Navigating an Essential Industry in Uncharted Territory
The coronavirus pandemic sweeping the world has been referred to as “unprecedented,” “once-in-a-generation,” and called an event that is having “global repercussions.” All this is true—but people in the essential food & beverage supply chain have real-world, life-and-death decisions to make. This is not hyperbole: The transformative nature of this crisis presents companies with unparalleled circumstances.
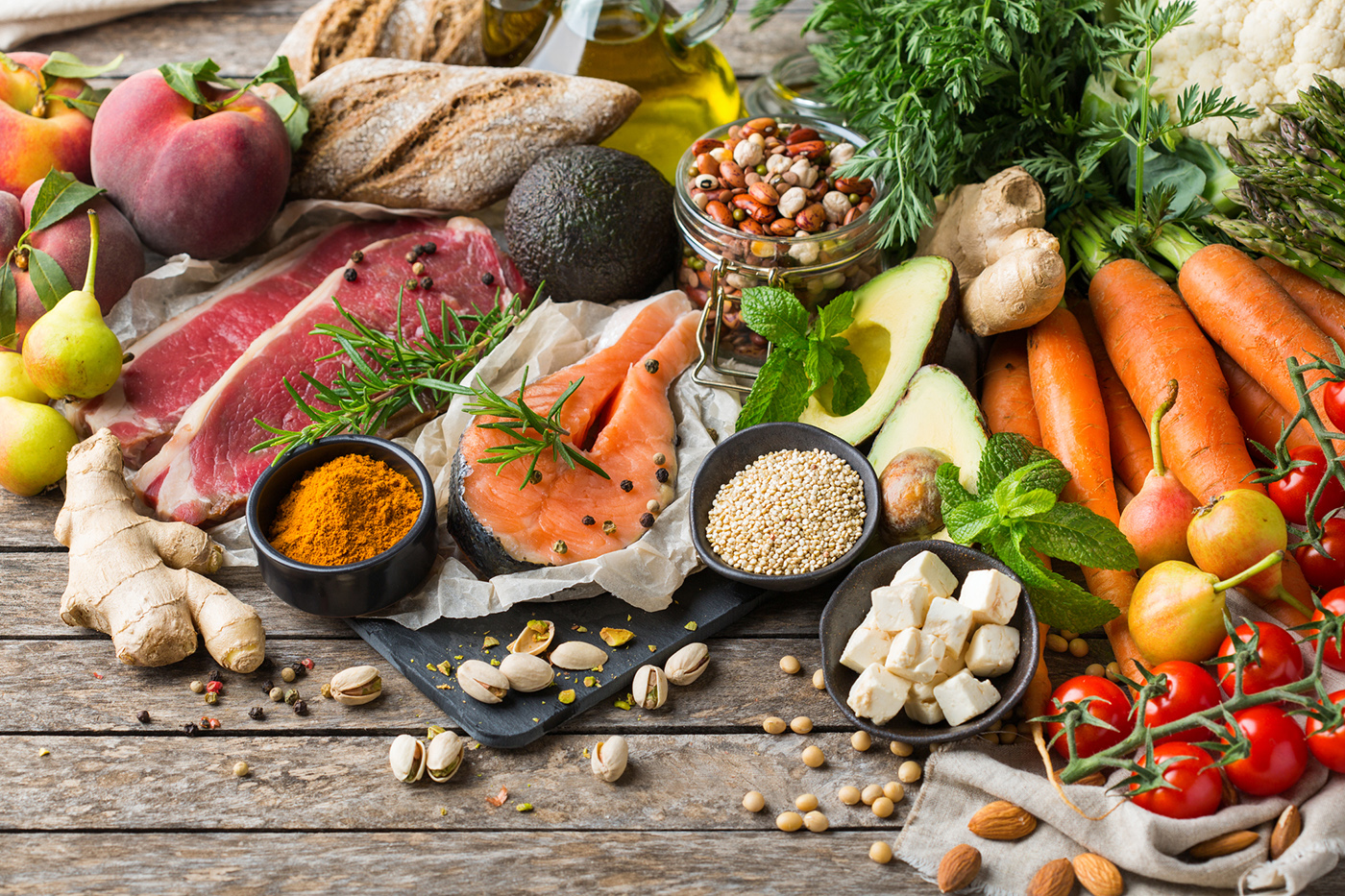
One of the main challenges facing food processors during the pandemic is the need to ensure that workers are staying safe and that their businesses are in compliance with governmental guidelines. Unfortunately, pandemic planning is not generally top-of-mind for many organizations.
Pandemics occur with less frequency than other crises (such as hurricanes, earthquakes, tornadoes), so we have not experienced many of them—certainly, nothing of this scale—in order to test that current systems are resilient and adaptable. Therefore, companies are navigating their businesses and their workforces through largely uncharted waters.
It is imperative to remember that the COVID-19 pandemic is novel; consequently, information on how to respond to the disease is evolving. Dr. Anthony Fauci, Director of the National Institute of Allergy and Infectious Diseases, and America’s top disease expert, now-famously averred: “You don’t make the timeline, the virus makes the timeline.” The same could be said for information on how to respond to the virus; it is crucial to keep up with information about this evolving disease—as the crisis evolves.
Organizations looking for guidance on where to start in their pandemic response have looked to information provided by public health agencies, such as the CDC. In addition, OSHA has published a document called “Guidance on Preparing Workplaces for COVID-19” that has been particularly helpful as a starting point for many businesses.
Also, in order to stay updated daily, the U.S. FDA puts out a “Daily Roundup” of press announcements, guidance clarification, and other useful information to help those in F&B industry stay abreast of the latest developments.
F&B Response to COVID-19
F&B processors are officially classified as “essential businesses,” so most have remained open—many with ramped up production due to the sudden increase in demand. However, the recent news about some processing plants having to shut down due to coronavirus outbreaks (and the negative publicity some have garnered as a result) has many F&B processors focusing on worker safety to keep operations up and running.
Some good news, though: There are strategies being used to keep workers safe, in line with FDA guidelines. Social distancing, encouraged handwashing routines for workers within the facility—and a restriction or reduction of travel and meeting attendance for those in office positions are just a few of the most common, easily-implemented strategies.
Industry Concerns
A recent report, based on a survey conducted by Clear Seas Research for Food Engineering magazine, gives a glimpse into how the F&B industry is responding to the challenges of COVID-19 and the things that are of most concern for those on the “front lines” of the industry. Generally, the report indicates that most are focusing on business goals, but the safety of both their own families and their workers’ health is a major concern.
The top concerns in the survey included the economy and both short- and long-term business goals. More than half of those surveyed (53%) indicated worries about supply chain challenges, as well. Disruptions in the supply chain come into play when there are state-by-state, rather than national guidelines. In some cases, this can result in lost freight costs if, for example, a company places an order and is not aware of closed shipping docks or a forced closure after the order has been placed.
The most prevalent economic/business concerns, however, dealt with new business development and spending. Some 63% of those surveyed indicated that product innovation has declined, along with 66% reporting a reduction in new business spending.
Personal concerns loom large, as almost half of respondents (49%) say they are worried about contracting the disease themselves—and a whopping 72% are worried about friends or family. Less than half (45%) are worried about employees not showing up for work, according to the survey.
Beyond Meat: Food Shortages Elsewhere
Another grim reminder of COVID-19’s affect on the F&B world relates to shortages. As the pandemic spreads beyond the meat processing plants that have captured much of the national spotlight, a new study from Environmental Working Group estimates that more than 60 food processing facilities outside the meat-packing industry have seen outbreaks, with more than 1,000 workers diagnosed with the virus.
In reality, the numbers gathered by the group might be much higher, according to a recent article in the Los Angeles Times. According to the Times, the advocacy group compiled its figures using local media reports, because there are no federal agencies reporting the data. “The true total is almost certainly higher. Fruit and vegetable packers, bakers, and dairy workers are risking infection as the virus spreads through processing plants where employees deemed essential have mostly remained on the job during the pandemic, sometimes laboring in close quarters.”
Such outbreaks expose a vulnerability in America’s food supply. Grocery store shortages have already been felt when the meat industry was forced to order plant shutdowns. “Even as that situation eases, more shortfalls of individual food items and ingredients are likely in the months ahead unless the virus’ spread is slowed at food-processing plants,” said Kevin Kenny, Chief Operating Officer of Decernis, an expert in global food safety and supply chains, in the Times article.
Addressing Workers’ Anxiety
Many Americans are anxious, often due to the above-mentioned confusion and in light of the mixed messaging and continued uncertainty about the virus. This doesn’t stop when employees enter their workplace. There are multiple things companies are doing to address employees’ confusion and anxiety.
Clear communication is key. Workers need to feel their health and safety are important. Companies need to develop and disseminate clear guidance for their employees. It is also important to clearly communicate the state of the company. This might mean revising guidance several times, in light of new information.
Technology in a Pandemic
Many companies have embraced technology during the COVID-19 pandemic. From remote communication tools to AI to EHSQ software, never has technology been more necessary to connect people and help with production challenges than it has in 2020.
In a recent interview with Sean Baldry, Product Marketing Manager, Safety & Health Solutions, at Cority, the subject was how F&B companies can utilize technology—both now and in the future. Baldry named the following examples of interesting applications and use cases for technology in light of COVID-19:
- Deploying artificial intelligence to identify people who are not wearing face masks and issuing an announcement, via smartphone apps, to inform them to put one on.
- Use of drones to identify potentially infected persons or contaminated surfaces with thermal imaging technology.
Such company’s software solutions offer many specialized tools that organizations can use to help them manage during this time. They include medical screening, worker absenteeism tracking, and more.
Baldry concluded: “The overarching idea from these tools is to manage the entire breadth of the pandemic response from a single location; to simplify and streamline their workflows to save time; and to give high-quality, real-time data to help make the best decisions available to keep people safe and maintain business operations for as long as possible.”
Meanwhile, as businesses begin the process of reopening, the future is still far from certain. F&B processors are committed, however, and continue to maintain the resilience that has helped them adapt to other crises. This happens through working together—and keeping up with the science and technology available to guide them through this difficult time.
Some opinions expressed in this article may be those of a contributing author and not necessarily Gray.
Related News & Insights
Food & Beverage
Gray Project Receives Manufacturing Innovation Award
Corporate News, Industry
December 04, 2024Advanced Technology, Automation & Controls
Four Use Cases for AI's Growing Role in Manufacturing
Industry
November 25, 2024Data Centers
Gray Expands Reach with Dallas Office
Corporate News
November 14, 2024