The Hypermodern Facility: The Next Generation of Food Processing
In 2023, what does it mean for a plant to be truly “modernized”? With lightning-fast shifts in technology, consumer preferences, and business priorities, designers of new food and beverage plants must be able to adapt quickly to accommodate changes.
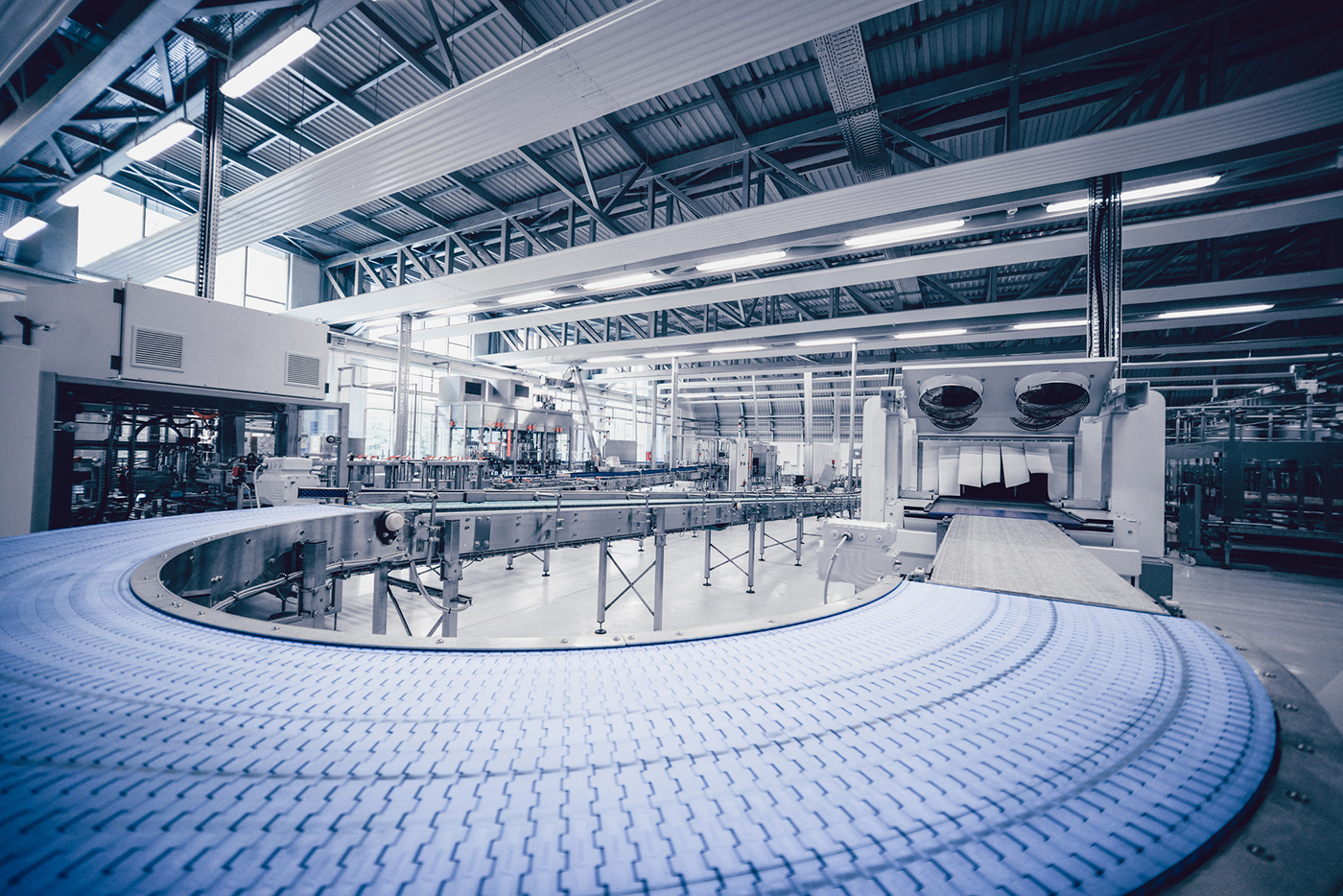
Such an approach demands space and flexibility for growth, process updates, and the integration of new equipment—all of which begins in the planning stages. Design versatility is now a requisite for creating a successful, fully integrated hypermodern facility.
Room to Grow
A recent article in Food Processing magazine outlined how versatility is the best way to design for growth when planning a hypermodern food and beverage facility. A versatile design enables customers to begin operations on one line and respond such that “if their needs change, they can quickly change that line within the facility.” Having the agility to expand a select process requires facility and process designers to leave ample room while still maintaining an efficient layout for current operations.
To achieve this, designers can allocate additional floor space for machinery, conveyors, and other equipment; alternatively, engineers can incorporate utilities that are “not only expandable, but sanitary. In many cases, that means putting them above the ceiling.”
Solutions such as walkable ceilings can keep all utilities outside a sanitary zone. As production equipment and processes evolve over time, equipment can be decommissioned and replaced simply by going through the ceiling to tap into existing infrastructure.
In a ProFood World roundtable panel discussion at PackEXPO 2022 in Chicago, experts from around the food industry answered questions about the challenges that food manufacturers will face in the next few years. Moderator Alan Reed, Executive Director, Chicagoland Food & Beverage Network put the question plainly “What are the changes you believe that we’ll see in manufacturing facilities in the future?”
According to the panel experts, the ability to reconfigure a plant using modular components will play a crucial role. Broadly speaking, “modularity” is the degree to which a system’s components may be separated and recombined to allow for greater flexibility and variety in use. A recent article in Food Manufacturing expounded on the practice.
“As a production method, modularization allows manufacturers to assemble hardware in a plant by combining individual modules into a desired order.” Splitting the line into modules bypasses the traditional, rigid format of production and enables manufacturers to modify their format according to the factory’s ever-changing needs.
Utilizing modularity in a facility gives engineers the flexibility to explore a range of layout options without excessive downtime or cost. This agility can be key to an operation’s success in the current climate of “high-mix, low-volume manufacturing.”
Calculating for Success
The digital transformation of industrial facilities was already trending up before the COVID-19 pandemic hit, but this event highlighted the need for more robust digital integrations and advanced automation in food & beverage manufacturing facilities. As the trend accelerated, so too did the importance of establishing and maintaining operational data streams.
Said Mark Adelmann, Director of Business Development, EN Automation, “Data is the lifeblood of a smart factory. And so, integration of that data, getting the data to where it needs to be, is key. If it’s done correctly, you’ll end up with an agile facility that can adjust to its operational needs and the demands of its customers as well.”
The most successful food & beverage facilities will be smart factories that seamlessly integrate data into their IT and OT systems. Such integration is essential to solve supply chain issues, meet sustainability requirements, and enjoy greater flexibility. “The key to this is making data available at all levels of the organization so they can leverage that information to operate more efficiently,” said Adelmann.
Software Does Hard Labor
One data-optimization solution that has gained traction in food & beverage facilities is the implementation of Computerized Maintenance Management Systems (CMMS). CMMS are software applications that centralize and automate maintenance management tasks.
CMMS software can optimize scheduling and tracking of maintenance work and provide data-driven insights to improve asset management and productivity. Digitized maintenance records empower manufacturers to monitor equipment performance more effectively and reduce operational costs.
A CMMS can help to ensure that maintenance tasks are completed in a timely and efficient manner—reducing downtime, increasing productivity, and lengthening equipment lifespan. Additionally, a CMMS can help organizations comply with regulatory requirements and improve safety by promoting regular maintenance and better record-keeping.
The software in a CMMS functions as a centralized repository for all maintenance-related data. It tracks and records information about maintenance history, equipment specifications, spare parts inventory, and other items. Plant managers can input tasks such as work order requests and preventive maintenance schedules and generate reports on asset performance, work orders, and inventory levels.
Always Evolving
Operating a hypermodern food & beverage manufacturing facility is all about embracing evolution. Agility and adaptability must encompass the physical facility design and layout as well as the digital sphere and its complete systems integration.
- Category:
- Industry
- Food & Beverage
Some opinions expressed in this article may be those of a contributing author and not necessarily Gray.
Related News & Insights
Food & Beverage
Gray Project Receives Manufacturing Innovation Award
Corporate News, Industry
December 04, 2024Advanced Technology, Automation & Controls
Four Use Cases for AI's Growing Role in Manufacturing
Industry
November 25, 2024Food & Beverage
Gray & Morinaga Celebrate New Production Expansion
Projects
October 18, 2024