Unlocking the Mysteries of Takt
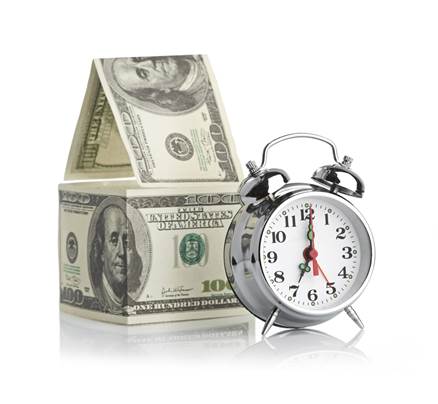
Countless times an effective lean consultant will go into the workplace and ask the dagger question: What is your takt? Takt simply refers to the rate of customer demand. It comes from the German word for meter or rhythm like a metronome set to play 60 beats per minute. Every second you play a note or set of notes worth one beat. In many disconnected processes, you can walk up to someone in any process and ask for their takt, and they will hand you a schedule. They know they have to produce a number of items each day, but they don’t know how long it takes them to complete an individual item. They have to really think about it, but it is largely irrelevant as there is enough inventory to hide any delays in production. Also, if it is a non-routine professional job, they may have no idea. Every task takes a different amount of unpredictable time so they put in a full day of work.
Ideally, lean consultants would like the answer to be: today we need to make 1 of these every takt, for example, 90 seconds. Therefore, as you approach 90 seconds you know if you are ahead, on time, or behind.
Toyota builds to takt, but many say it is easy for them. The takt is set by the speed of the final assembly line which sets the pace for all upstream processes. Since they make a lot of combinations of different options and as many as seven different vehicles on the same line, it is clearly not a simple process. But, they do a lot of things to smooth the schedule, so it is consistent throughout the day. Production control collaborates with sales to level the schedule, meaning you will not see 3 high content vehicles in a row. Other automakers that could, in theory, be able to do this, do not do it very well, so it certainly is not automatic on an assembly line. It requires intentional and thoughtful action.
Specialty food seller Zingerman’s Mail Order in Ann Arbor, Michigan, understands this subject well as it was in a position of getting different numbers and mixes of orders of specialty food items every day and taking more orders throughout the day. At first they believed it was impossible to create boxes of goods according to takt. Over several years of lean transformation, they went from batch building to one-piece flow—one customer order at a time—they got their process under control and achieved takt. The takt is set every day based on estimates of orders that will come in on a specific day. From there, orders that come in during the day are slotted in. In the slower periods, which are most of the year, they may only work a few hours of the day and need to fill a box every 3 minutes. But, in the peak holiday period, they hire many temporary workers and fill a box every 7 to 9 seconds.
The pacemaker is a computer printer that prints a batch of 3 orders to takt, so with a 9 second takt every 27 seconds, 3 orders are printed. This starts the process of pickers selecting items from specific locations within their zone—in fixed positions with unique addresses. These then flow through to inspection, placement in special colorful boxes, then placement in shipping boxes, and even flow by conveyor onto a waiting UPS truck.
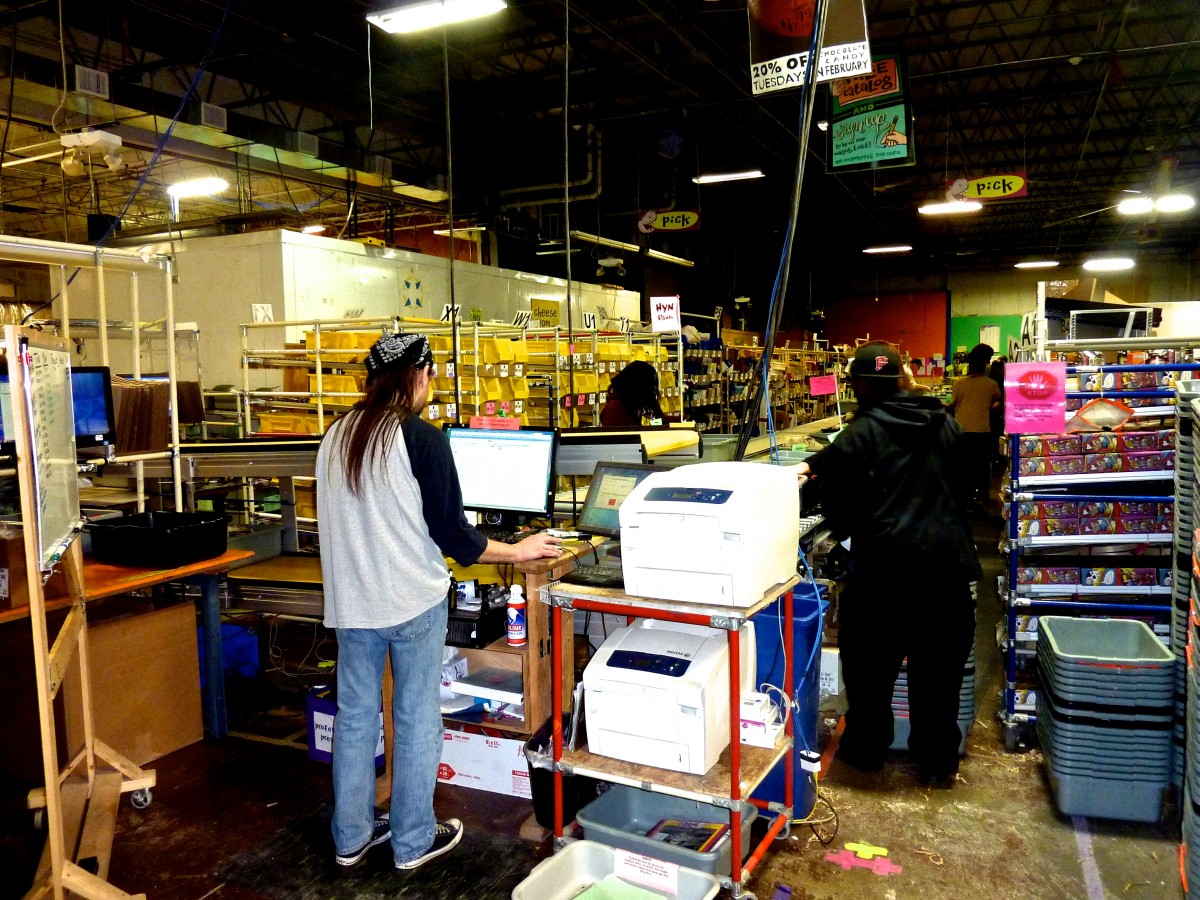
The takt is average, as it is for Toyota, and some tasks such as filling a gift box, take longer than the takt. Still, this model works as long as there are several people building those boxes and averaging to the takt as well. Through standardized work, they are getting more and more consistent and closer to building to takt. And, even material handlers bring product to the line based on takt, such as bread and cheese cut to order.
Another complication with takt is in highly variable knowledge work like software development. Menlo Innovations, also located in Ann Arbor, breaks the complex job of creating software into individual features and estimates the time to
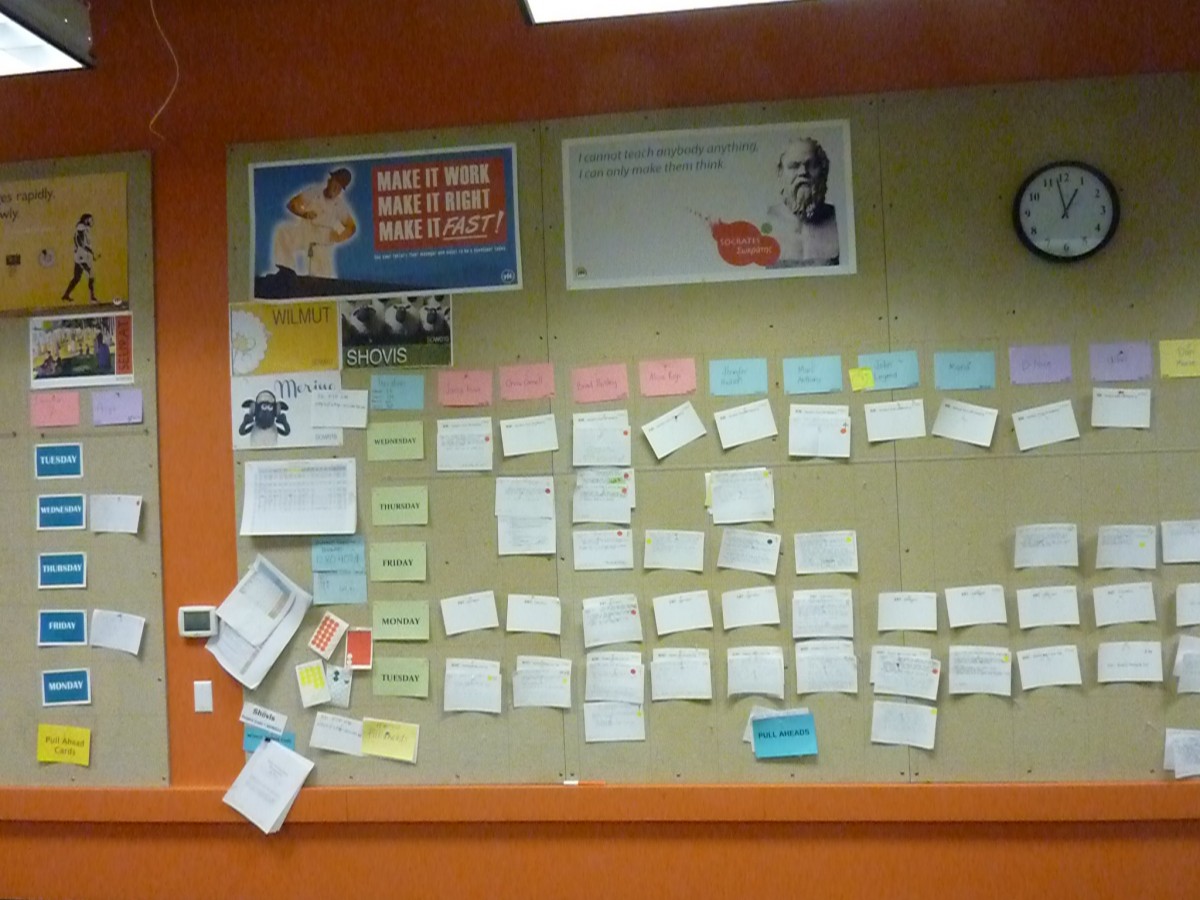
program those features in intervals of 1 hour, 2 hours, 4 hours, 8 hours, or 16 hours. Pairs of programmers are assigned a day of work each day using story cards (index cards) on a wall by picking a card, programming it, and then moving on to their next card. Though the takt is not easily expressed as a feature per hour, they do know each hour if they are ahead or behind and how the work is paced. Another pacing mechanism is customer reviews that happen every week at the same time for a given product. Even though the time intervals between starting and finishing a task are much longer than the 1 minute takt common in Toyota auto plants, they have a sense of time and there is a rhythm to the work.
Think of an orchestra with a conductor where all the instruments are coordinated by takt—the rhythm of the conductor. What is your rhythm? When do you know if you are ahead or behind—every takt, hour, week, month? The shorter the time interval, the better. This means breaking the work into smaller chunks and coming up with times, even if they are estimates. Paced work brings you to a rhythm, a pattern, and almost always will increase productivity and even quality.
Dr. Jeffrey Liker is professor of industrial and operations engineering at the University of Michigan and author of The Toyota Way. He leads Liker Lean Advisors, LLC and his latest book (with Gary Convis) is The Toyota Way to Lean Leadership.
- Category:
- Industry
- Manufacturing
Some opinions expressed in this article may be those of a contributing author and not necessarily Gray.
Related News & Insights
Manufacturing, Construction
The Evolving Role of Electric Vehicles in Sustainable Construction & Design
Industry
October 18, 2024Manufacturing
Sustainable Manufacturing Creates a Culture of Caring
Industry
Distribution, Advanced Automation
Shining a Light on the Lack of Fully Automated "Dark Factories"
Industry
September 27, 2024