LEED Silver Certificate & Plaque Presented to USPS
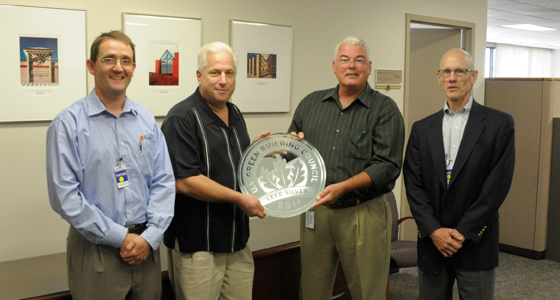
On Thursday, June 30th, Gray Construction presented the LEED® Silver certificate and plaque to USPS for the St. Paul Processing & Distribution Center (P&DC) in Eagan, Minn. The 611,538 s.f. facility was an expansion to the existing Bulk Mail Center and was designed and constructed in two consecutive phases over a 770 day schedule. Although not part of the original project requirements, the customer requested that Gray pursue LEED certification when the overall project was approximately 50% complete. Following that request, Gray adjusted the design and construction plans to accommodate the requirements associated with LEED certification. The USPS St. Paul P&DC is a continuation of the 16+ years between Gray and USPS.
Elements of sustainable construction incorporated into the facility include:
- Brownfield redevelopment.
- Native landscaping that does not require irrigation.
- Preferred parking for fuel efficient vehicles, low-emitting vehicles, and carpools; proximity to public transportation and community services.
- Over 40,000 tons of existing pavements were crushed and processed on-site to provide aggregate base for use under new pavements.
- Light pollution reduction & heat island reduction.
- Energy efficient building system that exceeds ASHRAE 90.1 requirements by 30%.
- No CFC based refrigerants.
- Enhanced commissioning of building systems.
- Over 70% of on-site generated construction waste was diverted from landfills through the use of recycling.
- Over 20% of the total building materials content, by value, was manufactured using recycled materials.
- Over 40% of the total building materials content, by value, was comprised of materials and products extracted, harvested or recovered, as well as manufactured within 500 miles of the project site.
- Outdoor air delivery monitoring.
- Low-emitting adhesives, sealants, paints, coatings, carpets, and composite wood products were utilized to reduce the quantity of indoor air contaminants.
- Indoor Chemical & Pollutant Source Control.
- Individual and networked lighting controls.
- Energy Control & Management System for HVAC systems.
- The electrical switchgear rooms are ventilated using excess air from the workroom allowing for increased ventilation in the workroom and eliminating overheating in the penthouse without adding mechanical cooling.
- Vertical storing dock levelers are utilized allowing full sealing at enclosed platform doors reducing air infiltration when the dock doors are closed.
Gray, which has customers throughout the United States, has been designing and building to LEED guidelines for several years. If you have distribution center construction needs, please contact Steve Summers, Executive Vice President, Distribution Market at ssummers@gray.com. If you would like more information regarding LEED construction, please contact Bob Lowry, Senior Vice President at blowry@gray.com.
- Category:
- Corporate News
Some opinions expressed in this article may be those of a contributing author and not necessarily Gray.