Battery Industry Expected to Reach $174 Billion by 2026
According to Mordo Intelligence, the North American battery market was valued at about $22 billion in 2020 and is projected to rise at a compound annual growth rate (CAGR) of 10.5% to about $53 billion by 2027. The trend for the global battery market is similar, jumping from about $105 billion in 2021 to $174 billion by 2026, at a very similar CAGR of 10.3%.
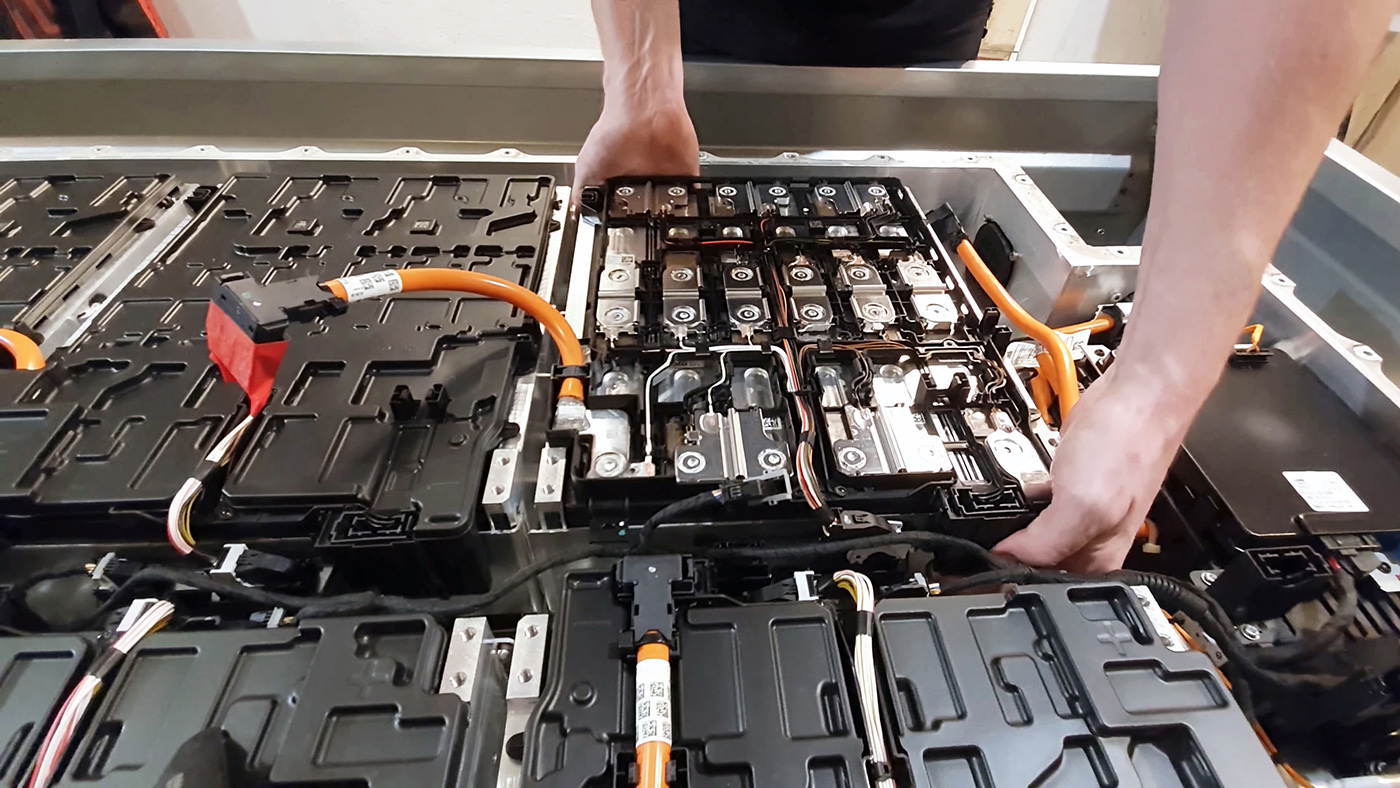
The surge in the battery market is driven largely by sales of electric vehicles (EV) and their lithium-ion battery needs. The automotive industry is the most robust segment in the global lithium-ion battery market. Electric vehicles accounted for almost 9% of new cars sold worldwide in 2021. The range of different vehicle types include EVs, hybrid electric vehicles (HEVs), and plug-in hybrid electric vehicles.
Major electric vehicle companies are competing to develop new and better batteries. For example, Ultium Cells, a joint venture between General Motors and LG Energy Solution in Spring Hill, Tennessee, will invest $2.3 billion to establish a new lithium-ion battery manufacturing plant, creating 1,300 new jobs.
Other key drivers for growth are increased sales of consumer electronics, strong federal support and funding for battery R&D, and the need to make batteries from less-expensive materials that can be sourced in the U.S. Raw materials account for roughly 70% of the total cost of battery cells, much of which come from foreign countries. The COVID-19 pandemic quickly exposed U.S. over-dependency on countries (especially China) for critical battery materials.
Jump-Starting the EV Market
One reason for the enthusiastic support of the battery industry is the recent legislation by the Biden administration. The U.S. Department of Energy (DOE) plans to provide $2.91 billion to boost production of the advanced batteries, including electric vehicles and energy storage. Other goals are developing new materials, battery cells and packs, and improved recycling facilities. DOE states that “the funding . . . will ensure that the United States can produce batteries, as well as the materials that go into them, to increase economic competitiveness, energy independence, and national security.” This is especially relevant now with the Russia-Ukraine conflict, which threatens material sources from that region that are key for battery production (nickel, aluminum) and semiconductor manufacturing (about half of the neon used in global semiconductor manufacturing comes from Ukraine).
With the global lithium-ion battery market expected to grow rapidly over the next decade, DOE has also prioritized sustainable domestic sourcing of the critical materials used to make lithium-ion batteries—such as lithium, cobalt, nickel, and graphite—as well as newer materials/alloys that will accelerate battery production in the U.S. and shorten supply chains.
The Biden administration also indicates it will require states to submit proposals for installing electric vehicle chargers along their highways, part of its $5-billion plan to upgrade the infrastructure and create more charging stations for battery-powered cars. All state proposals must be received by August.
At the Forefront of Innovation
R&D teams are experimenting with battery designs and chemistries to create higher-capacity, longer-lasting batteries from less expensive materials that are easier to source domestically, such as iron, silica, graphite, and nickel.
Thirteen new battery plants have recently been announced and are expected to be operational within the next five years (eight of these are joint ventures between automakers and battery manufacturers). For example, Ultium Cells, a joint venture between LG Energy Solution and General Motors, will spend $2.6 billion to build a battery cell manufacturing plant in Lansing, Michigan, which will utilize its own proprietary technologies and chemistries.
Other battery advances include:
- Solid-state batteries—SSBs are lighter weight, store more energy, and have no liquid electrolyte, making them less flammable; however, they are expensive to manufacture at scale
- Nickel metal hydride batteries—these rechargeable batteries have high energy density, superior capacity, longer run times between charges, and a wider range of operating temperature (-50°C to +85°C)
- Stanford University has invented a battery with an aluminum negatively charged cathode and a graphite anode, making it safer to operate, with the potential for faster charging and improved energy density
- Lithium-silicon batteries—this battery uses silicon, a plentiful and inexpensive material, for the anode instead of graphite, boosting battery performance by up to 40% compared to standard lithium-ion batteries
Lithium-ion batteries are not just for consumer products and cars—larger-scale versions are used on the energy grid to store energy. Grid-scale batteries are expensive, however, and degrade after several years of operation. An alternative is flow batteries , which are made from iron, salt, and water—abundant, inexpensive, and completely nontoxic materials. Flow batteries are being used more in the grid-storage market—a flow battery the size of a shipping container has the capacity to store up to 500 kilowatt-hours.
As more R&D is spent by government research agencies, universities, and the battery and automotive sectors, next-generation batteries will be developed with advanced microstructures, chemistries, and higher energy storage capacities to meet evolving consumer needs, especially the EV market.
- Category:
- Industry
- Construction
- Digital
- Manufacturing
Some opinions expressed in this article may be those of a contributing author and not necessarily Gray.