Killing the Manufacturing Skills Gap
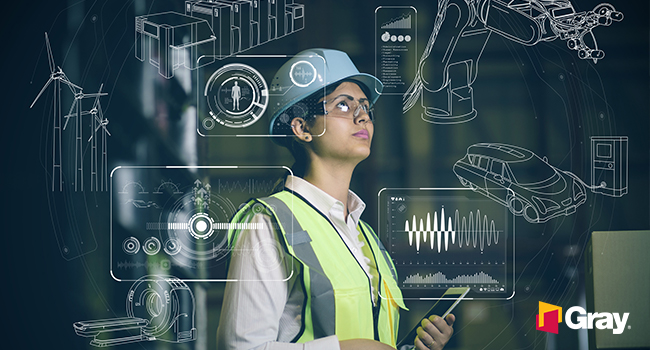
Contrarian views emerging on where to find manufacturing workers.
The numbers present a clear picture. American manufacturers are experiencing a lack of capable, prepared workers. Deloitte Consulting LLP and the Manufacturing Institute have said, over the next decade, nearly 3.5 million manufacturing jobs will be needed, and 2 million are expected to go unfilled due to a STEM (science, technology, engineering and math) skills gap.
In automotive manufacturing alone, an industry employing more than 948,000 workers and enjoying record-breaking sales, skills shortages are looming. Kristin Dziczek, director of the Industry, Labor and Economics Group of the Center for Automotive Research in Ann Arbor, Michigan, says “Demographic and technological trends are critical threats to the U.S. automotive industry’s ability to meet future talent demands. The U.S. automotive leadership position is in jeopardy.”
By demographic trends, she means more than half of automotive manufacturers expect to lose 20 percent or more of their workforce due to aging and retiring workers. Some 75 percent also anticipate major challenges in finding the workers they need to fill positions that require skilled and prepared workers.
Automation: Friend or Foe?
Many industry observers, particularly in the automotive sector, see manufacturers looking to robots and other automation strategies involving sensors, controllers and other components to address the skilled worker shortage.
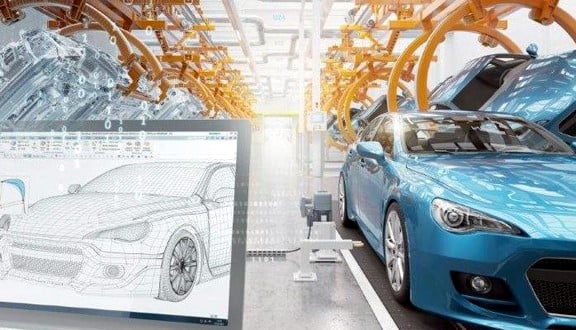
Motion control-related components also set sales records. The fastest-growing categories in the first nine months of 2017 were motion controllers (up 24% to $147m), sensors and feedback devices (up 20% to $116m), actuators and mechanical systems (up 13% to $479m) and motors (up 11% to $1b). The majority of suppliers believe that order and shipment volumes will continue to increase over the next six months. According to the Association for Advancing Automation (A3), 27,294 orders of robots valued at approximately $1.473 billion were sold in North America in the first nine months of 2017, the highest level ever recorded in any year during the same time period. Automotive-related orders are up 11 percent in units and 10 percent in dollars, while non-automotive orders are up 20 percent in units and 11 percent in dollars.
So, is manufacturing employment contracting in the face of increasing automation projects? Surprisingly, no. In a recent Milwaukee Journal-Sentinel article, staffing company ManpowerGroup, after overseeing a huge survey of employers worldwide on the impact of automation, had this message for workers: Don’t fear the robot.
Among the employers polled, only 10 percent told ManpowerGroup that automation would prompt headcount reductions over the next two years. Twice that share (20%) said they expect to add workers because of increased use of digital technology. U.S. employers were among the most optimistic, with 25 percent saying automation will increase their headcounts in the near term. But, the comparable figure in China, where manufacturing is more labor-intensive, was only three percent.
Worldwide, headcounts will increase in jobs involving information technology, manufacturing and customer-facing functions due to increasing digitization, the survey found.
Training for Skills
While many manufacturers continue targeting STEM-educated workers, others are focusing on supplying training as much as a production job, leaving them free to hire those who are most interested in the work.
New Jersey Precision Technologies Inc. (NJPT), located in Mountainside, New Jersey, is one of the largest EDM (electro-discharge machining) shops in the country. Its products are found in medical devices, aerospace products, plastic extrusion tooling, molds, dies, automotive components and consumer products.
There are a number of keys to NJPT’s success, but one that president Bob Tarantino told manufacturing training advocate Wayne Cheneski is this – training is consistent, ongoing and at the forefront of the shop’s overall business strategy. As he puts it, “Training is one of the most important things we can do to make sure we make the best possible products for our customers.”
Often, he hires those with very limited experience for entry-level positions in favor of those who have a real interest in technology and making things. Each new hire spends the first week on the job in some type of formal onboarding and training program that includes a combination of classroom study in the company’s technical training center and on-equipment training in the shop.
In addition, Tarantino is a firm believer in the power of cross-training, not just on different machines, but covering different departments. EDM operators, for example, spend time in the engineering department learning procedures and design methodologies. Engineers and management personnel undergo the same training as EDM operators, supplemented with additional instruction about document control, drawing revision procedures and the company’s enterprise resource planning software. The goal is to expose employees to as many areas of the operation as possible and equip them with a broad range of critical skills. “As a job shop, cross-training allows us to put resources where they are most needed without having to increase or decrease staff based on changing workloads. It helps us all,” Tarantino says.
Computerized machine tools, emerging technologies such as laser processing and 3D printing and digital art-though-part production are changing the very nature of what it means to manufacture something. But, hiring bright-eyed men and women and training them for related skills means progressive manufacturers need to never fear a skills shortage.
- Category:
- Industry
Some opinions expressed in this article may be those of a contributing author and not necessarily Gray.
Related News & Insights
5 Ways for Construction Workers to Put Safety First This Winter
Industry
Distribution, Construction
7 Trends Set to Dominate the Manufacturing Industry in 2018
Industry
Food & Beverage, Design
New Kraft Heinz Iowa Factory Awarded Food Engineering Magazine’s 2018 Plant of the Year
Corporate News
January 09, 2018