Can IT Systems Actually Hurt Supply Chain Performance?
A survey conducted by PwC and the Manufacturers Alliance for Productivity and Innovation (MAPI) found that companies with better Enterprise Resource Planning (ERP) and supply chain visibility (SCV) systems were more profitable than those without them. Average annual margins grew at a rate of 2 percent in companies that had ERP systems that were effective at enabling agility, responsiveness and operating flexibility. Yet, those with ineffective systems saw margins shrink by 3.5 percent. ERP does have well-known limitations, however, so many companies are adding SCV systems. For companies that already had effective ERP systems, those beefed up with SCV saw margins 0.4 percent higher than with ERP alone. In addition, those that said they had effective SCV systems had 30 percent higher inventory turns than those that did not.
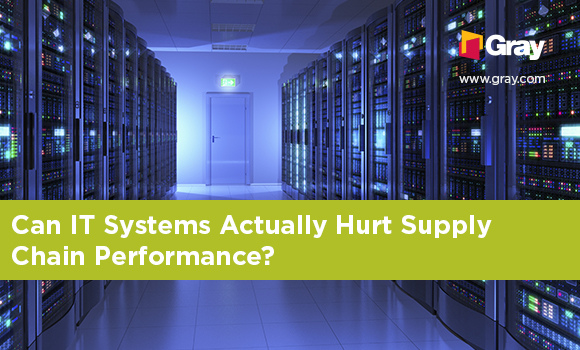
SIOP Performance Disappointment
But what about the day-to-day matter of sales inventory and operations planning (SIOP) performance? Whatever technology they used, more than 40 percent of respondents rated SIOP performance as not good enough. Respondents blamed the problems on poor discipline in operating processes and practices, product complexity, SKU proliferation, poor data quality and poor forecasts. Companies are struggling with uneven incoming materials and variability in demand. The current condition of things on the move is constantly changing. There are myriad ways to fail.
SIOP performance will continue to disappoint if management limits its view to technology or pointing at what they think people are doing wrong. Executives and managers could really benefit from a dose of reality. When managers from all functions and levels go see the production planning offices, the plant floor, shipping and receiving docks, warehouses, supply management offices, and customers and suppliers, they can learn a lot from the people there. Not about their lack of discipline, but what holds them back from doing a good job. Executives can uncover thousands of obstacles and opportunities for improvement. But to try to start fixing everything at once would be a big mistake.
Value Stream Mapping – A Better Way Forward
They need to stand back and take in the whole picture. To do this, many lean experts would advise that top management, including all functional areas, start with high level Value Stream Mapping (VSM). Organizations that begin to use this thinking technology often uncover a better way forward.
When they map the flow of goods and materials in the extended value stream, they will also see the flow of information that they want their ERP and SCV systems to facilitate. It’s more than likely that rationalizing the physical flow will dramatically change the information flow, so tinkering with costly IT systems before doing VSM wastes resources.
With VSM, management can bring the reality check from their visits to their facilities together with their new ideal system of goods and information. With people from all functions in the same room, they’ll find opportunities to streamline the organization and improve performance. The result—not the goal— will be less inventory, higher inventory turns, growing margins and better SIOP performance.
Karen Wilhelm has worked in the manufacturing industry for 25 years, and blogs at Lean Reflections, which has been named as one of the top ten lean blogs on the web.
- Category:
- Industry
- Manufacturing
Some opinions expressed in this article may be those of a contributing author and not necessarily Gray.