How EPMC™ is Changing the Food & Beverage Industry
The EPC model — engineer; procure; construct — is well-known in the design-build industry as a process for not just building a food & beverage plant, but also procuring, automating, and installing the equipment needed.
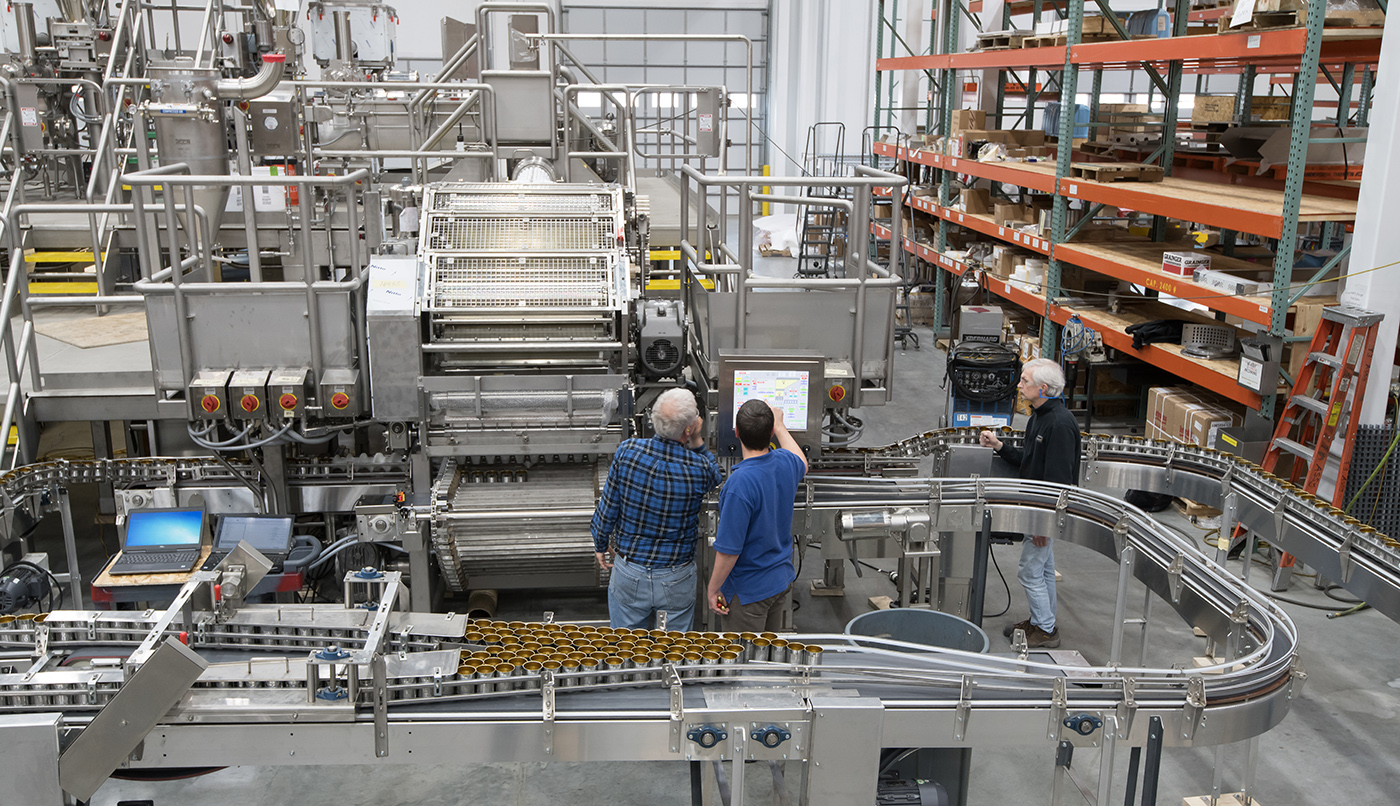
The benefit is clear. By integrating machine specifications, procurement, and installation into the engineering process, food & beverage processors can ensure that equipment is properly integrated into the building and its operating conditions. While EPC is a comprehensive model, there can still be collaboration gaps, especially related to the manufacturing of specialty equipment and specialty hygienic fabrications. For most processors, the equipment is the heart and soul of the facility. The quality, delivery, integration, and performance of that equipment is critically important. To avoid collaboration gaps, the process engineers and plant operators need to have deep transparency into the equipment manufacturing capability and delivery.
That’s where the EPMC™ — engineer; procure; manufacture; construct — approach comes in. Adding manufacturing as an in-line part of the process necessitates earlier conversations with the equipment manufacturer, meaning that quality and performance expectations and timelines for equipment are laid out before any construction begins. EPMC™ project teams will have real-time visibility into raw material supply chains and equipment production sequences. This visibility has become even more important given post-COVID supply disruption and uncertainty. Having an architect, engineer, construction manager, process engineer, automation engineer, and machine builders all on the same team that have worked together previously is a good recipe for success.
But it is important to understand not only what EPMC™ is, but what it is not. It is not a delivery model by itself. It is an extension of the EPC model that builds in an extra step, when it makes sense to do so, instead of trying to apply a one-size-fits-all model to every project, says Tyler Cundiff, president, integrated process group, Gray, Inc.
In the traditional design-build model, which dates back multiple decades now, you had construction contractors adding design services in-house with a focus on the building.
“Next were those design-build companies, and some A&E companies, that evolved into a more integrated EPC firm, offering process and packaging engineering along with equipment procurement,” says Cundiff. “Now some of those EPC and A&E firms are adding robust digital and automation services. Where we are right now is really in this next phase of integrating everything, which you could almost call a fourth generation of design-build.
“Moving toward the next generation of integrated project delivery we are looking beyond just the traditional capabilities of EPC as we know it. We call this EPMC™.”
This EPMC™ approach is as much of a “flexible” approach as it is an integrated approach. While the fully integrated EPMC™ approach functions similar to the EPC delivery model, there are various hybrid capabilities where the services and manufactured products can be discretely bundled.
So, if EPMC™ only applies to the right kind of project, and it is not a delivery model in the traditional sense, why do it? Because when it fits, it offers cost, quality, and schedule control, harmonization and visibility to processors, who never can have enough of that for starting up a new production plant.
Automation drives change
A modern food & beverage plant is highly automated from the moment ingredients arrive on the loading dock to the time they leave the plant as finished goods. Automated production lines, data collection, material handling, and packaging are nothing new.
But it wasn’t so long ago that they were new, and the engineering and construction processes are still catching up. In many cases, there are still two distinct pieces of a plant project: The plant and the production line. The plant is automated, the production line is automated, but they aren’t necessarily automated together, or at least as closely together as they can be, says Cundiff.
“Now, we’re seeing the production line and the automation of the production line should be closely married to the facility,” says Cundiff. “It’s almost like everything is being smashed together from a services standpoint. Equipment is the only outlier when elements come together in a food operation.”
Under the EPC model, the solution to equipment being the outlier is process and packaging engineers designing a solution to integrate equipment into the facility. This often involves workarounds or engineering solutions to equipment that maybe isn’t a perfect fit but can be used to perform the desired task.
EPMC™ approaches this challenge from the other direction, by including manufacturing of equipment into the process. This creates the opportunity for custom-built equipment or modifications to meet the customer’s specific needs for each step of the production process. For example, if a customer needs a specialized piece of cutting equipment for its protein products, they can specify that up front. This way, there is ample amount of time for the custom equipment to be manufactured while the rest of the design-build process moves forward. Streamlining the process eliminates surprises at the end.
Gray’s specialty equipment manufacturing arm through Anderson Dahlen, a Gray company, and AD Process Equipment, a Gray company, are familiar with custom manufacturing, approaching each design, fabrication, and project with a personalized process.
“Identifying specialized equipment early on in design-build projects is an important factor in creating efficient operations,” says Perry Henderson, vice president, sales, Anderson Dahlen. “When the process equipment is not effectively planned, there can be delays in getting the plant up and running, or a facility may not be as efficient.”
Turnkey systems can increase production efficiency, quality, and consistency when there is enough time to custom build the correct system for the space, process, and product. Integrating the manufacturing of equipment into the EPMC™ model will provide food & beverage processors with a competitive advantage, performing at their best right at the beginning of a facility opening, rather than piecing together inefficient options.
The evolution of design-build
As Cundiff says, the design-build model is changing to meet the needs of modern food & beverage processing and adapting current methods to take advantage of modern technology. Technological advancements in design tools such as BIM and in production applications such as IIoT have allowed integrated project teams to explore new project execution capabilities at the speed-of-light. This evolution is still occurring today.
This next generation offers food & beverage manufacturers an integrated opportunity to secure highly critical equipment directly from your trusted project partner in a way that can be highly customized and automated and closely harmonized with the facility design-build team and the end-to-end process engineers. By adding manufacturing to the traditional EPC model, engineers can take a more holistic view of how the building and the process need to work together.
“Our approach to EPMC™ is that it is a flexible model for our customers where comprehensive products and services can be considered holistically,” says Cundiff. “As we’ve seen a variety of design-build models evolve over the years, we see our EPMC™ approach as a natural progression that processors desire.”
Related News & Insights
Food & Beverage, Engineering
EPMC™: Building on a Foundation of Trust
Industry
Manufacturing, Construction
The Evolving Role of Electric Vehicles in Sustainable Construction & Design
Industry
October 18, 2024Food & Beverage
Gray Ranks No. 1 in Food & Beverage for Third Consecutive Year
Industry, Corporate News
October 08, 2024