Large Manufacturing Follows Attractive Labor Market to Southern USA
Due to southern states investing in job-training and customized workforce development programs, the South is becoming a top choice for new plant construction.
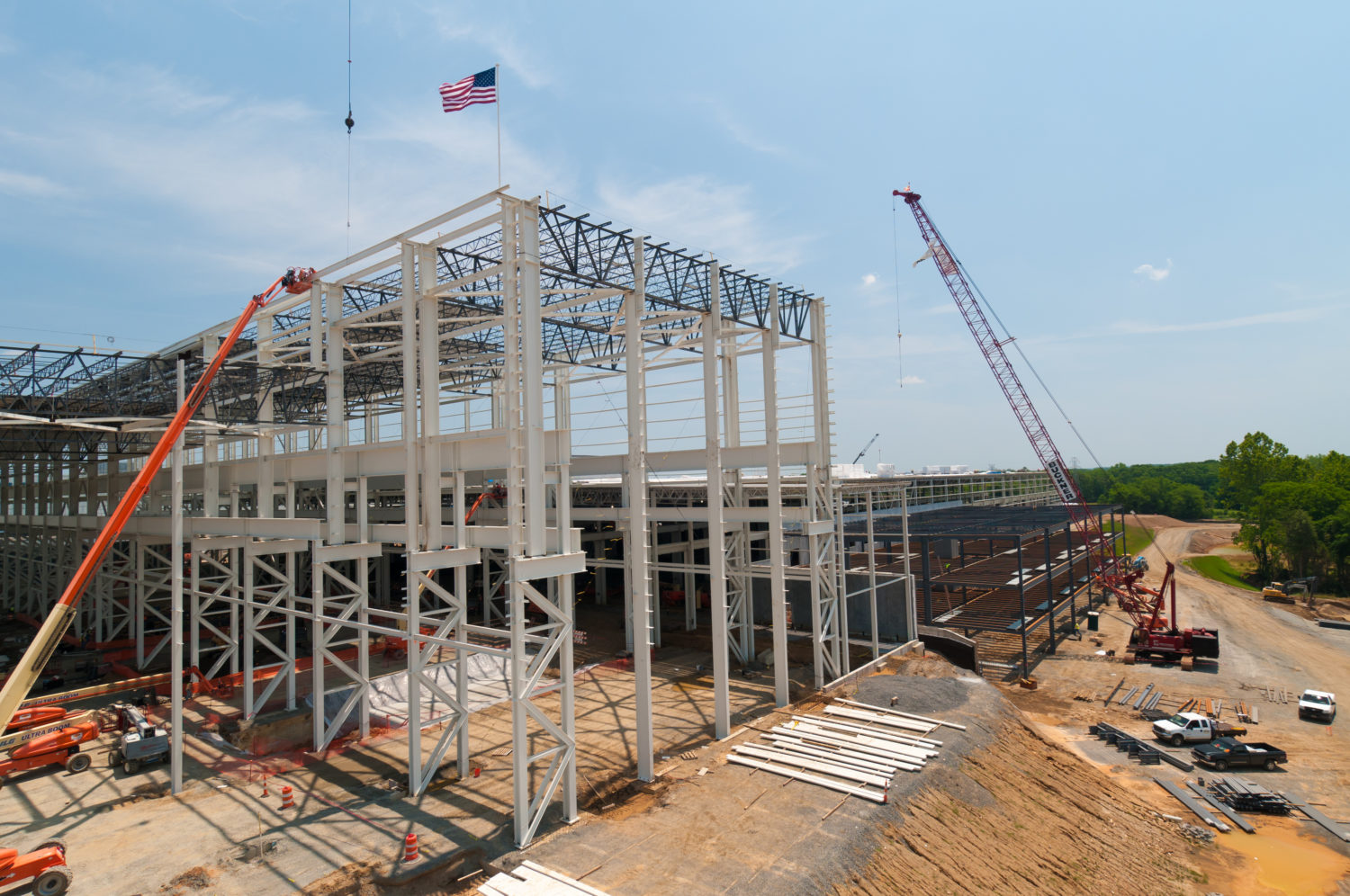
Skilled Labor Available at Lower Cost, Reduces Risk to Manufacturers
There is no question the South naturally possesses qualities that are important to business and industry—lots of available land and real estate, large labor pools, wide and varied transportation outlets supported by sound infrastructures. But businesses can’t survive on these alone, especially given the instability of the U.S. economy today.
Complementing the South’s large labor pool is its low cost of labor and increasing workforce development opportunities. According to the Bureau of labor Statistics, the median hourly wage across all occupations in Alabama, for example, was $14.26 in 2010, while Connecticut’s was $19.56—a significant difference indeed.
Some might assume a lower wage translates to a less skilled workforce, but southern states are wisely investing in vocational and technical training programs, and southern colleges and universities are rising in the national rankings each year according to U.S. News and World Report’s Best Colleges of 2011.
Vocational Training Investments Paying Off For States
A good example is Alabama, which boasts an educational and job-training institution that is part of the Alabama Community College System called AIDT (Alabama Industrial Development and training). Pre-employment and on-the-job training services are offered by AIDT—at no cost—to new and expanding businesses throughout the state.
“We have the best, and that’s not just my opinion,” said troy Wayman, Mobile Area Chamber of Commerce’s vice president of economic development. “AIDT is part of the two-year college system… and I would say, when it’s all said and done, it’s our strongest incentive.”

Austal USA MMF, Phase two, Mobile, Alabama
If you need more proof, just ask one of AIDT’s beneficiaries—Austal USA. Australian-based Austal is the world’s leading manufacturer of aluminum commercial and defense vessels and has a modular manufacturing facility in Mobile. Joe Rella, the company’s president and chief operating officer, has nothing but praise for AIDT and says the program functions as the primary training arm for Austal.
“There’s a maritime training center built adjacent to our property to support the trade skills and development that we need,” said Rella of how AIDT customizes training just for Austal. “In collaboration with AIDT, Austal has developed a curriculum that uniquely qualifies our pre-hire trainees with the necessary skills to be our future shipbuilders. AIDT and Austal instructors work together to ensure that this program remains current and complete through continual revision and modification as our needs change. The maritime training center that is here is a 60,000 square-foot building and we have 40,000 square feet of that building for our exclusive use. To me, AIDT is the tie-breaker when it comes to which state you want to locate your business.”
States’ Customized Workforce Development Programs Provide Pre-Trained Labor
If the labor pool is not ready to take on specialized jobs, like Alabama, many other southern states are developing their own customized workforce development programs to ensure new businesses have the skilled workforce they need to succeed.
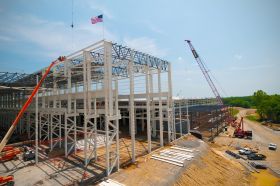
The Siemens Energy gas turbine plant
under construction in Charlotte, N.C.
Richard Voorberg is director of project management for Siemens Energy, Inc. and was heavily involved in the negotiations with the state of North Carolina for the Siemens location in Charlotte. While the area’s large labor pool was a draw, Voorberg noticed the lack of skilled labor available to successfully fill jobs at the new plant. That’s when the state stepped in with a customized workforce development program just for Siemens.
“The local community college system is working directly with us to help us scout the people to sift through the number of resumes that we get to test those individuals so that by the time they get to see a Siemens person, they’ve passed three or four tests,” said Voorberg. “We can see what their skill level is early on so we don’t waste a lot of time interviewing candidates that don’t have the basic knowledge that we need.”
Workforce development is just one piece of a much larger economic development pie. Customized incentive packages, geared specifically to the needs of individual businesses, are at the heart of many recruitment efforts by state governments and economic development organizations in the South.
“If I’m going to give free water line extensions to everybody, and your building already has a water line—that’s not an incentive,” explained Bob leak, president of Winston-Salem Business, Inc. “But, if you need 100 trained people delivered to your doorstep the day you open for business, if we provide that, then it becomes an incentive. Providing meaningful incentives that are tailored to the needs of the deal is something this state has done very well.”
- Category:
- GrayWay
Some opinions expressed in this article may be those of a contributing author and not necessarily Gray.
Related News & Insights
Food & Beverage
Gray Project Receives Manufacturing Innovation Award
Corporate News, Industry
December 04, 2024NexGen Spotlight: In Pursuit of Excellence
Stories
Advanced Technology, Automation & Controls
Four Use Cases for AI's Growing Role in Manufacturing
Industry
November 25, 2024