Cooking up Change in U.S. Breweries
Processors can help ensure the safety and health of their employees—and the product itself—through efficiency and quality control. Necessity being the mother of invention, as the old axiom goes, certainly the COVID-19 pandemic has brought out-of-box thinking toward safety to the forefront across the industry.
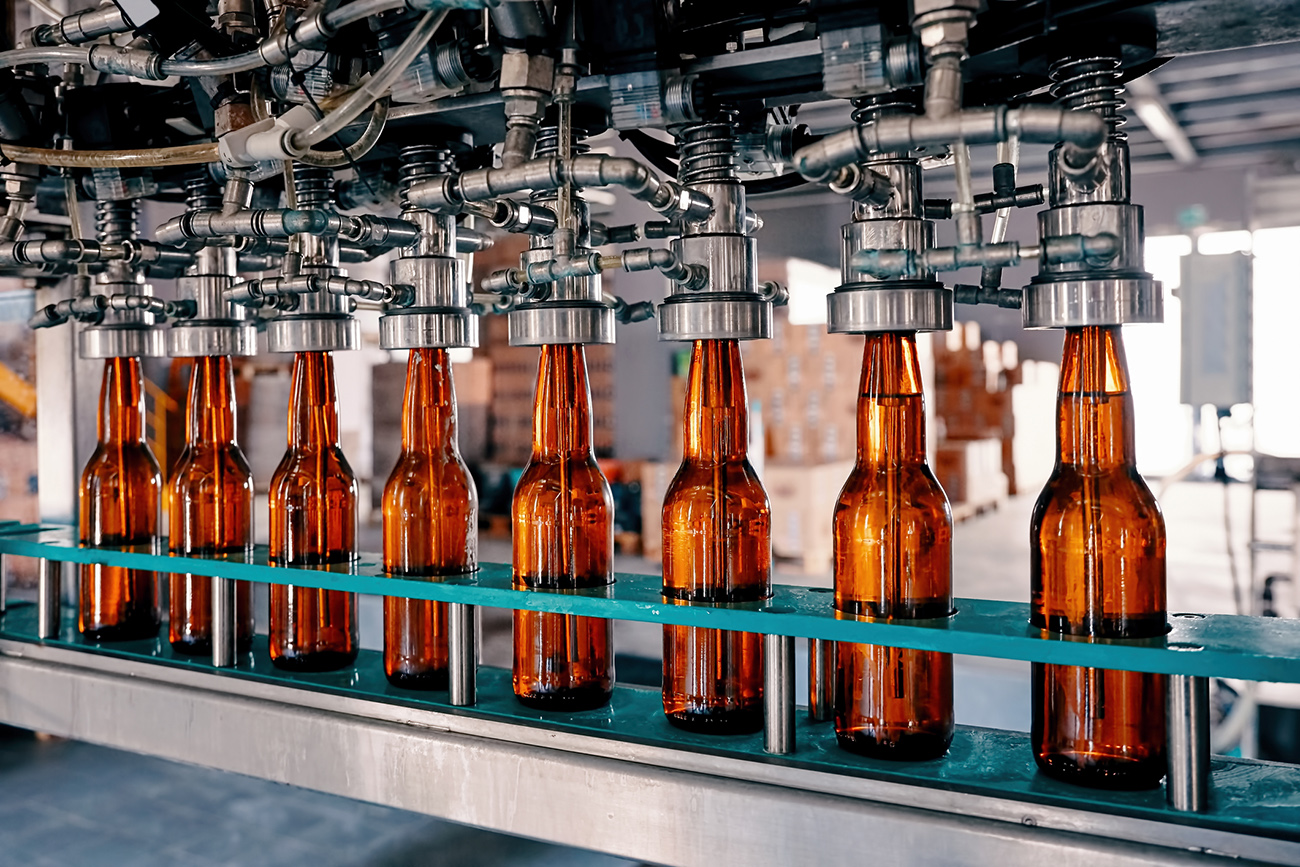
Many in the Food & Beverage industry are looking at some innovations that are already in play—and working to adapt them to their own company philosophies. However, some innovations were coming fast and furiously before the pandemic, and one doesn’t have to look far to see the wisdom behind some of them.
One source for inspiration might begin in the craft brewing world.
One example of such innovation is that of Yee-Haw Brewing Co., a small (but growing) craft brewery located in Johnson City, TN. The company’s water tube boiler “does a lot more than just heat water.” Yee-Haw says its boiler also brings efficiency to its operations and helps with accurate, precision quality-control. The equipment meets many of the versatile demands required in the company’s manufacturing process and is a microcosm of what could help shape the future of F&B processing philosophy.
Yee-Haw uses the Miura LX 200 SG gas-fired water tube industrial steam boiler, which has played an integral role in the company’s manufacturing process since 2015. Producing approximately 18,000 barrels of beer a year in a small 4,000 s.f. facility, Yee-Haw recognized the need for “highly efficient equipment that could fit in a small footprint,” the brewer told ProFood World in April.
This need led the company to install an unconventional choice: The Miura LX 200 water tube boiler has efficiency and design attributes that made it more desirable than a conventional fire tube model. It is smaller, for one thing, at roughly half the size of a fire tube boiler. This is obviously important when space is a factor. But, its compact design translates into more fuel savings—and less energy loss in the long run.
Yee-Haw and Miura estimate that the brewery uses only about 10% of the water volume that’s typically used in traditional fire tube boilers. This can be attributed in part to the reduction in water usage from the boiler’s floating header design. According to ProFood World, “Miura’s floating headers confine the water to the small water tubes. The heat source is distributed throughout the boiler and surrounds the tubes, requiring much less water than a fire tube boiler.”
Better Brews, Greener Breweries
Another (albeit larger) such brewer, located in in Green Bay, WI, is Badger State Brewing Company. With a tap room, beer garden, and 10,000 s.f. of brewing space, the company has a 30-barrel brewing system. In a recent effort to reduce their footprint and the goal of a greener brewery, they added a Miura LX-100SG steam boiler to build out processing capabilities, while reducing fuel consumption and lowering emissions.
As with the Mirua LX 200 SG, steam is what starts the brewing process. In January, company representatives told 2020 Food Engineering, “[with] the Miura LX boiler, shutdown is basically two valves and a button. It’s that simple, and almost anybody can shut it down or start it up. Customers really appreciate that, especially those in the brewery industry who aren’t typically trained as boiler operators.”
With its compact design, the boiler still can provide full steam in five minutes (from a cold start; this is known as “on demand steam”). This compares to other boilers, which often require hours to reach full steam. Co-owner Andy Fabry told Food Engineering: “Now, we can turn the boiler off at the end of the day and know that when we arrive the next morning, we’ll have the steam we need in minutes. Plus we’ll burn less fuel; have fewer emissions; use less water; and conserve natural resources.”
Other beverage brewers are working towards “carbon-neutrality” distilleries. In fact, Gray recently announced that it has partnered with Diageo on a new bourbon distillery and dried distillers grain facility that features an automated distillery process including a granary, fermentation, distillation, and barrel-filling in Lebanon, KY. Taking its sustainability objectives to an even higher level of commitment, no fossil fuels will be consumed for the bourbon production.
The facility will distill Bulleit whiskey and is expected to be one of the largest carbon-neutral distilleries in North America when it begins production in the first half of 2021. It is also a first for Diageo and reinforces the company’s global commitment to reducing its carbon emissions and addressing climate change. The site will be powered by 100% renewable electricity, with a capacity to produce up to 10 million proof gallons per year.
Trickling Up?
This trend toward conserving energy and maximizing efficiency is not lost on the larger players in the brewing business. In fact, in November 2019, Molson Coors Beverage Company announced a new revitalization plan intended to achieve consistent top-line growth by improving efficiency. The company has vowed to “put a greater focus on bringing new beverages to market faster and with more precision.”
This plan includes expanding on an already existing model that reduces the time it takes to bring innovations to market—from 18 months to as little as four months in the U.S. Molson Coors also plans to expand a “test and learn” approach that evaluates market potential for products and then quickly scales up. Part of the company’s new mission includes helping to “build out innovation systems.”
One can infer that even the larger players in the brewery game are committing to conserve resources by burning less fuel and having a smaller footprint overall. Perhaps the small breweries can be credited with having the bigger ideas.
- Category:
- Industry
- Construction
- Food & Beverage
Some opinions expressed in this article may be those of a contributing author and not necessarily Gray.
Related News & Insights
Food & Beverage
Gray Project Receives Manufacturing Innovation Award
Corporate News, Industry
December 04, 2024Advanced Technology, Automation & Controls
Four Use Cases for AI's Growing Role in Manufacturing
Industry
November 25, 2024Manufacturing, Construction
The Evolving Role of Electric Vehicles in Sustainable Construction & Design
Industry
October 18, 2024