Flexibility at the Food & Beverage Forefront
The fact that consumers’ shopping habits have evolved—especially wanting more choices among brands and products—means flexibility is at the forefront more than ever for F&B manufacturers.
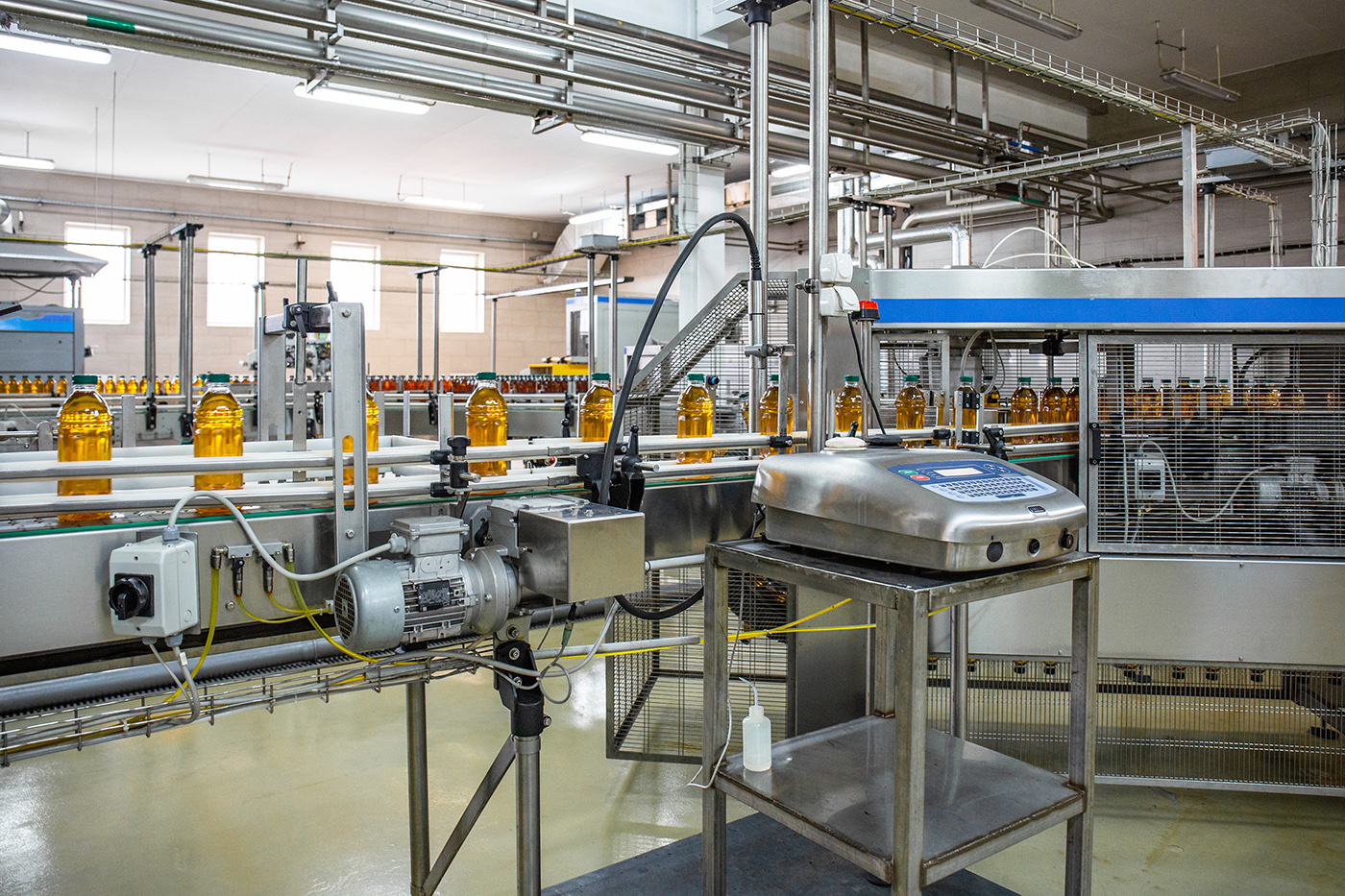
A recent survey conducted by Food Engineering magazine about plant construction safety revealed that a majority of food & beverage processors are increasing production to meet demand. However, what demand means today is not the same as it was even a decade ago. Previously, consumers were happy with long-running brands, and there was not a lot of choice among products. Now, says FE, “Consumers expect to choose from a wide choice of brands and products.”
We sat down with Dean Elkins, senior director of advanced automation with Gray Solutions, a Gray company, to discuss how food & beverage manufacturers are building more flexibility into their production lines.
Systems & Solutions for Flexibility
As consumer habits change, fueled by an appetite for more choices and faster deliveries, food & beverage manufacturers have turned to Gray to design new processes or revamp existing manufacturing facilities to allow for greater flexibility. “Everything begins with a consultive understanding of the customer’s needs and the challenges they are facing,” explains Elkins. “Bolstered by a greater use of Industrial Internet of Things (IIot), data acquisition, and data analytics, Gray will often employ process design and digital transformation tools that include modeling and simulation to emulate operations and demand created by a company’s warehouse management system (WMS)/warehouse control system (WCS) activity related to orders.” Emulation and simulation can provide a very accurate model of manufacturing and fulfillment throughput—often before a factory is built or modified.
Elkins mentioned that Gray has provided flexible control processes that “allow for efficient batching, metering, and mixing through the implementation of flexible, plant-wide control systems including advanced process control tools. These systems allow for the monitoring of material flow, temperature, and moisture content, along with other important process variables to insure the highest levels of process efficiency and quality.”
In addition, supplying a machine vision-based testing system that confirms batch and recipe data, in addition to date and time stamps, adds reliability to food & beverage manufacturing processes.
“Gray also routinely provides system solutions that utilize intelligent conveyors. Additionally, robots are utilized in testing, picking, packing, and palletizing applications to add further flexibility and accuracy to the manufacturing and order fulfillment process,” Elkins added. These devices are often programmed offline—this allows customers to gain even more operational efficiency.
As a highly qualified integrator of Automated Mobile Robot (AMR) and Automated Guided Vehicle (AGV) platforms, Gray works with manufacturers to enhance flexibility in material movement on both the manufacturing and fulfillment sides of an enterprise. Such devices, governed by fleet management software (which Gray interfaces to a company’s WMS/WCS software platform), are able to “move product to and from manufacturing operations, Automated Storage and Retrieval (AS/RS), and racking systems,” Elkins said.
Automation for Flexibility
Automation can be a way to speed up production in order to respond to consumers’ increased demands, but it’s also important for F&B manufacturers to know how to work with automated systems for maximum advantage. A systems design must be conducive to fast change-over in order to gain the flexibility’s true value, according to Elkins.
“Designs must be driven by data, with highly intuitive control architecture and operator interfaces allowing for operators to quickly respond to product changeover, recipe adjustments, or packaging differences based on demand,” he cautioned.
Flexible systems require flexible tooling that incorporates such features as servo motors, intelligent actuators, automatically adjustable conveyor guides on intelligent conveyors, and machine vision systems to ensure quality. He continued, “Flexible machinery, including case erectors, tray formers, and cartoners can be programmed to allow for rapid changeover as product runs with different packaging come into play.” In addition, robots can identify different pallet patterns based on the SKU that is being produced.
Modularity for Modern Manufacturing
The concept of modularity (or modularization) can help bring flexibility in automating production lines. It gives processors the ability to do batch experiments or even create new products—simply by re-configuring lines. According to Food Engineering, “Speeding up a production line through automation solves one problem, but when flexibility is important, some automation may have to be sacrificed. Modularity lets a processor roll equipment in and out of a line quickly to accommodate changes in products. When a successful arrangement is obtained, then additional automation can be applied.” Examples of modularity can be found in controls, programming, case packing, palletizing, and inspection.
Many of Gray’s control system designs and process designs incorporate a modular approach. “In many cases, utilizing up-front simulation allows for a basis to prove out the effects of adding modular equipment to a manufacturing line in phases—as production demands increase or change,” says Elkins.
Standard modules add production output, while reducing risk. This is due to the standardization of the design. There are other added benefits of module usage, including a lower total equipment cost through the elimination of non-recurring engineering costs; a lower cost of quality due to manufacturing process repetition; and speed-of-delivery for solutions.
Other Flexibility Factors to Consider
Aside from supply and demand, a few other factors play into the need for flexibility in food & beverage manufacturing. These include speed-to-market and product freshness, which can be aided by enhanced batching and mixing capabilities. Traceability is also extremely important, which includes data collection and analytics. The integrity of the data throughout the entire production process is also crucial. In addition, said Elkins, “Flexible storage of finished goods and reliable means of fulfilling factory orders are essential.”
Elkins stressed that the employment of flexible, data-driven order-picking methods, which include automated storage and retrieval systems and order picking automation (including robots and autonomous vehicles), are other proven means of enhancing flexibility.
Often, creative solutions and even new systems can be designed with increased flexibility in mind. Flexible metering and batching, based on demand, Elkins opined, can help shorten changeover time in food and beverage production. Flexible case erectors can also allow for the erection of multiple-size cases, which helps with packaging of multiple SKUs in varying case sizes.
Small-footprint, collaborative robot palletizing cells are another way to handle greater throughput with increased speeds and payloads. Elkins stated that “increased usage of AI tools will drive throughput, with fewer errors or scrap, while lessening the need for human intervention.”
Autonomous vehicles can create the free movement of manufacturing materials and free up essential floorspace, compared with conventional conveyor systems. “Evolution in control technology will continue to enhance fast set-up and changeover, while monitoring for the highest quality levels,” he concluded.
Conclusion
Flexibility in food & beverage manufacturing is more critical than ever. It can be achieved by utilizing data-driven analytics and digital transformation tools, as well as making use of modulization and flexible machinery. Creative solutions exist, including AI tools and robotics, along with strategic use of autonomous vehicles. Driven by data and implemented with either newly designed processes or revamped manufacturing facilities, it is possible to meet consumers’ ever-changing demands with flexibility and efficiency.
- Category:
- Industry
- Food & Beverage
Related News & Insights
Food & Beverage
Gray Project Receives Manufacturing Innovation Award
Corporate News, Industry
December 04, 2024Advanced Technology, Automation & Controls
Four Use Cases for AI's Growing Role in Manufacturing
Industry
November 25, 2024Food & Beverage
Gray & Morinaga Celebrate New Production Expansion
Projects
October 18, 2024