Why Supply Chain Partners Need to Embrace Industrial Energy Efficiency
Large brand-owning retailers and manufacturers are targets of scrutiny for environmental impact, and they are making strides in both reducing greenhouse gas emissions and increasing energy efficiency. The University of Minnesota Institute on the Environment’s NorthStar Initiative for Sustainable Enterprise (NiSE) and the Environmental Defense Fund (EDF) released a report in August called Supply Chain Energy Efficiency: Engaging Small & Medium Entities in Global Production Systems that provides valuable information on energy efficiency in regards to the supply chain.
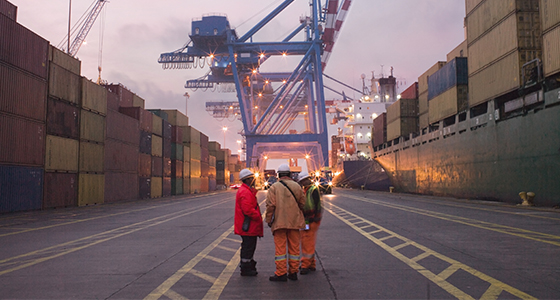
What stands in the way of a supply chain approach to reducing manufacturing’s environmental impact?
Large brand-owning retailers and manufacturers are targets of scrutiny for environmental impact, and they are making strides in both reducing greenhouse gas emissions and increasing energy efficiency. The University of Minnesota Institute on the Environment’s NorthStar Initiative for Sustainable Enterprise (NiSE) and the Environmental Defense Fund (EDF) released a report in August called Supply Chain Energy Efficiency: Engaging Small & Medium Entities in Global Production Systems that provides valuable information on energy efficiency in regards to the supply chain.
According to this report, retailers and manufacturers only produce an average of 14% of their product’s cradle-to-gate emissions: the other 86% comes from their supply chains, and a relative few of those suppliers are investing in emission reductions. In 2011, as 69% of their customers were working on producing lower emissions, only 27% of suppliers were.
Why aren’t suppliers getting on board? There are two interrelated barriers. One is the belief that sustainability improvements are not worth the cost of investment. The other is the widespread belief that environmental management metrics and standards do not exist, making meaningful evaluation impossible.
Supply chains include a constellation of small and medium-sized manufacturers (SMEs), where management often believes the short-run cost of an improvement outweighs longer term savings in energy. They shy away from having to incur the associated costs of measuring, recording, analyzing, and reporting the data that underpins a sustainability program. They are not even sure what the right metrics would be, so it’s that much harder to make an investment decision.
To encourage those smaller companies that say they can’t afford to make sustainability improvements, Germany, Japan, the UK, France, and China provide low interest loans or loan guarantees. In the U.S., the Department of Energy’s Industrial Assessment Center (IAC) program provides no-cost energy audits to SMEs. Using the information from the audit, IAC efficiency experts help them decide what improvements to make. Nearly 40,000 recommendations were made to 9,000 companies throughout 2011, but the record for implementation is not impressive. Only half of those projects were ever carried out, and they, of course, were those requiring the least money and effort. How well do these programs from governments around the world work? No one knows, because data about results is not required or collected.
Some say that industry collaborations should do more to attack the supply chain problem. Researchers and industry advisors have recommended that OEMs or powerful retail companies pilot Tier One and Tier Two supply chain energy improvement programs. They have urged industries to standardize data about energy use in supply chains. They have also recommended that supply chain collaborations develop benchmarking, analysis, and best practice sharing.
Have OEMs really been unable to improve energy efficiency at supplier companies? Why is industry benchmarking is not underway? Is it true that environmental metrics have no agreed-upon standards? It’s baffling to me that such assertions are being made.
Industry benchmarking is alive and well, facilitated by organizations like the American Productivity & Quality Center (APQC). Many industry associations also have structures for member companies to report and share best practices.
Leading OEMs’ procurement policies demand environmental performance measures and improvement from suppliers. Toyota’s green purchasing guidelines, for example, require suppliers to have an energy management system based on the environmental standard ISO 14000, and they specify the metrics and reporting expected. To remain a Toyota supplier, a company has to demonstrate continued improvement in environmental performance. Retailers like Walmart also exert their leverage on consumer product supply chains.
It’s true that many SMEs have not yet been touched by industry mandates and aren’t voluntarily addressing environmental concerns. At the same time, almost all are part of some raw material-to-retail product lifecycle so environmental improvement demands from customers will reach them at some point. SMEs that get started now with sustainability programs, based on common standards, will gain an advantage over their competitors in securing a preferential place in supply networks.
Whether it’s to reduce energy costs, comply with increasingly stringent government regulations, keep customers, or make the environment better, ready-to-use standards for environmental performance, opportunities for benchmarking, and help in financing improvements are already in place.
If we have done all this groundwork already, how do we educate researchers and manufacturing executives to keep them from wasting time and resources reinventing the wheel?
Karen Wilhelm has worked in the manufacturing industry for 25 years, and blogs at Lean Reflections, which has been named as one of the top ten lean blogs on the web.
- Category:
- Industry
- Manufacturing
Some opinions expressed in this article may be those of a contributing author and not necessarily Gray.
Related News & Insights
Manufacturing, Construction
The Evolving Role of Electric Vehicles in Sustainable Construction & Design
Industry
October 18, 2024Manufacturing
Sustainable Manufacturing Creates a Culture of Caring
Industry
Distribution, Advanced Automation
Shining a Light on the Lack of Fully Automated "Dark Factories"
Industry
September 27, 2024