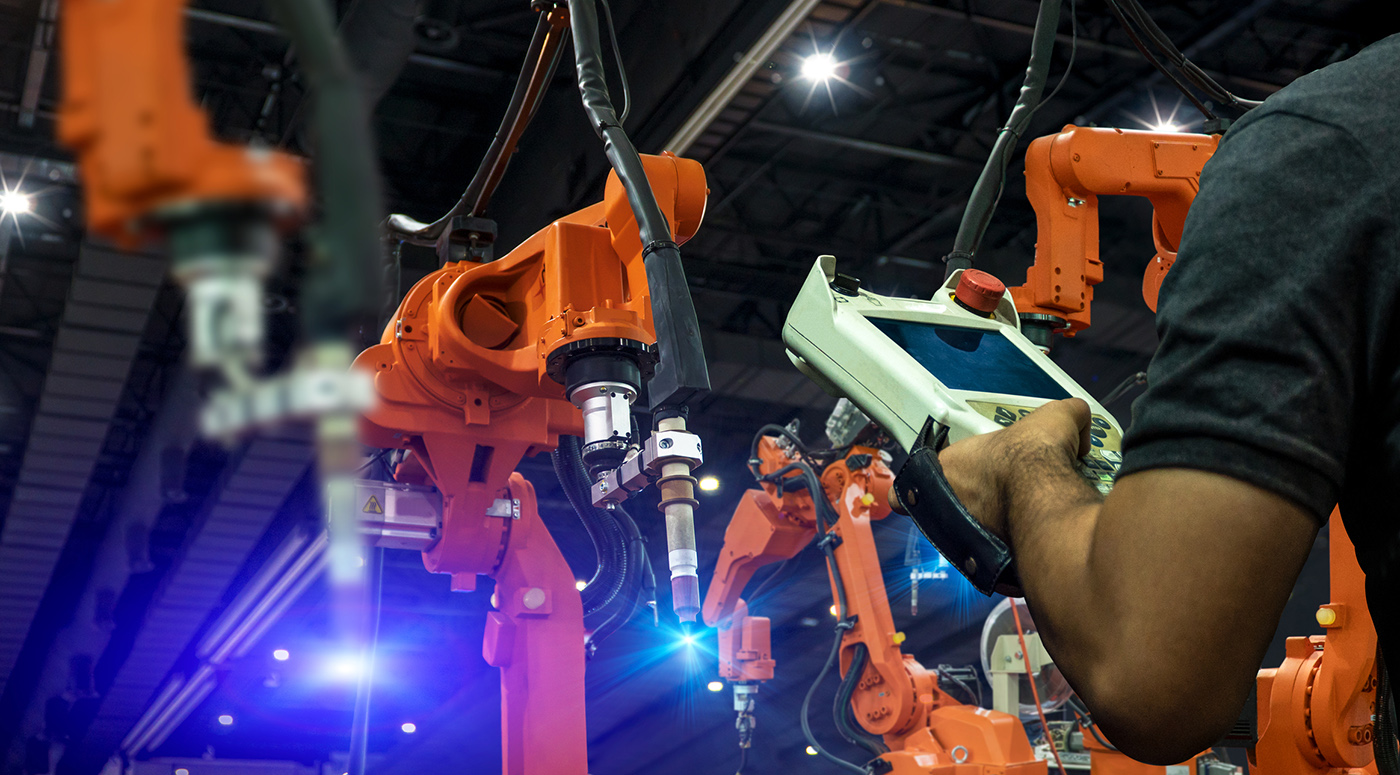
This data can also be used to build a “digital twin.”
A digital twin is a digital (virtual) detailed “copy” of an existing object. The twin contains all the data that is relevant to its original. A digital twin can also represent a person, process, system, supply chain, or an entire business ecosystem—the twin is only as detailed or intricate as information coming from the arrays of sensors that monitor that original object.
“Digital twins can keep on collecting data during a product’s operational lifetime,” says Dirk Hartmann, a leading expert on digital twins and simulations at Siemens Corporate Technology. “This can be information about physical stresses, components that have failed, or how an object—whether a milling machine, an aircraft, or a building—is used. Such information supports optimization during operations and also aids designers, architects, and engineers in preparing the next generation of a product.”
When the concept of “digital twin” was first introduced about 20 years ago, few companies were interested because the data required could not be easily gathered and analyzed. Now, with IoT and big data, digital twin technology is becoming more widespread. Deloitte indicates that the global market for digital twins is expected to grow at a 38% compound annual growth rate to reach $16 billion by 2023.
“Digital twin technology is expected to reach its tipping point in the next three to five years, considering its widespread adoption across the industrial manufacturing domain,” adds FutureBridge, a business advisory firm.
How Digital Twins Are Used in Manufacturing
Digital twins can only drive operational improvement when they can access IoT technologies including sensor systems, high-speed networks, data analytics, and cloud-based computing. Forward-thinking manufacturers use digital twins to add value across all stages of a project’s lifecycle.
Manufacturing applications of digital twins include:
- Product design. Digital twins can be essentially virtual prototypes during the design phase and be adjusted to test different models, manufacturing processes, system interactions, and customer experience.
- Production. The production line can be evaluated with respect to its footprint, workflow, and efficiency. For example, “in a typical production plant, our clients see time spent on changeovers reduced by up to 21%,” says Andrew Wright, a partner in Deloitte’s consulting practice.
- Operations. Digital twins can test different key performance indicators and business models to optimize efficiency. For example, Chevron expects to save millions of dollars in maintenance costs in their oil fields and refineries by 2024 by using digital twin technology.
- Predictive maintenance. Digital twins can detect real-time performance variances that indicate when equipment will likely fail. “Digital twin technologies and advanced analytics can optimize machine throughput and detect quality defects in production by enabling the exponential scale-up of new algorithms across manufacturing facilities,” says Enno De Boer, leader of McKinsey’s global manufacturing practice.
- Supply chain. Supply chains and logistics/distribution use digital twins to study key performance parameters, such as packaging performance and route efficiency. “A digital twin of a road network carries information about the traffic situation, road layout, and construction,” states DHL. “With that knowledge, logistics companies can design the distribution routes and inventory storage locations.”
- Space optimization. Manufacturers and distributors utilize digital twins to test footprint dimensions and layouts to maximize operational performance. This application can also be used for workspaces, where space allocation plays a vital role, and for simulating various emergency scenarios to identify the best evacuation routes.
- Cybersecurity. The U.S. Department of Energy and GE research are creating a “digital ghost” that gathers the critical data generated by a company’s network of digital twins so that it fully understands what is “normal” in the their digital interactions. When the digital ghost spots an aberration, it flags the potential intrusion for human operators. “The technology will also apply algorithms that allow power generation systems to quickly mitigate the effects of an attack by reverting to operating data from the digital model in the event of an attack,” states the Department of Energy.
Moving Forward
Overall, digital twins have many applications across the life cycle of a product and work to continually improve the efficiency of a manufacturing plant, supply chain, or even an ecosystem. If a parameter can be measured with a sensor, its data can be gathered in real time and adjusted for optimum performance. In the future, almost every manufactured product will have a digital twin.
“When combined with analytics, the concept of the digital twin delivers insights that can unlock hidden value,” says Rohit Gupta, vice president of products and resources for Cognizant. “It can provide engineers with information on potential operational failures of IoT-connected products, for instance, and thus help prevent unplanned downtime and improve product performance. The digital twin concept can also help solve challenges across the product value chain, such as lack of coordination and visibility of supply chain processes, limited cross-functional collaboration, and an inability to make data-driven decisions.”
- Category:
- Industry
- Digital
- Equipment
- Manufacturing
Some opinions expressed in this article may be those of a contributing author and not necessarily Gray.