GE Sharpens its Focus on Advanced Manufacturing
James Surowiecki, columnist at the New Yorker, is one of the rare business journalists who understands today’s manufacturing industry. When GE sold most GE Capital assets last month, Surowiecki saw more than a story about a business decision— he saw the news as a sign that the manufacturing industry is entering a new era.
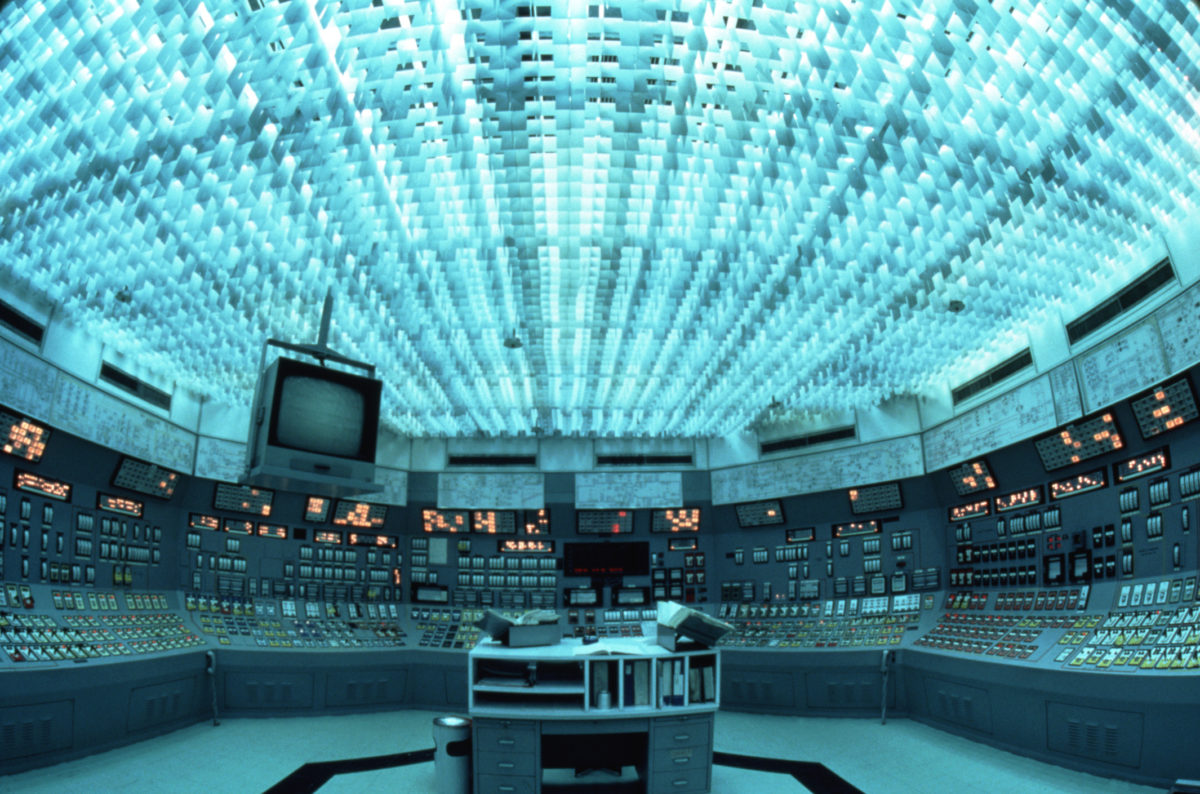
By refocusing on manufacturing, GE is betting on the industry’s continued growth and profitability. It is developing its high-tech industrial niches, looking to take a lead in durable goods like aircraft engines, medical devices, and power generation equipment. GE expects these and other industrial markets to produce more than 90 percent of earnings by 2018.
GE has revived industrial R&D, which had been slashed in half when the company’s focus was on financial products. GE is now breaking new ground in materials, machine-to-machine communication, big-data analytics for manufacturing automation and collaborative innovation.
Last year, we noted the rapid startup innovation approach GE is using to develop new products. Now, that process is being applied to industrial items like aerospace parts, not just consumer goods like air conditioners. In fact, one of its achievements by using the process demonstrates that not all additive manufacturing is alchemy. GE has enough control over the direct metal laser melting process to make parts such as a 3D printed temperature sensor, which recently cleared rigorous FAA standards for use in the next-generation LEAP jet engine.
In addition to these advances, GE is transforming production facilities into what it calls the Brilliant Factory. Such a plant uses sensors, data collection, analytics and other tools to optimize and adapt to problems and changing conditions. In a company publication, Christine Furstoss, global technology director at GE Global Research, said that the strategy improves insight into the manufacturability of parts, as well as optimization of cycle time, cost and yield. Even later, when a part is in use, data returns to engineering so it can improve design tools.
It’s clear that GE’s Brilliant Factory strategy does not miss profit opportunities. Furstoss has said, “If we could get across the whole of GE—not just one factory or product, but the whole company—if we could just get one percent productivity savings in our total supply chain, that could be up to $500 million for GE.”
Indeed, GE is not the only company to refocus on manufacturing. Not just in America, but around the world, global manufacturers are building and revamping super-efficient plants designed to consistently produce defect-free parts in customizable variety, synchronized to customer demand. James Surowiecki is now telling readers outside the manufacturing industry, “…the move from financial services back to industry could herald the close of an entire chapter of American capitalism… After 25 years of the financial tail wagging the industrial dog, it’s time to try something new.”
Karen Wilhelm has worked in the manufacturing industry for 25 years, and blogs at Lean Reflections, which has been named as one of the top ten lean blogs on the web.
- Category:
- Industry
- Manufacturing
Some opinions expressed in this article may be those of a contributing author and not necessarily Gray.