Lean Manufacturing - Automotive Suppliers Recognize That Less Is Often More
No matter what anyone says, good things can come from a bad economy. No one understands that better than the folks leading America’s automotive companies—from the domestic and international assembly plants, to the scores of companies that supply them. A three-year recession forced this industry to become smarter, leaner and more productive. And with demand for new cars and trucks soaring once again, for suppliers, the new challenge isn’t staying afloat, but keeping up with demand.
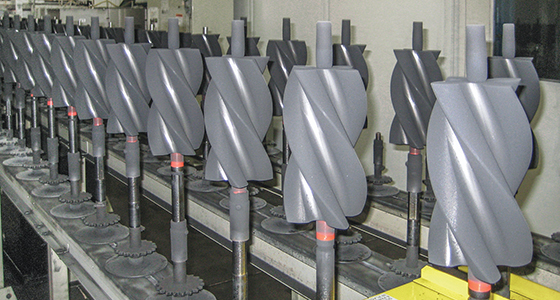
No matter what anyone says, good things can come from a bad economy. No one understands that better than the folks leading America’s automotive companies—from the domestic and international assembly plants, to the scores of companies that supply them. A three-year recession forced this industry to become smarter, leaner and more productive. And with demand for new cars and trucks soaring once again, for suppliers, the new challenge isn’t staying afloat, but keeping up with demand.
Lean Manufacturing in Automotive
Bernard Swiecki is assistant director of the Automotive Communities Partnership at the Center for Automotive Research (CAR) and manages CAR’s analysis of vehicle sales, production, and segmentation data, in addition to authoring a monthly column on the automotive industry. He says that, in response to the U.S. economic downturn, some 2 million units worth of parts were taken out of the automotive supply chain to decrease volumes. Some suppliers were forced to shut down plants, while others reduced headcount and invested less in new equipment to keep the doors open.
Now that new life has been breathed into the U.S. automotive industry, suppliers are once again bustling with activity, with some just under or approaching full capacity. Even with clear signs that the economic recovery is here to stay, Swiecki says suppliers are reluctant to make new capital investments until it is absolutely necessary.
“So, what they’ve been doing is either adding shifts or finding ways to increase efficiency of their manufacturing operations by increasing productivity and working overtime,” began Swiecki. “Or, when they have a contract for which they specifically need new tooling or new space that is when they will add (capacity), and they will only add enough to cover that contract. There isn’t a buffer that’s being built into the equation.”
Eaton, one of the largest suppliers to the global automotive industry, is one company feeling the pressure to keep up with the increased demand for parts, but is energized to take on this new challenge.
Lean Manufacturing Challenges Automotive Manufacturers to React Quickly.
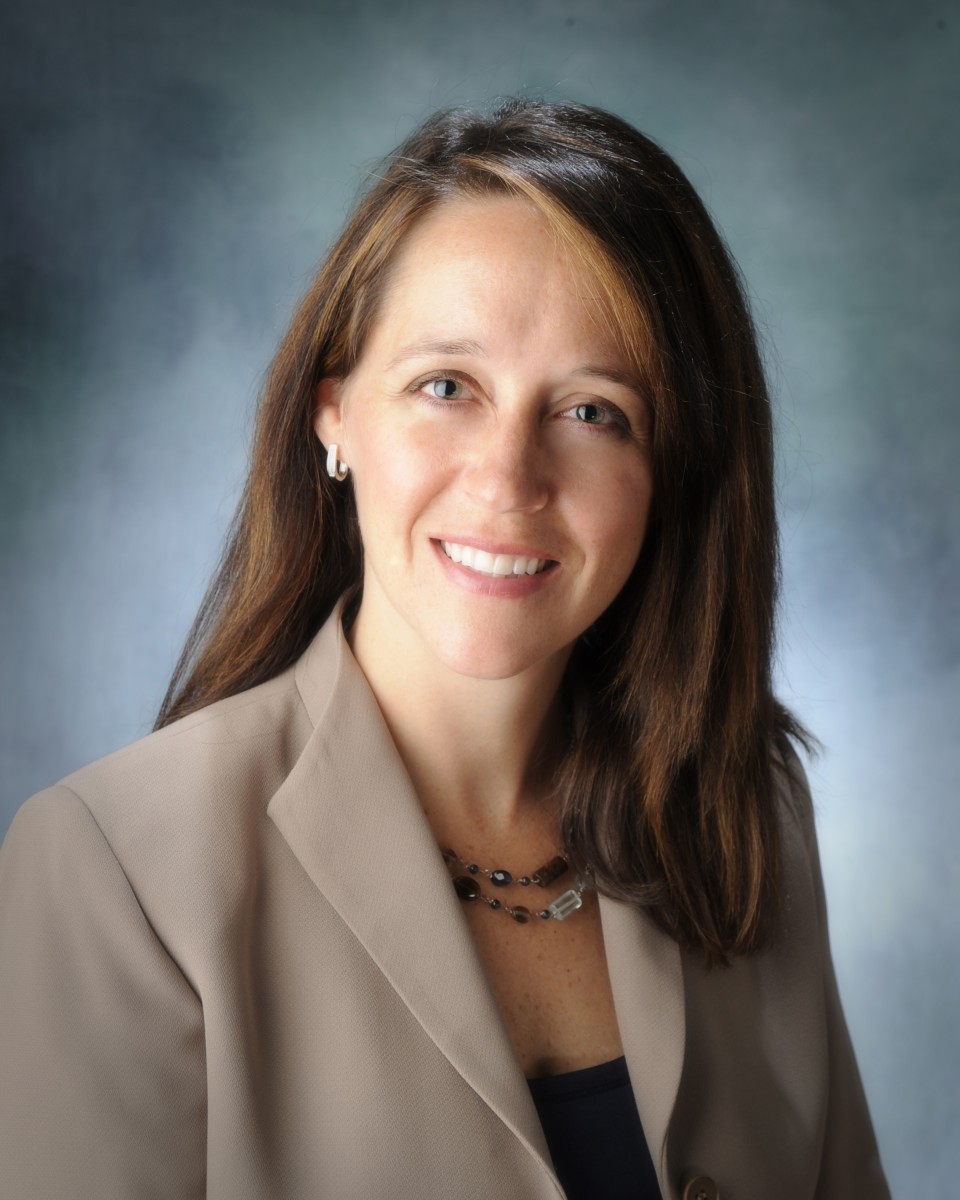
Staci Kroon, president of Eaton’s North American Automotive division, is a 17-year veteran of the automotive parts industry and says, while recovering volumes are indeed causing automotive suppliers some strain, another challenge is reacting to the much quicker rate at which customers are launching new vehicles.
“Even though the capacity to make a product is there, you still have to make modifications to make the new product,” said Kroon. “Just because you can make a given component doesn’t mean it’s the right component for the launches that are happening. So that level of activity is not just around units produced, but it’s around the complexity that’s created in the manufacturing environment when you have all these new launches going on, and the products are more advanced than they have been in the past.”
To deal with this “good” problem, Kroon says Eaton is finding ways to utilize equipment differently than they had in the past, running production lines six-to-seven days a week. She says the company has also added staff and new production lines, and has increased overtime.
This year, Eaton has filled nearly 40 new roles and has several salaried positions in engineering, technology, program management, and finance still open.
Despite the challenges automotive suppliers are facing today, Kroon believes the industry is well-positioned to thrive in what has become the “new normal” business of automotive manufacturing.
“It’s not like this has been sneaking up on us,” Kroon said. “We’re all very aware, and we’re having a lot of conversations around it. I think that sets us up for success better than if it came as a big surprise, like it did in ‘08 and ‘09. We weren’t ready for that downturn. We’re ready. We’re preparing for the volume increase.”
- Category:
- GrayWay
- Industry
- Manufacturing
Some opinions expressed in this article may be those of a contributing author and not necessarily Gray.
Related News & Insights
Advanced Technology, Automation & Controls
Four Use Cases for AI's Growing Role in Manufacturing
Industry
November 25, 2024Data Centers
Gray Expands Reach with Dallas Office
Corporate News
November 14, 2024Manufacturing, Construction
The Evolving Role of Electric Vehicles in Sustainable Construction & Design
Industry
October 18, 2024