Equipment Manufacturers Must Automate to Stay Competitive in the Global Economy
To stay competitive, U.S. equipment manufacturers must find ways to increase the quality and throughput of their products and reduce costs in the process. This requires investment in technologies that maximize efficiencies and eliminate waste—most notably, automation and robotics.
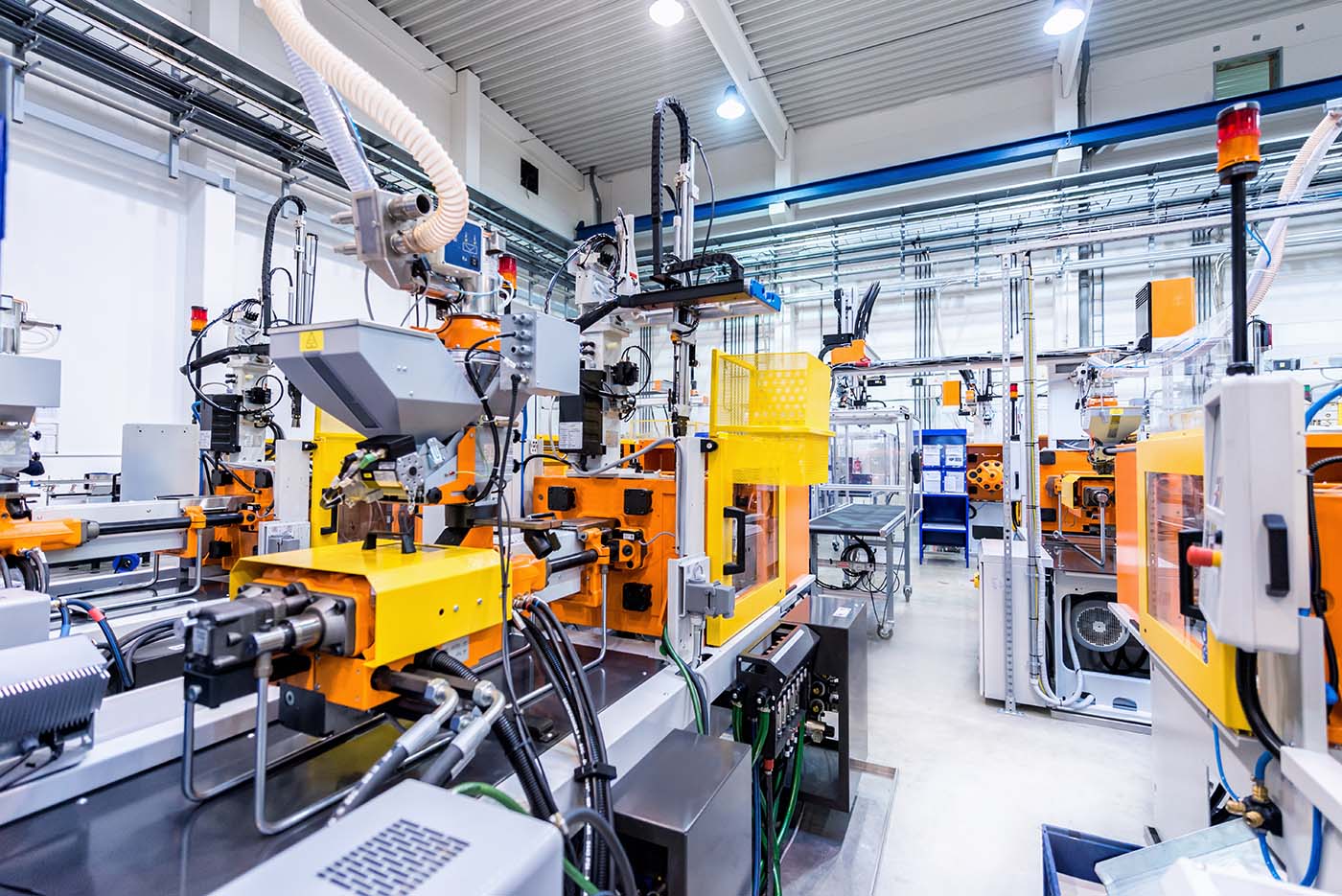
Automation, when integrated with other Industry 4.0 technologies, can greatly increase production capacity and operational efficiency.
Robotics especially make sense for repetitive work that can be dangerous or boring to employees, freeing them up to take on more challenging tasks. For example, robots can take over quality control and auditing functions, inspection of materials and parts, and even inventory management. Drones can fly through warehouses and use radio frequency identification to count products. Data collected through automation can also be used to make more informed business forecasts regarding production and inventory needs.
Benefits of Automation
Companies that invest in automation commonly integrate robotics and vision into their manufacturing and assembly needs, including material handling. Automation benefits include:
- Reduced downtime
- Predictive maintenance
- Improve decision-making
- Real-time analytics
- Modular units or cells for scaling production
- Traceability of parts and materials
“Having real-time data can help manufacturers understand lead times and provide more accurate estimates and timelines,” says Dave Westrom, vice president of business development for MachineMetrics, a company that makes machine monitoring software. “Additionally, automated devices improve repeatability that can improve quality and reduce variability in production. Overall, automated monitoring offers a more predictable model to make business decisions from, while providing transparency for all stakeholders.”
In particular, robotics can help maintain production when the workforce is diminished. For example, during the COVID-19 pandemic, when workers were either ill or socially distanced, manufacturers realized how important robots were in maintaining operations and keeping their workers safe.
“One of the surprise benefits of automation was how far we could spread out employees on the production lines,” says Andy Ahern, plant manager for Food Service Specialties, a company that specializes in making custom tomato and dairy based sauces in Red Wing, MN. “Most of the automation/equipment on our production lines involve machine operators monitoring and replenishing consumables. The design of the lines and layout of machines were conducive to social distancing.”
Pearson’s Candy Company, a mid-sized manufacturer in St. Paul, MN, relies on a hybrid mix of automation and manual labor, which provides it with a competitive advantage over the smaller manual manufacturers. Its automation capabilities also allow it to take on more customized orders that the larger automated manufacturers cannot handle. “We have been updating and automating several key parts of our organization to increase capabilities in order to produce current packaging standards and to expand the ability to incorporate trending flavors and ingredients,” says vice president Alex Allen. “Automated inline monitoring and recipe adjustments usually result in huge improvements for quality and consistency of production.”
Implementing Automation and Robotics
Westrom advises that the first step should be connecting all the plant equipment through the Internet of Things (IoT) and analyzing performance data to see where automation makes the most sense. “You will then have the insight into operational performance across both your equipment and staff to automate processes and drive greater efficiency across the shop floor,” he says.
Automation in equipment manufacturing is often applied in strategic areas such as welding, material handling, pick and place, and other repetitive tasks. According to digital services provider Gray Solutions, a Gray company, companies often look to automation capabilities through robotics, artificial intelligence, and machine learning, among other areas in order to embrace opportunities for increased throughput and productivity, efficiency, and precision. “Digital solutions utilize advanced communications and control abilities to enable real-time, autonomous decisions by production machines and products,” adds Walker Mattox, CEO of Gray Solutions.
However, robotics and automation are not without their challenges.
“It is much easier to train humans on new styles or shapes, with much greater flexibility for creativity,” Allen points out. “Robotic machines can create limitations on the breadth of options, as well as create an inherent minimum economic order size, for tooling or programming adjustments.”
In fact, robots are just as vulnerable to supply chain disruptions as other equipment.
“COVID-19 has highlighted the need to be very diligent regarding reliability and maintenance supply chains for robotic systems,” Allen adds. “Most robotic systems have broad international part sourcing, and we have seen random, sometimes critical components, suddenly become unavailable. Can the supplier truly send you any part overnight? Can technical support be sent immediately?”
Robotics are coming down in price, making them more affordable to small and mid-sized manufacturers allowing for a more even playing field. However, they are still an expensive investment.
“As you research your business case for purchasing, consider all the costs, including installation and configuration,” advises Mark Stevens, a principal with Wipfli LLP’s manufacturing and consulting practice. “Evaluate whether your robot can be easily modified if you need to alter operations in the future. Industrial robots also need sophisticated operation, maintenance, and programming—consider the personnel investment you will need to make to bring in that expertise or re-tool your existing staff to take on the tasks. In addition, you will want to consider the costs to keep your robot and any related IoT-connected devices protected from cyberthreats.”
Manufacturers who turned to automation and robotics to help them get through the COVID-19 pandemic have seen how these and other Industry 4.0 technologies improved the efficiency and productivity of their operations. More automation will also be used in the supply chain, orders and delivery fulfillment, and sensing and communication technologies. Companies that choose not to invest in these technologies will find it challenging to stay competitive with other manufacturers that transition to digital systems of operation that boost quality, profits, and speed to market.
Some opinions expressed in this article may be those of a contributing author and not necessarily Gray.
Related News & Insights
Food & Beverage
Gray Project Receives Manufacturing Innovation Award
Corporate News, Industry
December 04, 2024Advanced Technology, Automation & Controls
Four Use Cases for AI's Growing Role in Manufacturing
Industry
November 25, 2024Data Centers
Gray Expands Reach with Dallas Office
Corporate News
November 14, 2024