Closing the Manufacturing Gap, Part 2
Manufacturers face increasing competition for “customers” of a different sort – people who want to work for them and have needed capabilities for developing key skills and attitudes. We recently discussed several manufacturing gaps that need to be closed in regards to workforce development.
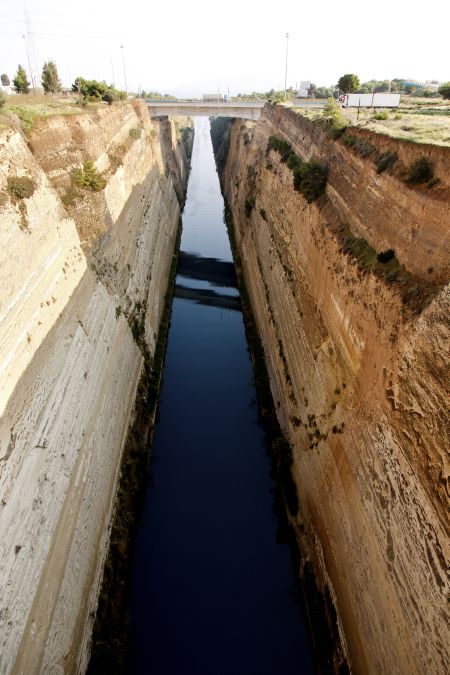
Manufacturers face increasing competition for “customers” of a different sort – people who want to work for them and have needed capabilities for developing key skills and attitudes. We recently discussed several manufacturing gaps that need to be closed in regards to workforce development. Still, are you prepared to meet the growing challenge of not only attracting talent, but also developing and retaining the high-caliber people you need and who will make your company successful in the future? Let’s hope so because others have a head start.
Central States Manufacturing in Lowell, AR, for example, created a Leadership Job Rotation Program (LJRP) to help fuel the company’s growth.
“We created this program to attract, develop and retain the people we will need for the future,” said Ladena Lambert, director of talent acquisition.
LJRP participants are high-potential employee owners who serve in various development roles and receive regular management coaching to prepare them for advancement and a broader scope of responsibility. The employee-owned manufacturer of metal building components for the light gauge, commercial, architectural and residential markets has doubled in size every five to seven years on average since it was founded 25 years ago. During the past year, its employee ranks rose from 407 to 512.
Lambert suggested that manufacturers keep an open mind when they’re scouting for new hires and leadership candidates. “We don’t look as much at the technical side of the job requirements as we focus on whether they are a match with our company and culture,” Lambert said. “That means driven, results-focused, humble and an employee ownership mentality. Then we look at experience, a willingness to relocate if needed and possible roles where they can fit. If they lack some technical skill, we can always train them.”
In this way, the company recruits internally and externally as it attracts and develops the next generation of general managers. “We’ve hired 11 LJRP participants this year and will have 21 by the end of the year,” Lambert added.
Keeping the company’s successful culture and values consistent throughout all its facilities is essential. Promoting within the company supports this goal. Lambert pointed out that current employees often prove to be the best candidates for new positions or for seeking recommendations of others they believe will perform well. Job postings within the company, on numerous job boards and on LinkedIn as well as career open houses help to spread the word about job opportunities.
Lambert suggested that manufacturers seeking a better way to recruit employees shouldn’t be overly focused on teachable technical skills. “Look at what is needed to be successful in your culture,” she counseled. “Once you know they are a culture fit, consider what traits or competencies are required for them to be successful in the job.”
“For instance,” she went on to say, “maybe the job requires creativity or strong planning and organization. Through behavioral interviewing, strategic reference checks and professional assessments and tests, you can learn where there are any gaps.” She described key employee selection factors as “how do – culture fit, can do – skill sets and will do – attitude. We share what our culture is like, and let them know we value their ideas and their ownership,” continued Lambert.
Additional Initiatives
In an initiative aimed at closing the skills gap in manufacturing, Advanced Clean Air Technologies Global (ACAT Global) in Charlevoix, MI recently joined a partnership with other businesses, veterans groups and area educators to offer training in CNC, CAD, CAM and other advanced manufacturing processes. “We need to create a new image of 21st century manufacturing and encourage more people to consider advanced manufacturing, CNC and CAD/CAM engineering as a career,” said Joseph A. Moch, president and CEO of ACAT Global and Oliver Racing Parts.
“Manufacturing jobs are not the repetitive assembly jobs of the past,” Mark Lagerway, the dean of business and technology at Baker College of Cadillac. “From CNC operators to engineers, today’s manufacturing jobs require technical communication and problem-solving skills, and industry and education must work together to prepare both our current and future workforce.”
Coming up September 23-25 in Chicago, the third annual tuXperience session, hosted by U-SME, will focus on successful, integrated manufacturing training programs:
Speakers will discuss how companies align training programs to handle workforce issues and provide bottom-line gains. “The tuXperience is all about how best to build practical knowledge and employee skills through successful, fully-integrated training initiatives calibrated to real business needs,” according to Jeannine Kunz, director of training and development at the Society of Manufacturing Engineers (SME). “This conference brings together manufacturing’s best, brightest and most forward-thinking, those with their hands on the pulse of this industry’s bright future.”
Lea Tonkin has extensive experience as an editor and writer about manufacturing and business. She was the editor in chief of a national manufacturing trade association magazine and the group’s online newsletter, previously serving as the business editor for a chain of daily newspapers in the Chicago area and as an editor for plant engineering and purchasing management periodicals.
- Category:
- Industry
- Manufacturing
Some opinions expressed in this article may be those of a contributing author and not necessarily Gray.