Electrostatic “Muscles” Give Robots a Gentle, Human-Like Touch
Robots do a lot of things well, but picking up and holding fragile items is not one of them. So far, each robotic arm’s “hand,” its end effector, must be specifically designed and programmed to manipulate a single shape. Picking up delicate, flat, or deformable objects has been difficult to do.
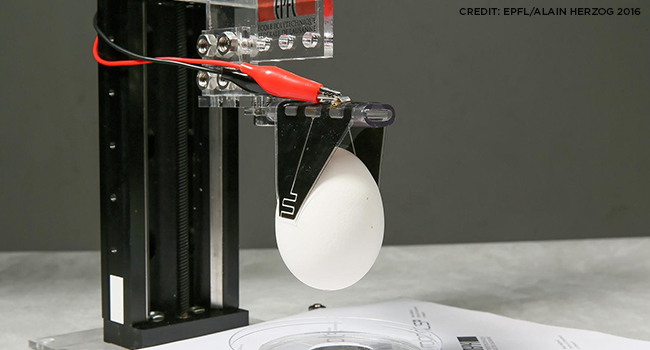
Now, researchers at the Ecole Polytechnique Fédérale in Lausanne, Switzerland (EPFL), while seeking to create artificial muscles, have developed a soft conformable material that can replace the human touch. That has led them to develop an innovative robotic end effector that can pick up a wide range of objects in varying sizes and shapes that can be as much as 80 times the gripper’s weight. Using electroadhesive attraction to mimic the muscle action of a thumb-and-finger grip, small flaps of the soft material are attracted to each other to gently handle tiny or delicate objects.
How soft electronics works
It may sound simple, but the fabrication of the innovative 5-layer electrostatic material is complex. A layer of pre-stretched elastomer lies between two layers of electrodes that are surrounded by two layers of silicone that differ in thickness. That difference means that the membranes curl, but can be made to straighten out when voltage applied to the electrode layers creates an electrostatic field. That causes the flaps to be attracted toward each other. It works much like flexing our finger muscles.
How will this technology be used in manufacturing and other industries?
The researchers are the first to say that there is nothing new about any of the materials or robotic applications in the device. But putting them together in this way is new, and has resulted in this highly adaptable robotic technology. The team envisions the applications to include food handling, capturing debris in outer space, or picking up thin flexible items like sheets of paper. Imaginative manufacturing engineers, however, will soon be using their ingenuity to go far beyond those few ideas. Robotic manufacturers and end users should keep a close watch as the technology makes its way from the lab to the factory floor.
The Swiss are not the only scientists exploring the advantages of softer end effectors. In the U.S., the National Science Foundation has funded work at Empire Robotics to solve similar problems. That has resulted in a spherical robotic “hand” filled with granular material, which can conform to and grip objects of varying shapes and degrees of fragility. The versatile tool has achieved wide notice in the press.
Adaptable robotic tooling can take automation to a new level. Automation is great when manufacturing large volumes of identical items, but less cost-effective for small batch or high variety production, or in uncertain new-product introduction. These new multipurpose tools can handle more complexity as well as a wider range of objects, giving manufacturers new ways to increase productivity.
Karen Wilhelm has worked in the manufacturing industry for 25 years, and blogs at Lean Reflections, which has been named as one of the top ten lean blogs on the web.
- Category:
- Industry
- Manufacturing
Some opinions expressed in this article may be those of a contributing author and not necessarily Gray.
Related News & Insights
Manufacturing
How Technological Advancements Are Changing Modern Manufacturing
GrayWay
Manufacturing
Little Factory Floor Robots That Help, NOT Replace Workers
Industry
November 19, 2014Manufacturing
Google Is Shopping for Robots in New Manufacturing Venture
Industry
March 14, 2014