Gray Senior Design Manager Featured in The Lane Report
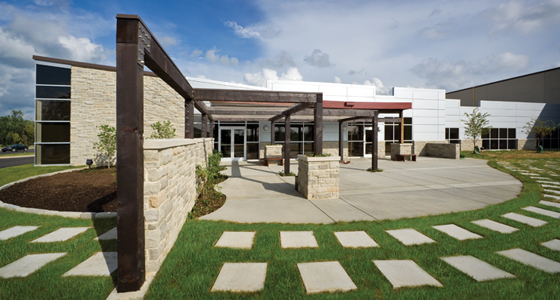
Gray Construction Senior Design Manager, Gary Hisel, was asked by The Lane Report to write an article on green building which was published in the September 2010 issue. The Lane Report is a business and economic news magazine focusing on Kentucky business.
If you have LEED construction needs, please contact Bob Lowry, Senior Vice President at blowry@gray.com. If you are interested in additional Kentucky Eagle, Inc. project information, please contact Gary Hisel, Senior Design Manager at ghisel@gray.com .
Please read Gary Hisel’s article from The Lane Report below.
Doing “The right thing”
A look at the route a project took to achieve LEED Certified status
The marketplace is asking for it and today there’s no impediment to do it: going green. Kentucky has almost 800 LEED APs (accredited professionals) and LEED Green Associates; Louisville has 320, Lexington has 288 in all walks of life from accountants to attorneys to architects and engineers to material suppliers. The availability of green products, either LEED or Energy Star rated, now includes every piece of the building project. Now, it’s also the “easy” thing to do.
So how can you make your building green?
In order to give you a better frame of reference, I’d like to share some LEED aspects of a recent 188,024-s.f. distribution facility in Lexington for Kentucky Eagle Inc., designed and built by Gray Construction. I was the senior design manager. Let’s take a look at the specific strategies used to make Kentucky Eagle the first Anheuser-Busch distributorship in the United States to gain certification under the LEED program – Leadership in Energy and Environmental Design.
First, you start with an owner who wants to do “the right thing” and requests, at a minimum, a LEED Certified building – see the U.S. Green Building Council at usgbc.org for more information. Beyond “Certified,” projects can achieve LEED Silver, LEED Gold and LEED Platinum status.
The first step was to take the LEED checklist scorecard and identify those categories and credits that we wanted to attain. The earlier the full green team is working from the same scorecard, the better.
It’s important to note that Kentucky Eagle’s project was scored under USGBC’s former 69-point LEED scorecard. The current system has a possible 110 points.
For the Kentucky Eagle project, since site work was already underway some of the Sustainable Site category credits were not obtainable.
However, we were able to achieve six points from the 14 available by incorporating such things as:
- Preserving more of the area green and minimizing storm water runoff, which resulted in 24.7 percent vegetated open space.
- Incorporating bicycle racks, changing and shower facilities.
- Assigning designated, preferential parking for fuel-efficient vehicles and those employees who choose to carpool, encouraging more environmentally friendly methods of transportation.
In Water Efficiency we obtained four credits of the five possible.
- No use of potable water for landscaping
- 42.3 percent reduction in water consumption through low-flow plumbing fixtures
- The result was a 50 percent reduction in total water used.
In Energy & Atmosphere we obtained three credits of the 17 possible.
- 18.7 percent reduction in total energy use, leading to substantially lower monthly energy bills for the larger new building than the owner was paying for the older facility, which turned out to be a surprising return on investment.
In Materials & Resources we obtained seven credits of the 13 possible.
- 83.7 percent of construction waste generated by the project was recycled, which meant 817 tons of material were not sent to the LFUCG landfill.
- 22.5 percent of the materials used to construct the new building were made of recycled material, including wood from a tobacco barn located on the property.
- 35.2 percent of materials in the project were manufactured regionally, which helped keep jobs local.
In Environmental Quality, we obtained seven credits of the 15 possible.
- No CFC-based refrigerants were used, which in turn limits further damage to the ozone layer.
- 100 percent of the paints, adhesives, sealants and carpeting systems used within the building meet LEED low volatile organic compound (VOC) requirements leading to a healthier workplace.
In Innovation in Design we obtained three credits of the five possible.
- Innovative lighting controls, architectural and interior design and the use of a LEED Accredited Professional all contributed to these points.
Each person reading this has benefited from Kentucky Eagle’s decision to go “green.” The result was less concrete, less water usage, less traffic, less energy usage, less waste and less harmful chemicals in the environment.
The deliberate decisions Kentucky Eagle made in order to attain LEED Certified on their new distribution facility offers a frame of reference as to how your project can do the same, or perhaps even better. The question remains – when will you go “green”?
- Category:
- Corporate News
Some opinions expressed in this article may be those of a contributing author and not necessarily Gray.