Responding to Supply Delays, Labor Shortages, and Economic Downturn
As a recent guest on a podcast hosted by Food Engineering’s Wayne Labs, Tyler Cundiff, president, food & beverage group, Gray, Inc. discussed the business challenges of an economic downturn, the rise of vertical farming and controlled environment facilities, and the expanding role of alternative proteins and cultured meats across the industry.
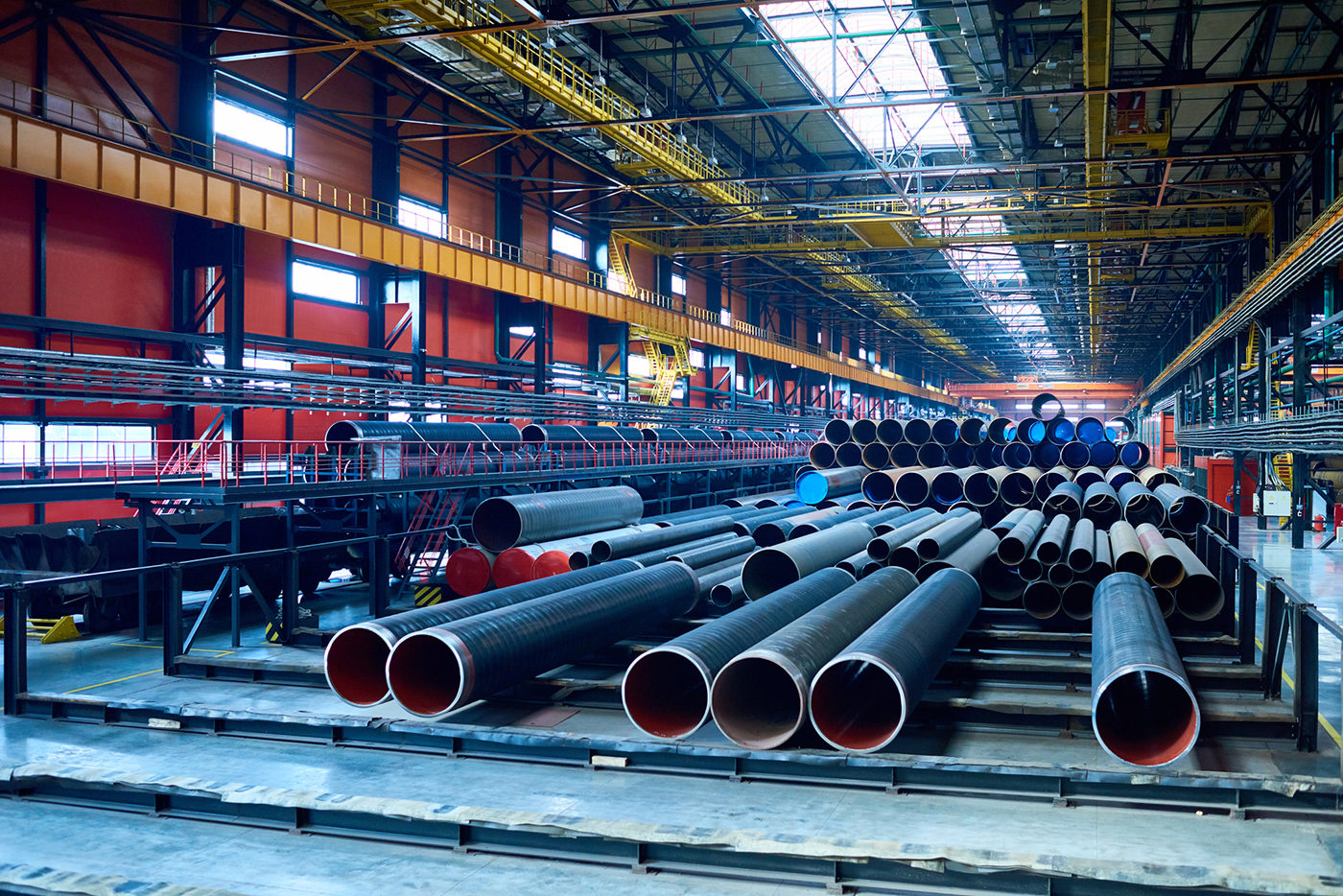
The economic downturn’s causes as well as its symptoms have had high public visibility—a lingering pandemic, sharp inflation vs. stagnating wages, and Russian aggression in Ukraine have resulted in prolonged supply chain delays, labor shortages, and an emerging food crisis. In part one of the podcast, Cundiff discussed the availability of construction materials, the business impact of food supply chain interruptions, and lead times that in some cases extend beyond two years.
Cundiff explained that a volatile economic climate with fluctuating supply, pricing, and logistical bandwidth have made it more difficult to identify trends and accurately forecast market conditions and business needs. For a close-to-home example, Cundiff explained that some steel suppliers won’t price product until it ships, which illustrates how much can change in a matter of weeks. These industry challenges extend to energy prices as well.
In terms of labor markets, firms across the construction industry are experiencing labor and supply chain issues, whether they’re focused on engineering, construction, design-build, or EPC. Cundiff explained that the current market for labor results in firms competing to find talented trade partners and subcontractors.
Despite the market’s volatility, food & beverage customers are moving forward with greenfield projects of significant size despite their awareness of the escalated costs and lead times. Cundiff says that today, most customers already have a thorough understanding of their facility needs and have already decided on a brownfield vs. a greenfield facility when projects reach the RFP phase.
It’s this critical juncture where Cundiff believes that an expert partner can provide essential guidance and insight. When it comes to investing in sustainable facility elements, for example, customers need to know what will make the biggest difference in their sustainability footprint. Gray recently completed a project for the first carbon-neutral distillery in the U.S. By far the biggest piece of achieving this goal was upgrading to electric boilers. To make the best possible investment decision, the customer has to understand CapEx vs. OpEx and total cost of ownership.
These sustainability decisions usually do come down to cost, says Cundiff. Increasing carbon taxes or sustainable/upcycling incentives can help food processors move in a more sustainable direction. Many regulations also now reach LEED status, so it’s increasingly rare that customers elect to go through the certification process.
To learn more, listen to the full podcast from Food Engineering or explore how Gray serves customers in Food & Beverage.
- Category:
- Industry
- Food & Beverage
Some opinions expressed in this article may be those of a contributing author and not necessarily Gray.
Related News & Insights
Food & Beverage
Gray Project Receives Manufacturing Innovation Award
Corporate News, Industry
December 04, 2024Advanced Technology, Automation & Controls
Four Use Cases for AI's Growing Role in Manufacturing
Industry
November 25, 2024Food & Beverage
Gray & Morinaga Celebrate New Production Expansion
Projects
October 18, 2024