The Meaning of Ownership in Lean Methodology: A Tire Change Case Study
We recently began working with a new client – a large and productive business unit of a global company that depends on a great deal of mobile heavy equipment to move major tonnage of materials around. The details do not matter, but for this company, the equipment is the key to production, and thus maintenance is the key to production. The president of this business unit is a lean zealot who brought in a major lean consulting firm about a year ago to support a lean transformation. They chose to work on the core operations and leave support functions like maintenance for the next phase. Meanwhile, the director of maintenance did not want to wait. He assigned two highly experienced managers to become internal lean coaches and self-learn through courses, reading, and benchmarking with lean exemplars. The president learned of the good progress they were making and ordered them to hire an outside teacher.
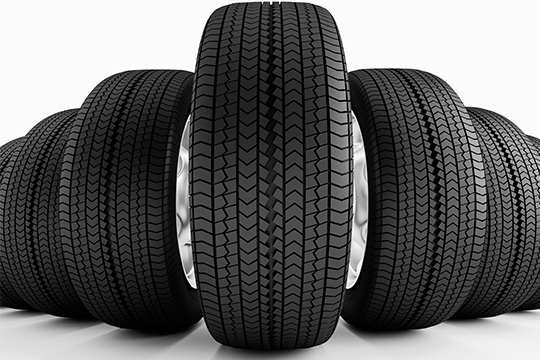
We recently began working with a new client – a large and productive business unit of a global company that depends on a great deal of mobile heavy equipment to move major tonnage of materials around. The details do not matter, but for this company, the equipment is the key to production, and thus maintenance is the key to production. The president of this business unit is a lean zealot who brought in a major lean consulting firm about a year ago to support a lean transformation. They chose to work on the core operations and leave support functions like maintenance for the next phase. Meanwhile, the director of maintenance did not want to wait. He assigned two highly experienced managers to become internal lean coaches and self-learn through courses, reading, and benchmarking with lean exemplars. The president learned of the good progress they were making and ordered them to hire an outside teacher.
The consulting firm already working in operations uses a kaizen event approach consisting of five-day lean events. The maintenance department followed the same approach and ran their first event focusing on tire changes, using a “pit crew” concept. They dedicated a bay in the maintenance building to tires, in which they organized tools through 5S and created kits of replacement parts. Through these and other improvements, in a one month period, they were able to reduce the changeover time from 8 hours to just 3 hours. The team was even able to complete 1 changeover in just a little over 2 hours.
They were ready to declare victory on their improvements, but it was clear to me they had only scratched the surface of what was possible in that area. There was no real standard of work for the tire change. And, a more serious problem was that an owner did not exist who would take responsibility for working out detailed procedures. Someone needed to be able to check to see that these procedures were followed and work toward continuous improvement. In fact, all the lean activities seemed to have a short half-life that quickly decayed—5S was not being maintained, suggestions that were months old were not yet acted on, and there was little evidence of real problem solving. Supervisors were interested, but not seriously engaged in the lean activities. The maintenance workers were less engaged as evidenced by their low energy levels in the daily morning meeting.
The problem of sustainability was simple: someone needed to take ownership over the process. Someone had to check the process, facilitate the use of the tools, and provide improvement in the standards. Herein was the root cause of their sustainability woes. There was little stability of personnel in any area or for any process, which was partly because of a recent crisis. As a result, supervisors had been shuffled, and due to a matter of policy, maintenance workers were already treated as “generalists” who could be assigned to any repair at any time. In other words, there was no stability of ownership of any process or of any particular piece of equipment.
Standard work is one practice that would be unsustainable with this lack of stability. The standard work for routine preventative maintenance, like a tire change or lube job, had been developed by a corporate function and was displayed as a Gantt chart on A3-size paper. One could check the progress of the maintenance relative to the standard times. But, no one in maintenance new exactly where the standard times came from, how a process step was expected to be performed, and whether the times reflected actual conditions. This became obvious in the case of tire changes since they had dramatically reduced the lead time. The Gantt chart, however, was still based on an 8-hour process. Who was supposed to change the chart and develop new standard work for tire changes? Who would be sure the workers were trained to the standard work and continue to follow it? Who would try to improve the tire change to another level and modify the standard work accordingly?
While these answers are still in the process of being determined, the good news is that the maintenance director, key managers, and lean coaches in training felt a strong sense of ownership. In many ways, they benefited from not having immediate access to the external consultants. They had to struggle and learn on their own. Going forward, they need to build on that strong foundation and establish stable processes, such as the quick tire repair bay, as well as create local ownership of those processes. Unfortunately, too many companies view lean methodologies as a toolkit to be deployed, and not a process of developing capable people who are accountable for continuous improvement.
Dr. Jeffrey Liker is professor of industrial and operations engineering at the University of Michigan and author of The Toyota Way. He leads Liker Lean Advisors, LLC and his latest book (with Gary Convis) is The Toyota Way to Lean Leadership.
- Category:
- Opinion
- Manufacturing
Some opinions expressed in this article may be those of a contributing author and not necessarily Gray.
Related News & Insights
Advanced Technology, Automation & Controls
Four Use Cases for AI's Growing Role in Manufacturing
Industry
November 25, 2024Data Centers
Gray Expands Reach with Dallas Office
Corporate News
November 14, 2024Manufacturing, Construction
The Evolving Role of Electric Vehicles in Sustainable Construction & Design
Industry
October 18, 2024