Replacing Robots with People at Toyota: Simple, Slim & Flexible
Bloomberg news recently ran a story with the provocative title “Gods’ Make Comeback at Toyota as Humans Steal Jobs From Robots.” The news journalists spent time in Toyota’s plant next to Toyota City headquarters that I wrote about last summer related to automated manufacturing processes. They also visited the Toyota veteran I spent an afternoon with–Mitsuru Kawai, Senior Technical Executive. These days it is provocative to put people before technology since technology seems to take center stage.
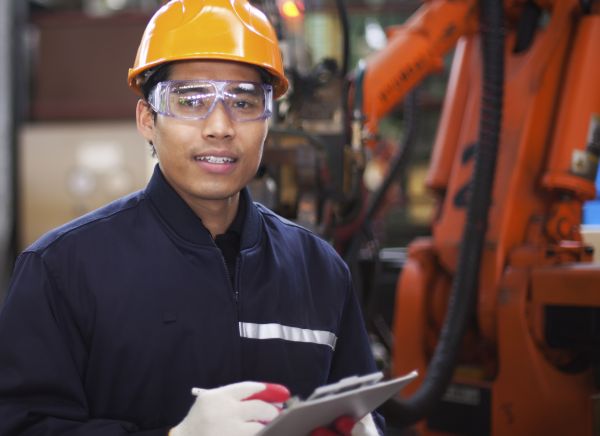
Bloomberg news recently ran a story with the provocative title “Gods’ Make Comeback at Toyota as Humans Steal Jobs From Robots.” The news journalists spent time in Toyota’s plant next to Toyota City headquarters that I wrote about last summer related to automated manufacturing processes. They also visited the Toyota veteran I spent an afternoon with–Mitsuru Kawai, Senior Technical Executive. These days it is provocative to put people before technology since technology seems to take center stage.
The Bloomberg article described a section of a forging plant where people took over for robots. This was originally a production line in Brazil set up 75 years earlier to make crankshafts and other metal parts for a variety of low volume engines. Originally, the plant was not cost-effective and was slated to be closed, but Taichi Ohno took the challenge to make it cost-effective with flexible cells and succeeded.
When production finally halted in Brazil, Kawai asked to have all the equipment shipped to the Japan plant where they set up the “basic TPS line” for Toyota Production System training. Kawai, a half century-long company veteran tapped by President Akio Toyoda to promote craftsmanship at Toyota’s plants, believes that technicians and engineers must understand forging intimately, in every detail, to improve the complex robotics and automation that now do almost all the forging in the plant.
“We need to become more solid and get back to basics, to sharpen our manual skills and further develop them,”Kawii explained to Bloomberg. “When I was a novice, experienced masters used to be called gods, and they could make anything.”
This does not mean Toyota is abandoning robotics and computers in manufacturing. Manual work such as this is still a small portion of the work of forging, machining, welding and painting, while stamping and injection molding are all done by machine. Toyota’s philosophy of production engineering is captured in the saying “simple, slim, and flexible.” Toyota had experimented with increasing levels of automation in engine, transmission and assembly plants and discovered they had gone too far too fast. Automation for the sake of replacing people requires a great deal of investment in fixed costs, as well as huge maintenance costs. Toyota toned down the automation, and today you will see limited manual welding, manual painting, and machining lines staffed with people who load and unload machines in cellular layouts.

The desire for lower fixed costs and greater flexibility really hit home in the Great Recession when Toyota, famous for adapting to large drops in demand, was stuck with fixed costs and lost money for the first time in fifty years. On reflection, Toyota redoubled efforts to reduce fixed costs, which included a new “global engine assembly line” with far less automation than its presumably more advanced predecessor. Akio Toyoda is often quoted for his decision for a moratorium on building new manufacturing plants for three years at a time when sales are booming and when journalists assume he wants to slow growth in the wake of the recall crisis. Toyota has taken many measures in response to that crisis, but the reason Toyoda did not want new plants going up was to force kaizen and prevent another buildup of fixed costs. It is easy to get extra capacity by building new factories or adding on square footage. It takes much more thought and hard work to shrink your current footprint in a plant and get more product out with the space you have—this is one of the famous Toyota challenges.
Indeed the benefits of retaining manual processes go beyond reducing fixed capital costs. The benefits are in building craft “gods” who can continually achieve amazing feats of improvement in cost reduction, quality, and space savings. The experience of performing the manual jobs, eliminating waste through kaizen, and then tackling waste elimination in the automated processes has led to a 50 percent reduction in the square footage of the “basic TPS line,” and major productivity, space, and quality improvement on the automated production lines in a three-year period. In fact, Kawai has the ongoing task of increasing productivity by two percent each month and has had that task for 50 years.
Kawai was tasked by Akio Toyoda to bring this training across Japan, and so far, has created about 100 manual stations in plants teaching the basic methods of waste elimination through TPS. An important part of this is reducing energy waste. Currently, we see more use within Toyota and its key suppliers of weights, balances, and counterbalances so gravity can move materials without electricity.
The real goal is reinvigorating a deep understanding of TPS in engineers and technicians. This is one thing Akio Toyoda saw weakening as Toyota grew rapidly from 2000 to 2008 with many retirees and many new hires globally. Japan is still the hub of innovation, especially in production engineering. To keep that innovation alive, Toyota believes in the master craftsman model. Robots are very reliable at doing a repetitive task, when people meticulously maintain them, but only people’s ingenuity can create simple, slim, and flexible systems. It takes people with deep craft knowledge, who can do the job manually, to continually drive out waste in complex technical systems. In the end, Toyota builds people before it builds cars.
Dr. Jeffrey Liker is professor of industrial and operations engineering at the University of Michigan and author of The Toyota Way. He leads Liker Lean Advisors, LLC and his latest book (with Gary Convis) is The Toyota Way to Lean Leadership.
- Category:
- Industry
- Manufacturing
Some opinions expressed in this article may be those of a contributing author and not necessarily Gray.
Related News & Insights
Manufacturing, Construction
The Evolving Role of Electric Vehicles in Sustainable Construction & Design
Industry
October 18, 2024Manufacturing
Sustainable Manufacturing Creates a Culture of Caring
Industry
Distribution, Advanced Automation
Shining a Light on the Lack of Fully Automated "Dark Factories"
Industry
September 27, 2024