Top Trends for Equipment Manufacturing in 2022
Brought on by the COVID-19 pandemic, Industry 4.0 and the Internet of Things (IoT) technologies were embraced by many manufacturers as the best way to stay competitive, deal with disrupted supply chains and fewer workers, and remain connected with customers. Manufacturers learned that these technologies could maximize quality, improve operational performance, and reduce costs.
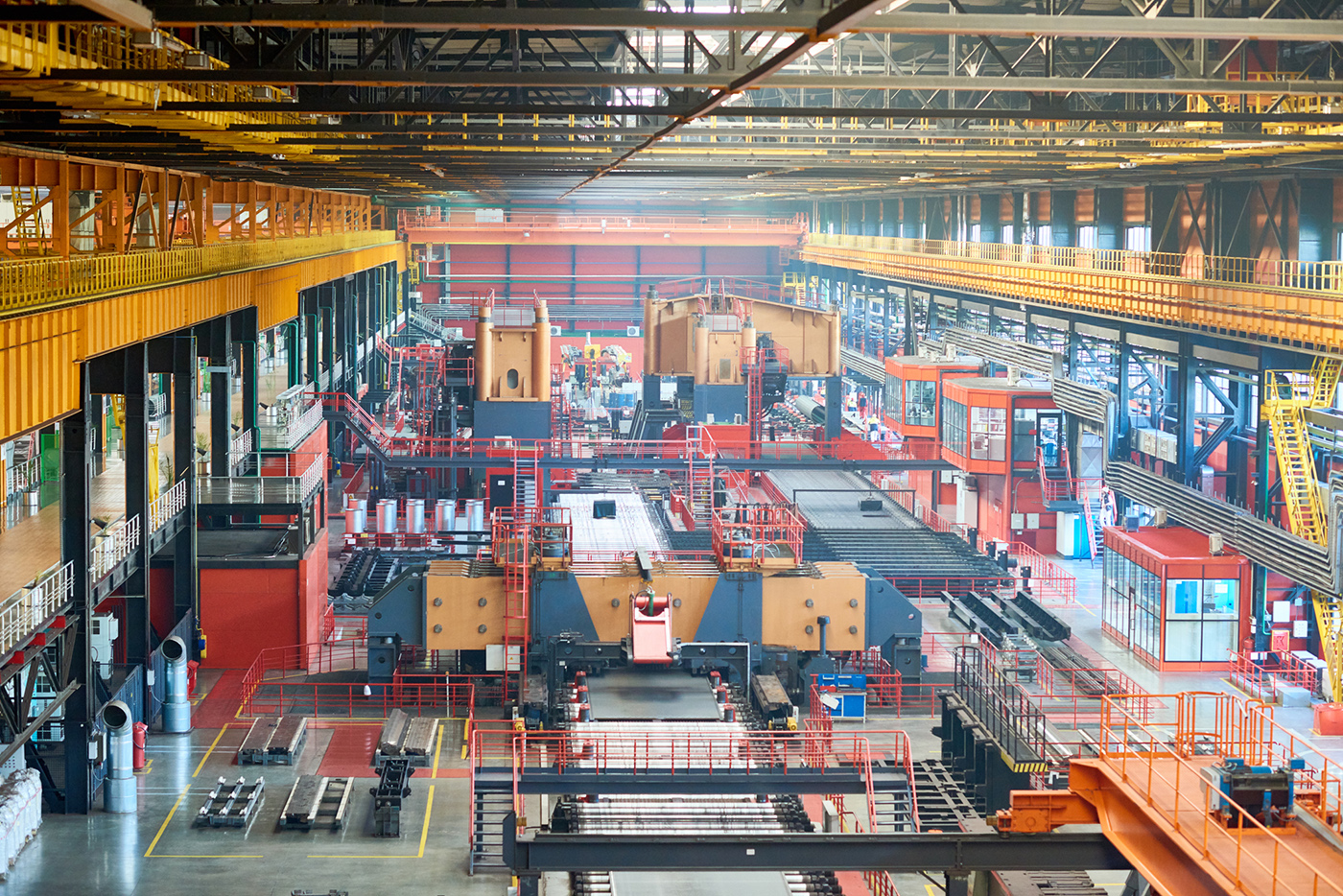
IoT also helped hold together wobbly and impaired supply chains, which impacted equipment manufacturers as well as food processing companies.
“Impacts from the COVID-19 pandemic include raw material shortages, extended lead times, and supply chain issues that were not a problem 18 months ago,” says Jon Nordrum, vice president of Operations for Anderson Dahlen Inc., a Gray company, in Ramsey, Minnesota. “There were also direct impacts to our manufacturing operations, which required significant adjustments to how we managed our team members to keep everyone safe while continuing to keep products moving through welding, machining, and other work centers.”
Robotics, vision systems, digital paperwork systems, and more advanced packaging requirements are all becoming key elements for supply chain management. “Digitizing quality and production paperwork into dedicated software systems helps drive improved knowledge and data to the plant worker, while also improving the focus on quality and productivity,” says Alex Allen, vice president of Pearson’s Candy Company, an American chocolate and confectionery manufacturer in St. Paul, MN. “Automating visual inspection is also becoming easier and more cost-effective.”
IoT enables many new ways to enhance plant and supply chain operations while also maximizing profits. Research group IDC maintains the combined added value from the improvements in operations powered by IoT is worth about $470 billion per year.
Below are eight trends that will make manufacturing more efficient in 2022 and beyond.
1. Safety. IoT can improve safety in the manufacturing environment by monitoring machine performance and identifying problems before they become dangerous. IoT-enabled sensors in personal protective equipment such as vests and hardhats can monitor a worker’s vital signs, movements, and repetitive motions to keep them safe.
2. Digital twins. A digital twin is an exact virtual model of an object, process, or system that is built from hundreds of thousands of data points generated by IoT technologies, using embedded sensors. The virtual, 3D replica or “twin” can then be viewed, monitored, or adjusted in real time to test new ideas or determine the best ways to improve production and efficiency.
3. VR and AR. Digital twin data can be used to create virtual reality (VR) and augmented reality (AR) 3D models. Aspects of the models can be varied to solve manufacturing challenges, evaluate virtual prototypes, reduce costs, and increase productivity. VR and AR can also be used to determine the most efficient use of space, inventory locations, and workflow patterns. They are also effective tools for staff training and demonstrating safety protocols.
4. 3D printing. Additive manufacturing (AM) or 3D printing continues to be applied in new and creative ways in the manufacturing sector. Some companies, such as Caterpillar, design products that can only be made through additive manufacturing. A steady stream of new materials and more sophisticated AM processes give engineers a wider range of design options. 3D printing can also be used to build replacement tools or parts for the manufacturing equipment itself.
5. Predictive maintenance. Sensors embedded in equipment track key performance indicators and alert operators in real time of operational variances that could be signs of an upcoming equipment failure—allowing technicians to fix the issue before it becomes a problem. “Advanced control features and sensors are monitoring more key indicators,” says Joe DeFrancisci, a managing partner with DEMACO, a food equipment manufacturer. “For example, not only can sensors monitor oil levels, they also monitor the percent of water in the oil.” Predictive maintenance extends the lifespan of equipment, reduces maintenance costs, and increases physical safety for workers.
6. Customization. Customization is the process by which a mass-produced product can be tailored to meet the demands of smaller customer groups, without a significant increase in costly manufacturing adjustments. For example, “we are seeing a consistent push toward smaller runs with more variety of flavors, packaging size, and packaging options,” says Allen. “Competitive retailers like to be able to offer unique products, which often results in packaging or size changes.” IoT technologies such as robots and 3D printing improve the feasibility of making low-volume customized products without high costs.
7. Automation. With worker shortages during the COVID-19 pandemic, many manufacturers invested in automation and robotics to maintain production. Robot cells are easy to scale up or down depending on production needs. Cobots Robots can also be programmed to work safely beside human workers and fill in gaps along the production line, where workers are missing. Heavy lifting or risky repetitive tasks can also be assigned to robots, improving worker safety and reducing injuries.
8. 5G. According to The Manufacturing Institute, “5G will usher in faster speeds, greater throughput, and lower latency. The network specifications also promise greater reliability, extended battery life for connected devices, and support for massive device connectivity [IoT].” Application areas for 5G-enabled manufacturers include supply chain, inventory, facility security, warehousing and logistics, inspection, assembling, packaging, and HR training.
Smart Manufacturing Gets Smarter
IoT and data analytics have become an integral part of the manufacturing landscape. Even when COVID-19 subsides, manufacturers will continue to implement and deploy Industry 4.0 and IoT technologies to stabilize their supply chains and be competitive in the global economy. By integrating these digital technologies with each other and cloud-based analytical platforms, manufacturers will be more efficient, productive, and safer than ever before, increasing revenues and winning market share.
- Category:
- GrayWay
- Construction
- Manufacturing
Some opinions expressed in this article may be those of a contributing author and not necessarily Gray.
Related News & Insights
Advanced Technology, Automation & Controls
Four Use Cases for AI's Growing Role in Manufacturing
Industry
November 25, 2024Data Centers
Gray Expands Reach with Dallas Office
Corporate News
November 14, 2024Manufacturing, Construction
The Evolving Role of Electric Vehicles in Sustainable Construction & Design
Industry
October 18, 2024